320 Mesh Ore Crusher For Fine Ore Processing
Ore crushing plays a pivotal role in mining and material processing industries. When fine-grade ore materials are needed, a 320-mesh ore crusher is an invaluable tool. This article delves into the specifics of this type of crusher, its applications, benefits, and operational considerations.
What is a 320 Mesh Ore Crusher?
A 320 mesh ore crusher is a machine designed to pulverize raw ore into particles fine enough to pass through a 320-mesh sieve. In mesh terms, this translates to particles with diameters of approximately 44 microns. This level of granularity is critical for certain applications in metallurgy, pharmaceuticals, ceramics, and construction materials.
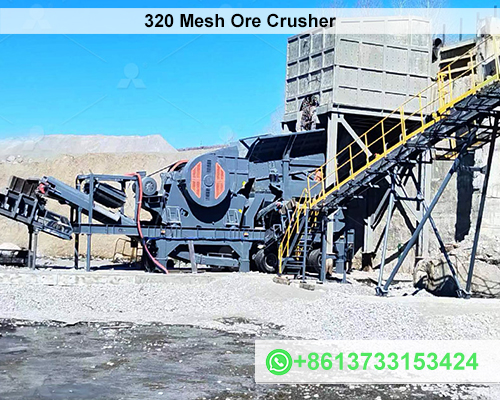
The term “mesh” refers to the number of openings per inch in a sieve screen. A 320-mesh sieve has 320 openings per linear inch, ensuring that crushed material achieves a very fine consistency.
Applications of a 320 Mesh Ore Crusher
- Metallurgy and Mining
Fine ore crushing is essential for metal extraction processes such as flotation, smelting, and leaching. A 320-mesh crusher ensures optimal liberation of valuable minerals from gangue materials. - Construction Materials
Pulverized ore is used in producing cement, glass, and ceramics, where precise particle size distribution enhances product strength and quality. - Chemical Industry
The fine material is utilized as a feedstock for chemical reactions, including catalysts or pigments requiring ultra-fine powders. - Pharmaceuticals
Certain ores processed to 320 mesh are used in medical applications, such as creating biocompatible materials or active pharmaceutical ingredients.
Features of a 320 Mesh Ore Crusher
- High Precision Grinding
These crusher is equipped with advanced mechanisms like roller mills or high-speed impact mills to ensure uniform particle size. - Robust Construction
Designed to handle various ore types, from soft limestone to hard quartzite. - Adjustable Settings
Allows operators to fine-tune the machine for different mesh sizes, ensuring versatility in applications. - Energy Efficiency
Modern 320 mesh crusher is engineered to minimize energy consumption without compromising output quality. - Durable Wear Parts
Materials like tungsten carbide or hardened steel ensure longevity, even under abrasive conditions.
Operational Considerations
- Feed Material Characteristics
- Hardness: Softer ores are easier to process; harder ores may require pre-treatment like jaw crushing.
- Moisture Content: High moisture can clog the mesh and reduce efficiency.
- Maintenance
Regular cleaning and replacement of wear parts, such as screens and grinding elements, are crucial to maintain performance. - Safety Measures
Adequate shielding, dust extraction systems, and vibration isolation are necessary for operator safety. - Energy Optimization
Implementing variable speed drives and automation can improve energy efficiency and throughput.
Advantages of Using a 320 Mesh Ore Crusher
- Enhanced Recovery Rates
By finely grinding ores, valuable minerals are better liberated, boosting downstream processing efficiency. - Versatility
Suitable for a wide range of ore types and industrial applications. - Improved Product Quality
Uniform particle size distribution ensures consistency in end-product performance. - Cost Efficiency
Reduces the need for multiple crushing and grinding stages, saving energy and operational costs.
Conclusion
A 320 mesh ore crusher is an indispensable tool for industries requiring ultra-fine ore processing. By delivering precise particle size distribution, these machines enhance product quality, streamline processes, and reduce costs. Whether you are in mining, construction, or manufacturing, understanding the capabilities and operational parameters of a 320 mesh crusher can optimize your operations and ensure superior results.
Investing in high-quality equipment and adhering to best practices in maintenance and operation can significantly enhance efficiency and longevity.