Capacity and energy of primary gyratory crusher
Primary gyratory crusher play a pivotal role in the mining and aggregate industries, where they are used to crush large quantities of raw materials, such as rocks and ores, into smaller, manageable sizes. The capacity and energy consumption of these crusher are critical factors that influence their efficiency and the overall productivity of mining operations. In this article, we will explore the key aspects of primary gyratory crusher, focusing on their capacity, energy requirements, and the factors that affect their performance.
Understanding Primary Gyratory Crusher
A gyratory crusher is a large crushing machine that consists of a concave surface and a conical head, both of which are typically lined with manganese steel. The material is fed into the top of the crusher, where it is crushed between the rotating head and the concave. The crusher’s design allows for continuous operation, which makes it highly suitable for high-capacity operations, such as large-scale mining or quarrying.
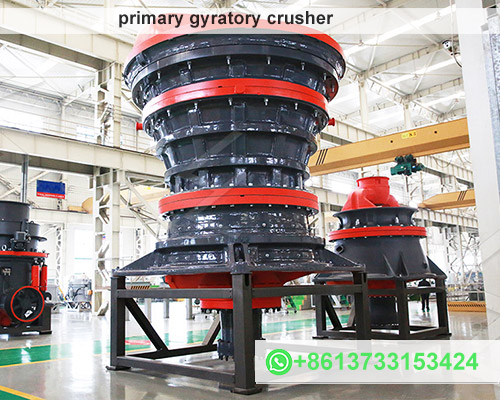
Primary gyratory crusher are designed to handle the initial phase of crushing, reducing the size of run-of-mine (ROM) material to a level that can be processed further by secondary crusher or mills. The size of the gyratory crusher, often indicated by the feed opening and mantle diameter, directly correlates with its capacity and energy consumption.
Capacity of Primary Gyratory Crusher
The capacity of a gyratory crusher refers to the maximum amount of material it can process in a given time frame, typically measured in tons per hour (tph). Several factors influence the capacity of a gyratory crusher:
- Feed Size: The larger the feed size, the more material the crusher can process at a time. However, oversized material may lead to blockages or require more energy to crush.
- Crusher Dimensions: The size of the crusher’s mantle and concave chamber determines how much material can be accommodated at any given time. Larger crusher generally have higher capacities.
- Material Characteristics: The hardness, density, and moisture content of the material being processed impact the capacity. Harder materials may require more time and energy to crush, reducing throughput.
- Crushing Chamber Design: The geometry and design of the crushing chamber, as well as the profile of the liners, affect how efficiently the material is processed.
- Crusher Speed and Stroke: The speed at which the gyratory head rotates and the stroke (the distance between the mantle and the concave) can influence both the crusher’s capacity and the size of the output material.
Modern gyratory crusher are capable of handling up to thousands of tons of material per hour, making them essential for high-production environments.
Energy Consumption in Gyratory Crusher
Energy efficiency is a key concern in the mining industry, where crushing operations account for a significant portion of total energy usage. The energy consumption of a primary gyratory crusher is influenced by various factors:
- Crushing Power: The power required to crush the material depends on its hardness and the crusher’s design. More energy is needed to break tougher or more abrasive materials.
- Crusher Efficiency: A more efficient crusher uses less energy to achieve the same level of crushing. This is often achieved through improvements in chamber design, mantle shape, and operating conditions.
- Feed Rate: The rate at which material is fed into the crusher can affect its energy consumption. Overfeeding the crusher can lead to increased wear and energy usage, while underfeeding may result in wasted energy and reduced productivity.
- Material Compression: The energy consumed during the crushing process is also affected by how much the material is compressed between the mantle and concave. More compression requires more energy, but it may result in finer material, reducing the need for additional crushing.
- Operational Settings: Adjusting parameters like the crusher’s operating speed, stroke, and eccentric throw can optimize energy usage. Lower speeds and reduced strokes may conserve energy but decrease capacity.
Balancing Capacity and Energy Efficiency
Balancing the capacity of a primary gyratory crusher with energy efficiency is a key challenge for mining operations. High capacity often demands more energy, but technological advancements in crusher design and materials have made it possible to improve energy efficiency without sacrificing throughput.
One way to achieve this balance is through the use of automation and control systems. Modern crusher are equipped with sensors and monitoring systems that can adjust the crusher’s settings in real-time based on the feed conditions and energy consumption. This not only ensures optimal performance but also reduces energy waste.
Another approach to improving energy efficiency is the use of variable frequency drives (VFDs) on the crusher’s motors. VFDs allow for precise control of the crusher’s speed, enabling operators to fine-tune the machine’s performance for different materials and conditions.
The capacity and energy consumption of primary gyratory crusher are crucial aspects that directly affect the efficiency of mining and aggregate operations. By understanding the factors that influence these parameters and implementing advanced technologies to optimize performance, companies can reduce energy costs, increase productivity, and minimize the environmental impact of their operations. As the demand for higher efficiency continues to grow, innovations in crusher design and operation will play a critical role in meeting the industry’s evolving needs.