Feldspar ore crushing equipment and beneficiation processes
Feldspar is a silicate mineral containing alkali metals such as potassium, sodium, calcium, and small amounts of barium. Pure and single feldspar is rarely found in nature, often occurring in solid solution with similar minerals. In industrial applications, feldspar is commonly used as a flux in ceramics, glass, and other materials. With the increasing demand for high-purity and low-iron feldspar raw materials in the production of high-end glass and ceramics, the requirements for feldspar purification have become increasingly stringent. In the following, we will introduce the methods of feldspar ore dressing (purification process), the process flow of feldspar ore dressing, and the equipment used in feldspar ore dressing.
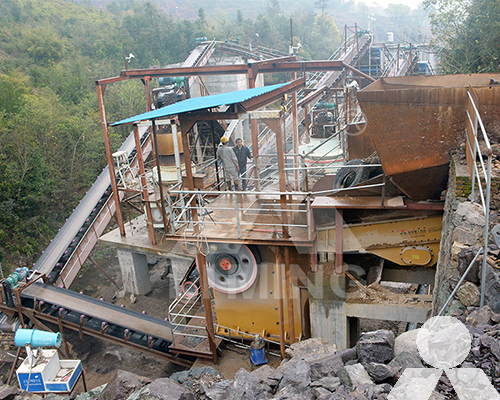
Depending on the type of mineral deposit and the nature of the ore, the mineral processing processes for each feldspar are also different. Based on different mine properties and plant dressing needs, Liming Heavy Industry will tailor a scientific and reasonable feldspar dressing process for each feldspar dressing plant. Common process flows are as follows:
- Hand selection-crushing-grinding-grading process
This process is generally suitable for selecting high-quality feldspar produced in pegmatite. The mined feldspar ore can be manually sorted first, except for the feldspar ore with high concentrate content. The remaining minerals are sent to the crushing stage for coarse and fine crushing operations, and then enter the grinding and classification operation, using rods. The mill and spiral classifier form a closed circuit.
- Crushing-grinding-grading-flotation process flow
This process is mostly used to select feldspar minerals in weathered granite. Among the flotation processes, one type of flotation is used to remove iron and mica, and the other type of flotation is used to separate quartz and feldspar.
Method for removing iron and mica by feldspar flotation: in a weakly alkaline medium, use sodium carbonate as a regulator, water glass as an inhibitor, and saponified oleic acid as a collector; in a weakly acidic medium, use sulfuric acid as a regulator, Dodecaamine is used as collector and frother to remove mica impurities by flotation method.
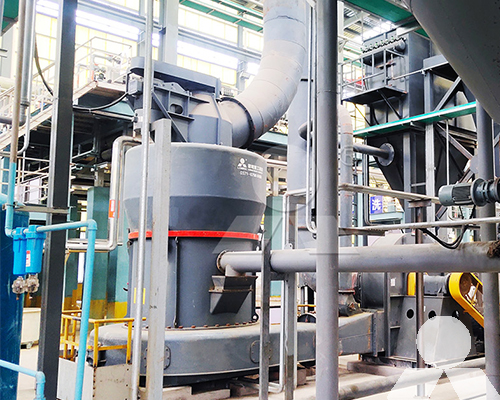
Feldspar quartz flotation separation methods: can be divided into three types: hydrofluoric acid method, fluorine-free and acid method, and fluorine-free and acid-free method. Among them, the hydrofluoric acid method uses hydrofluoric acid or fluoride as the activator of feldspar. In a strongly acidic medium, amines and other cationic collectors are used to preferentially float out the feldspar; the fluorine-free acid method uses strong acidic media ( In a medium with a pH value of 2 to 3, amines and petroleum sulfonates are used as anionic and cationic mixed collectors to float out feldspar first; the fluorine-free and acid-free method uses anionic and cationic mixed collectors to float and separate quartz.
- Crushing-grinding-screening-magnetic separation process flow
This process is generally suitable for selecting feldspar (containing mica and sometimes iron) in fine-crystalline rocks. The minerals are first coarsely and mediumly crushed using a crusher to -6mm particles, and then sent to a ball mill for grinding. Grind to 60~200 mesh, and then send it to a drum screen for screening. After screening, the minerals enter a magnetic separator for magnetic separation to remove mica and iron impurities.
Recommended feldspar mineral processing equipment: wet overflow ball mill, linear vibrating screen, permanent magnet magnetic separator
- Water washing-rod mill-gravity-flotation process flow
This type of process is suitable for processing feldspathic sand minerals. The process flow is as follows: after the raw ore is crushed in two stages of open circuit, it is directly fed into the rod mill and screening machine to form a closed-circuit grinding system, and the undersized material enters the spiral chute and shaker. bed to remove minerals such as rutile, and then pass through a permanent magnet magnetic separator to further remove iron. The product after iron removal uses a flotation process to remove impurities such as chlorite.
Recommended feldspar mineral processing equipment: circular vibrating screen, spiral chute, jjf flotation machine
- Rod mill-magnetic separation-flotation process flow
The process flow is that after two stages of open-circuit crushing, the raw ore enters the rod mill and vibrating screen to form a closed-circuit grinding system. The undersized material is removed by a high-gradient magnetic separator to remove iron. After the fine mud is removed from the product, it is first processed into a coarse and second fine flotation to recover mica, followed by fluorine-free flotation to separate feldspar from quartz.