Limestone Crushing System
Limestone is one of the most widely used materials in construction, mining, and industrial applications. It is essential for producing cement, aggregates, and lime, and is used in industries ranging from steelmaking to agriculture. To process limestone for these applications, an efficient limestone crushing system is required. This article explores the key components and stages involved in a typical limestone crushing system, providing an overview of how the system works.
1. Overview of Limestone Crushing System
A limestone crushing system is designed to take large pieces of raw limestone, reduce their size, and prepare them for further processing. The process generally involves three stages: primary crushing, secondary crushing, and sometimes tertiary crushing, depending on the desired product size. The output is usually sorted into various sizes, used for aggregates, concrete, cement, or other industrial purposes.
2. Key Components of a Limestone Crushing System
The typical limestone crushing system consists of the following components:
- Hopper and Feeder
- Primary Crusher
- Secondary Crusher
- Screening Equipment
- Conveyor System
- Dust Control System
2.1 Hopper and Feeder
The system begins with a hopper, which stores raw limestone transported from the quarry. The limestone is then fed into the crushing system through a vibrating feeder, which ensures a continuous and controlled flow of material to the primary crusher. The feeder also helps remove smaller particles and debris, preventing unnecessary wear on the crusher.
2.2 Primary Crusher
The primary crusher is responsible for the initial reduction of the limestone rock. This stage breaks down large limestone boulders into smaller, more manageable pieces. The two most common types of primary crusher used in limestone crushing systems are:
- Jaw Crusher: A jaw crusher is used for the initial reduction of hard, abrasive limestone rocks. It works by compressing the rock between two jaw plates—one fixed and one moving—crushing the material into smaller chunks.
- Gyratory Crusher: For higher capacity operations, a gyratory crusher might be preferred. It has a larger crushing chamber and can handle larger limestone blocks.
2.3 Secondary Crusher
The secondary crusher further reduces the size of the limestone to meet specific size requirements for the final product. Secondary crusher typically include:
- Impact Crusher: This crusher is commonly used in limestone crushing systems due to its ability to handle soft to medium-hard materials. It works by using high-speed rotors that throw the rock against hard surfaces, breaking it into smaller fragments. Impact crusher is often used when the desired product size is relatively small and well-shaped aggregates are required.
- Cone Crusher: In some systems, a cone crusher is used for secondary crushing. Cone crusher apply a compressive force to crush the material and are better suited for harder types of limestone.
2.4 Screening Equipment
After the secondary crushing stage, the material is passed through vibrating screens that separate it into different size fractions. The screens have multiple decks with various sized apertures to classify the crushed limestone into specific grades or particle sizes required for different applications (e.g., aggregates, cement production).
- Vibrating Screens: These are used to classify the material by size. The oversize material is sent back to the crusher for reprocessing, while the correctly sized product moves forward for further use or storage.
2.5 Conveyor System
The conveyor system is responsible for transporting the crushed material between different stages of the process. Belt conveyors are commonly used to move the limestone from one part of the crushing system to another, ensuring efficient material flow and minimizing manual handling.
- Belt Conveyors: These are used to carry material from the primary crusher to the secondary crusher, from the screen to stockpiles, or from crushing stations to processing areas.
2.6 Dust Control System
Crushing limestone generates significant amounts of dust, which needs to be controlled to maintain a safe and environmentally compliant operation. Dust control systems are integral to modern crushing systems.
- Dust Suppression: Water sprays are used at various stages to suppress dust at the source.
- Dust Collection Systems: These systems capture dust using filters or cyclone separators, preventing it from escaping into the environment.
3. Stages in Limestone Crushing
A limestone crushing system operates in several key stages, each with its specific function and objective:
3.1 Primary Crushing Stage
- The limestone is fed from the hopper to the primary crusher, typically a jaw or gyratory crusher, where it is reduced to a size suitable for secondary crushing.
- This stage typically reduces the limestone size to between 200 mm and 300 mm, depending on the crusher settings and material characteristics.
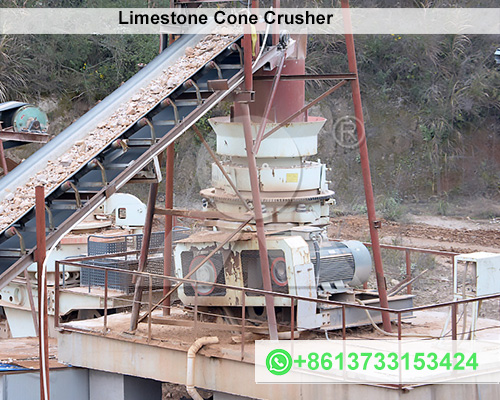
3.2 Secondary Crushing Stage
- The output from the primary crusher is further processed in the secondary crusher, which reduces the material to a size of about 50 mm to 100 mm. Secondary crusher such as impact crusher or cone crusher is used for this purpose.
- This stage ensures the limestone is further reduced to sizes appropriate for final screening or direct use.
3.3 Screening and Classification Stage
- After secondary crushing, the limestone is screened to separate the material into various size fractions. The oversize material may be sent back to the secondary or tertiary crusher for further reduction.
- The correctly sized limestone is then conveyed to stockpiles, silos, or transported for immediate use in production processes such as cement manufacturing.
3.4 Optional Tertiary Crushing Stage
- In some cases, tertiary crushing is required when the limestone must be crushed into finer materials for specific applications, such as for the production of fine aggregates or in industries requiring extremely fine limestone powder.
- Tertiary crusher, such as vertical shaft impact crusher (VSI), can be used to produce these finer materials.
4. Automation and Control in Limestone Crushing Systems
Modern limestone crushing systems are often equipped with automated controls that monitor and adjust the operation in real-time to optimize efficiency and product quality. Key technologies include:
- Programmable Logic Controllers (PLC): PLC systems control the start/stop sequences of different equipment, monitor material flow, and adjust crusher settings based on the production requirements.
- Supervisory Control and Data Acquisition (SCADA): SCADA systems provide operators with a high-level overview of the crushing process, allowing them to monitor key performance indicators (KPIs) such as throughput, crusher settings, and material quality.
5. Conclusion
A limestone crushing system is an essential part of the production process for a wide range of construction and industrial materials. The system’s efficiency, design, and choice of equipment directly impact the quality and cost-effectiveness of the final products. By selecting the appropriate crusher, screens, conveyors, and dust control systems, operators can ensure that their limestone crushing operations are optimized for maximum productivity and minimal environmental impact.