Concrete crusher description for concrete recycling
Concrete crusher is a heavy-duty machine designed to break down concrete into smaller pieces for the purpose of recycling. It plays a crucial role in the process of concrete recycling by efficiently reducing the size of concrete rubble, such as demolished buildings, bridges, and other structures, into manageable and reusable aggregates.
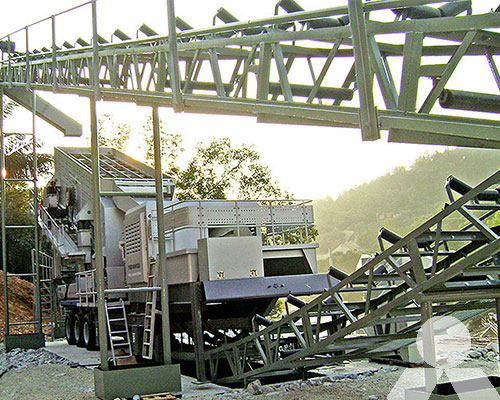
Here is a detailed description of a typical concrete crusher used for concrete recycling:
1. Structure and Components: A concrete crusher is typically mounted on a wheeled or tracked chassis, allowing it to be easily transported to the demolition site. It consists of various components that work together to process concrete rubble:
- Jaw Crusher or Impact Crusher: These are the primary crushing mechanisms responsible for breaking down the larger pieces of concrete into smaller chunks. A jaw crusher uses a stationary jaw and a moving jaw to apply pressure and crush the concrete, while an impact crusher uses hammers or blow bars to strike the material and break it apart.
- Feed Hopper: This is where the concrete rubble is loaded into the crusher for processing. It ensures a steady and controlled flow of material into the crushing chamber.
- Conveyor Belts: After the concrete is crushed, conveyor belts are used to transport the processed material away from the crusher. These belts move the aggregates to the next stage of the recycling process or to a stockpile for future use.
2. Crushing Process: The concrete recycling process using a crusher involves the following steps:
- Loading: Demolished concrete pieces are loaded into the feed hopper of the crusher either manually or using heavy machinery.
- Crushing: The concrete is fed into the crusher’s crushing chamber, where the primary crushing mechanism (jaw or impact) applies force to break down the material into smaller pieces.
- Sizing: The crushed concrete pieces are sorted by size using screens or grates, separating them into different grades of aggregates. These aggregates can include various sizes of crushed concrete ranging from fine particles to larger chunks.
- Separation of Rebar and Contaminants: Many concrete structures contain reinforcing steel bars (rebar). Magnetic separators or other devices may be used to separate and remove rebar and other contaminants from the crushed material.
- Output: The processed concrete aggregates are then conveyed away from the crusher for further processing or storage.
3. Benefits of Concrete Recycling: Concrete recycling offers several environmental and economic benefits:
- Resource Conservation: Recycling concrete reduces the need for new aggregates, helping conserve natural resources like gravel and sand.
- Energy Savings: Processing recycled concrete requires less energy compared to producing new aggregates from raw materials.
- Reduced Landfill Waste: Recycling concrete reduces the amount of construction waste ending up in landfills.
- Cost Savings: Using recycled aggregates in construction projects can lead to cost savings.
Overall, a concrete crusher is a vital tool in the concrete recycling process, helping to reduce waste, conserve resources, and contribute to sustainable construction practices.