Cone Crusher Lubrication Systems Schematic Drawing
Introduction
Cone crusher is essential components in the mining and aggregate industries, responsible for reducing large rocks into smaller, manageable sizes. Proper lubrication is critical for ensuring the optimal performance and longevity of these machines. This article provides an overview of cone crusher lubrication systems, including a schematic drawing that illustrates their components and functions.
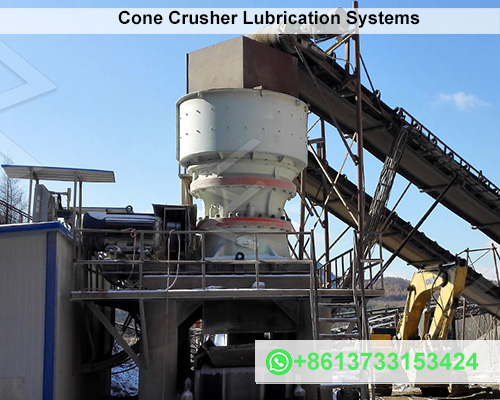
Importance of Lubrication in Cone Crusher
Lubrication systems in cone crusher serve multiple purposes:
- Cooling: Lubrication helps dissipate heat generated during the crushing process, preventing overheating and extending the lifespan of the crusher components.
- Friction Reduction: Proper lubrication reduces friction between moving parts, decreasing wear and tear.
- Sealing: Lubricants can act as seals to prevent contaminants from entering the system, ensuring cleaner operation.
- Protection: Lubricants form a protective film on metal surfaces, minimizing corrosion and damage.
Components of a Cone Crusher Lubrication System
A typical cone crusher lubrication system consists of the following components:
- Oil Reservoir: Holds the lubrication oil, allowing for circulation throughout the system.
- Oil Pump: Circulates oil from the reservoir to the crusher’s lubrication points.
- Filters: Remove impurities from the oil to ensure it remains clean and effective.
- Cooling System: Often includes a heat exchanger or cooler to maintain optimal oil temperatures.
- Pressure Relief Valve: Protects the system from excessive pressure by releasing excess oil.
- Lubrication Lines: Channels through which oil flows to various components of the crusher.
- Oil Temperature and Pressure Gauges: Monitor the oil’s condition, ensuring it operates within specified parameters.
Schematic Drawing of Cone Crusher Lubrication System
The following schematic drawing illustrates a typical cone crusher lubrication system:
Operation of the Lubrication System
- Oil Circulation: The oil pump draws lubricant from the oil reservoir and pumps it through the filters, removing impurities.
- Cooling: After filtering, the oil flows through the cooling system, where it is cooled before entering the crusher.
- Lubrication: The cooled oil is directed to critical lubrication points within the cone crusher, including bearings and gears.
- Monitoring: Pressure and temperature gauges continuously monitor the oil’s condition. If readings exceed set limits, adjustments can be made to ensure optimal performance.
- Return Flow: After lubricating the components, the oil returns to the reservoir, where it can be re-circulated.
Conclusion
A well-designed lubrication system is crucial for the effective operation of cone crusher. It enhances performance, extends equipment life, and minimizes downtime due to maintenance issues. Understanding the schematic drawing and components of these systems helps operators and engineers maintain their equipment more effectively, ensuring reliable and efficient crushing operations. By prioritizing proper lubrication practices, users can achieve optimal results in their mining and aggregate processes.