Mobile Aggregate Crusher and Screening Plant
Introduction to Mobile Aggregate Crusher and Screening Plants
In today’s fast-paced construction and mining industries, mobile aggregate crusher and screening plants are game-changers. These self-contained units combine crushing, screening, and material handling capabilities to process aggregates directly at job sites, eliminating the need for transporting raw materials to fixed plants. This article explores their advantages, operational workflows, and how they optimize productivity across industries.
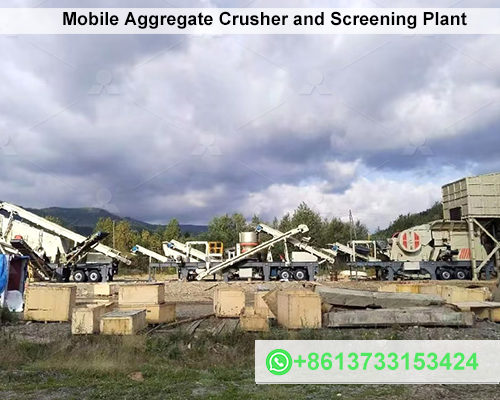
How Mobile Aggregate Crusher and Screening Plants Work
A mobile aggregate crusher and screening plant integrates multiple components into a single, transportable system:
- Feeding: Raw materials (e.g., limestone, granite, recycled concrete) are loaded into the crusher via an excavator or loader.
- Crushing: Primary crusher (jaw or impact) break down large rocks into smaller fragments (50–150 mm).
- Screening: Vibrating screens separate crushed materials into desired sizes (e.g., 0–5 mm sand, 10–20 mm gravel).
- Stockpiling: Conveyors transfer sorted aggregates to storage piles or trucks for immediate use.
Key Components of a Mobile Crushing & Screening System
- Primary Crusher:
- Jaw Crusher: Ideal for hard, abrasive materials (e.g., basalt).
- Impact Crusher: Produces cubical aggregates for asphalt and concrete.
- Secondary/Tertiary Crusher:
- Cone Crusher: Refines materials to precise sizes (5–50 mm).
- Screening Unit:
- Multi-Deck Vibrating Screens: Sort aggregates into 3–4 fractions.
- Mobility Features:
- Track-mounted or wheeled chassis for easy relocation.
- Hybrid (diesel/electric) power options for fuel efficiency.
Advantages of Mobile Aggregate Plants
1. Unmatched Flexibility
- Operate in remote quarries, urban construction sites, or disaster recovery zones.
- Switch between materials (e.g., from limestone to demolition waste) seamlessly.
2. Cost Savings
- Eliminate hauling costs by processing materials on-site.
- Reduce labor expenses with automated controls and minimal setup time.
3. Eco-Friendly Operations
- Lower emissions with Tier 4 Final engines and electric drive options.
- Recycle construction debris into reusable aggregates, reducing landfill waste.
4. Rapid Deployment
- Set up and start crushing in under 30 minutes.
Applications Across Industries
- Road Construction: Produce base layers, asphalt, and drainage materials.
- Mining: Pre-process ores (e.g., gold, copper) before refining.
- Recycling: Convert concrete, bricks, and asphalt into high-quality aggregates.
- Landscaping: Create decorative gravels and sands for parks and gardens.
Top Models of Mobile Aggregate Plants
Model | Crusher Type | Capacity (TPH) | Key Features |
---|---|---|---|
Liming YG938E69 | Jaw Crusher | 50–180 | Compact design, ideal for tight spaces |
Sandvik QI442 HS | Impact Crusher | 200–500 | Doubles as a primary/secondary crusher |
Metso Lokotrack LT220D | Cone Crusher | 150–300 | Hybrid power, advanced automation |
How to Choose the Right Mobile Plant
- Material Hardness:
- For granite or basalt, prioritize jaw crusher with Mn18Cr2 liners.
- For softer limestone, opt for impact crusher.
- Production Goals:
- Small projects: 50–150 TPH models (e.g., Liming YG938E69).
- Large-scale operations: 300–600 TPH setups (e.g., Sandvik QI442).
- Mobility Needs:
- Track-mounted plants for rough terrains.
- Wheeled units for road-legal transport.
Case Study: Quarry Optimization in Texas
A Texas-based quarry replaced its fixed plant with a Liming Y3S1860CS160 Mobile Cone Crusher and Screen, achieving:
- 40% Higher Output: 450 TPH vs. 320 TPH previously.
- 25% Fuel Savings: Hybrid engine reduced diesel consumption.
- Zero Downtime: IoT sensors enabled predictive maintenance.
Maintenance Tips for Longevity
- Daily Checks: Inspect belts, bearings, and hydraulic lines.
- Lubrication: Use high-temperature grease for crusher joints.
- Wear Parts: Replace manganese liners every 1,200–2,000 hours.
FAQs About Mobile Aggregate Plants
Q: What’s the average cost of a mobile crusher and screening plant?
A: Prices range from 200,000forbasicmodelstoover200,000 for basic models to over 200,000forbasicmodelstoover1M for high-capacity systems.
Q: Can these plants handle wet or sticky materials?
A: Yes, but pre-screening or drying may be necessary to prevent clogging.
Q: How do I ensure compliance with environmental regulations?
A: Opt for dust suppression systems and Tier 4 engines to meet EPA standards.
Conclusion
A mobile aggregate crusher and screening plant is a versatile, cost-effective solution for modern material processing needs. By investing in advanced models like Liming’s Y3S series or Sandvik’s QI442, businesses can boost efficiency, reduce environmental impact, and stay competitive in dynamic markets.