Roller mill for crushing refractory material
Refractory materials are essential in various industrial processes where high temperatures and extreme conditions are prevalent, such as in metallurgy, cement production, and glass manufacturing. These materials must possess exceptional heat resistance and durability to withstand intense thermal stress. To prepare these refractory materials for use, they often require size reduction, which is efficiently achieved through the use of roller mills. In this article, we will explore the role of roller mills in crushing refractory materials.
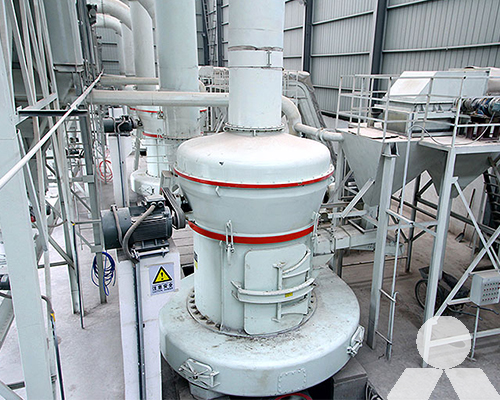
The Role of Refractory Materials
Refractory materials play a crucial role in industries that involve high-temperature processes. They are used to line furnaces, kilns, and reactors, providing insulation and protection against extreme heat, chemical corrosion, and mechanical wear. Common refractory materials include various types of bricks, castables, and monolithic refractories, each designed for specific applications.
The Need for Size Reduction
Before refractory materials can be used effectively, they often need to be crushed and ground into smaller, uniform particles. This size reduction process improves the material’s handling, mixing, and application properties. It also enhances the packing density, allowing for better heat transfer and insulation within the lining of industrial equipment.
The Roller Mill Solution
Roller mills have proven to be highly effective in crushing and grinding refractory materials due to their unique design and operational advantages. A roller mill consists of two or more rotating rollers that crush and grind materials between them. The key features that make roller mills suitable for processing refractory materials are:
- High Efficiency: Roller mills can achieve high crushing efficiency because they apply compressive forces evenly across the material, resulting in a uniform reduction in particle size.
- Adjustable Fineness: The gap between the rollers can be adjusted to control the final particle size, allowing for precise customization to meet specific application requirements.
- Minimal Heat Generation: Roller mills generate less heat compared to other grinding methods, which is crucial for preserving the integrity of refractory materials.
- Low Maintenance: Roller mills are robust and require minimal maintenance, making them a cost-effective choice for refractory material processing.
- Versatility: Roller mills can handle a wide range of refractory materials, including dense bricks, castables, and aggregates.
Applications of Roller Mills in Refractory Industry
- Crushing Refractory Bricks: Roller mills can reduce refractory bricks to the desired size, making them suitable for lining furnaces and kilns.
- Grinding Castables: Roller mills are used to grind castable refractory materials into fine powders, improving their flowability and ensuring uniform distribution during installation.
- Preparing Aggregates: Roller mills are employed to crush and refine refractory aggregates, which are used as raw materials in the production of monolithic refractories.
Roller mills are indispensable tools in the refractory industry, providing efficient and precise size reduction of refractory materials. Their ability to maintain material integrity, control particle size, and minimize heat generation makes them an ideal choice for processing refractory bricks, castables, and aggregates. As industries continue to rely on high-temperature processes, roller mills will remain a crucial component in the production of reliable and durable refractory linings.