Aggregate
Last Updated :2023-08-17 Views:458
Quarry crusher Selection and Design
Selecting and designing a quarry crusher involves several important considerations to ensure efficiency, safety, and cost-effectiveness. Here’s a step-by-step guide to help you with the process:
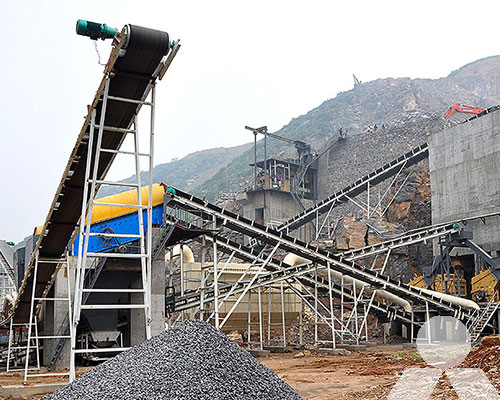
- Understand Quarry Requirements:
- Determine the type of material to be extracted (e.g., limestone, granite, sandstone).
- Identify the required production capacity (tons per hour).
- Consider the final product size specifications.
- Geological Survey:
- Conduct a geological survey of the quarry site to understand the composition and quality of the rock.
- Identify any potential challenges such as hardness, abrasiveness, and presence of moisture.
- Crusher Types:
- Choose the appropriate type of crusher based on the material’s characteristics and the required product specifications. Common types include jaw crushers, cone crushers, impact crushers, and gyratory crushers.
- Capacity Calculation:
- Calculate the required crusher capacity based on the production rate and material characteristics.
- Ensure the crusher has enough capacity to handle peak loads and future expansion.
- Crusher Setting:
- Determine the appropriate crusher settings to achieve the desired product size.
- Consider the trade-off between product size and production rate.
- Feeding Arrangement:
- Design an efficient feeding arrangement to ensure a consistent and controlled feed to the crusher.
- Use apron feeders, vibrating feeders, or other appropriate equipment based on the material properties.
- Safety Considerations:
- Incorporate safety features such as emergency stops, guards, and warning signs.
- Ensure that personnel have safe access to all areas for maintenance and repair.
- Wear Parts Selection:
- Choose wear-resistant materials for crusher components like jaws, liners, and hammers.
- Select the right combination of wear parts to optimize the crusher’s performance and minimize downtime.
- Automation and Control:
- Consider using automation and control systems to monitor and adjust the crusher’s operation for optimal performance.
- Implement remote monitoring and diagnostics for preventive maintenance.
- Environmental Impact:
- Assess the environmental impact of the crusher’s operation and take measures to mitigate dust, noise, and other potential issues.
- Obtain necessary permits and approvals from relevant authorities.
- Installation and Maintenance:
- Plan the installation process, including foundation requirements and equipment positioning.
- Develop a comprehensive maintenance plan to ensure the crusher operates efficiently over its lifespan.
- Cost Analysis:
- Evaluate the initial cost, operational expenses, and potential ROI of the chosen crusher.
- Consider factors like energy consumption, maintenance costs, and expected lifespan.
- Supplier Selection:
- Choose a reputable and experienced supplier with a track record of providing reliable crushers and excellent customer support.
- Testing and Optimization:
- Conduct initial testing to validate the crusher’s performance and adjust settings if necessary.
- Continuously monitor and optimize the crusher’s operation for maximum efficiency.
Remember that every quarry is unique, so the selection and design process should be tailored to your specific requirements and conditions. It’s advisable to consult with experienced engineers and industry experts to ensure the best possible outcome.