Sand Crusher Technical Specifications
Sand crusher play a vital role in producing high-quality manufactured sand for a range of applications, from construction to glass production and industrial manufacturing. By breaking down large aggregates or rocks into smaller particles, sand crusher provide a controlled particle shape, size, and consistency. When selecting a sand crusher, understanding its technical specifications is essential to ensure it meets the production requirements and aligns with industry standards. This article provides an overview of sand crusher technical specifications, focusing on types, components, capabilities, and applications.
1. Importance of Sand Crusher Specifications
The technical specifications of a sand crusher determine its suitability for specific applications. Factors such as crusher type, rotor speed, capacity, power requirements, particle size control, and durability play critical roles in selecting the right sand crusher for different projects. Properly chosen specifications ensure that the crusher can operate efficiently, produce uniform sand quality, and contribute to sustainable production practices by reducing waste.
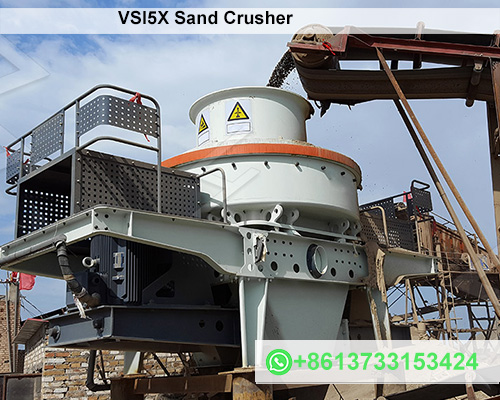
2. Types of Sand Crusher and Their Specifications
There are several types of sand crusher, each with unique specifications that cater to different needs:
- Vertical Shaft Impact (VSI) Crusher: VSI crusher is ideal for producing sand with precise shape and size. They use high-speed rotors to throw the rock against hard surfaces or anvils, creating a finely graded and cubical particle.
- Horizontal Shaft Impact (HSI) Crusher: HSIs are used for softer or less abrasive materials. They utilize horizontal rotors that crush materials through impact with bars or hammers.
- Cone Crusher: Although not exclusively used for sand production, cone crusher provide an alternative for producing finely graded sand from specific materials, especially in secondary or tertiary crushing stages.
- Roll Crusher: Roll crusher crush materials between two rotating cylinders, producing fine particles without creating excessive fines.
Each type offers different technical specifications to suit various industries. Below is a breakdown of key specifications.
3. Key Technical Specifications of Sand Crusher
a) Feed Size and Reduction Ratio
- Feed Size: The feed size is the maximum dimension of material the crusher can accept. VSI crusher generally handle feed sizes between 30–50 mm, while HSI crusher can manage slightly larger sizes, depending on their design.
- Reduction Ratio: The reduction ratio indicates how much the crusher can reduce material size. VSI and HSI crusher typically have reduction ratios of 10:1, ensuring that large rocks are broken down into fine sand particles suitable for different applications.
b) Capacity and Throughput
- Capacity: Capacity refers to the amount of material a sand crusher can process per hour. Capacities vary widely across crusher types, with smaller VSI crusher handling up to 50 tons per hour, while larger, industrial crusher can process several hundred tons per hour.
- Throughput: Throughput determines how much material can pass through the crusher within a given period. For example, VSI crusher provide consistent throughput levels, which is important for maintaining uniform sand quality in high-demand operations.
c) Rotor Speed and Power Requirements
- Rotor Speed: The rotor speed in a VSI crusher, typically measured in revolutions per minute (RPM), greatly affects the particle shape and size of the produced sand. Higher speeds (up to 2500 RPM) allow for finer, more cubical sand, which is ideal for construction and glass manufacturing.
- Power Requirements: Power consumption varies depending on the crusher’s capacity, size, and design. Smaller crusher may operate on 50–75 kW, while larger industrial models require upwards of 300 kW. Energy efficiency is a key consideration, as more efficient machines reduce operational costs and environmental impact.
d) Particle Size Control and Gradation
- Particle Size Control: Sand crusher offer mechanisms for controlling the size of the output particles. VSI crusher achieve this with adjustable rotor speed, which allows for fine-tuning the particle shape and size. HSI crusher provide similar control through adjustment of the hammer or bar spacing.
- Gradation: Gradation is the distribution of particle sizes within the sand output. Certain industries, like concrete production, require specific gradation to ensure stability and strength. VSI crusher can produce sand with uniform gradation, making them preferable for applications requiring strict particle size distribution.
e) Build Quality and Durability
- Wear-Resistant Parts: High-quality sand crusher is equipped with wear-resistant parts like hardened alloy anvils, tungsten carbide tips, and durable liners. These materials enhance durability and reduce maintenance costs.
- Structure and Frame: The structural integrity of the crusher is important for long-term use in high-demand environments. Steel frames and reinforced designs reduce vibrations and extend the crusher’s operational life, which is crucial for reliability.
4. Additional Features of Sand Crusher
Modern sand crusher come equipped with advanced features to enhance performance and usability:
- Automation and Monitoring Systems: Automated control systems allow operators to monitor rotor speed, load, and wear in real time, adjusting parameters to maintain consistent sand quality.
- Dust and Noise Reduction: Some crusher include dust suppression systems and noise reduction features to comply with environmental regulations.
- Adjustable Output Controls: Adjustable controls enable operators to vary the size and shape of the sand produced, making the crusher adaptable to different industry requirements.
5. Industry Applications of Sand Crusher
Due to their versatility and efficiency, sand crusher is widely used across multiple industries:
- Construction: High-quality manufactured sand is essential for making concrete and mortar, which require sand with consistent gradation and shape.
- Glass Production: The glass industry demands high-purity sand with specific particle sizes to achieve clarity and strength in glass products. VSI crusher is particularly suitable here, as they produce fine, uniform sand.
- Mining and Mineral Processing: Sand crusher is also used to produce fine particles from ores and minerals, reducing large boulders to smaller grains that can be further processed.
- Electronics and Silicon Production: In producing silicon-based products, sand crusher help produce highly refined sand with minimal impurities, a prerequisite for electronics manufacturing.
6. Future Developments in Sand Crusher Technology
The demand for more efficient and environmentally friendly sand crusher is driving innovation in the industry. Researchers are exploring ways to integrate artificial intelligence into crusher for predictive maintenance, allowing for real-time monitoring and optimization. Additionally, hybrid crusher, which use a combination of mechanical and pneumatic systems, are emerging to reduce energy consumption further.
Conclusion
Sand crusher technical specifications are essential for selecting the right machine for specific industrial applications. Key specifications like feed size, reduction ratio, rotor speed, and particle size control play a major role in the performance and efficiency of these machines. German and other leading manufacturers are pushing the envelope, providing solutions that balance high capacity with precision and sustainability. By understanding these specifications, industries can make informed choices that meet production demands and environmental goals, contributing to long-term operational success.