Jaw Crusher Working Diagram
Introduction to Jaw crusher
Jaw crusher is essential machines in mining, construction, and recycling industries, designed to crush hard materials like granite, basalt, and concrete. A jaw crusher diagram visually explains the structure and operation of these machines, making it easier to optimize performance and troubleshoot issues. This article breaks down jaw crusher components, working principles, and applications with clear diagrams and actionable insights.
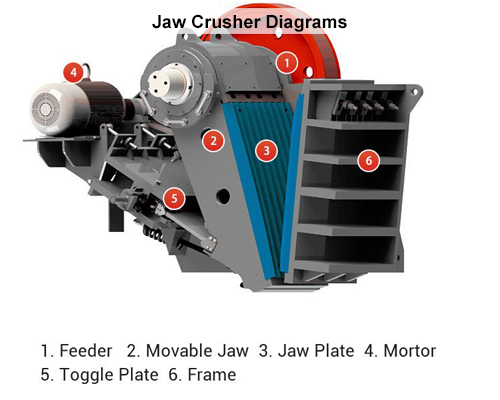
Key Components of a Jaw Crusher (Labeled Diagram)
1. Fixed Jaw Plate
- The stationary surface where material is crushed.
- Made of high manganese steel (e.g., Mn14Cr2) for durability.
2. Movable Jaw Plate
- Oscillates against the fixed jaw, applying compressive force to break materials.
- Driven by an eccentric shaft connected to a motor.
3. Eccentric Shaft
- Transfers rotational energy from the motor to the movable jaw.
- Precision-balanced to minimize vibration.
4. Toggle Plate
- Acts as a safety mechanism to protect the crusher from overloads.
- Replaces easily if damaged.
5. Flywheel
- Stores energy to ensure smooth operation during load fluctuations.
6. Adjusting Wedge
- Allows operators to modify the discharge opening size (e.g., 50–150 mm).
How a Jaw Crusher Works:Step-by-Step Diagram
- Feeding:Raw material enters the crushing chamber through the vibrating feeder.
- Compression:The movable jaw moves toward the fixed jaw, crushing the material.
- Discharge:Crushed material exits through the bottom discharge gap.
Types of Jaw crusher (Schematic Comparison)
1. Single Toggle Jaw Crusher
- Diagram Feature:A single toggle plate connects the movable jaw to the eccentric shaft.
- Advantages:Simpler design, lower maintenance costs.
- Applications:Medium-hard to hard materials (e.g., granite, iron ore).
2. Double Toggle Jaw Crusher
- Diagram Feature:Two toggle plates for enhanced mechanical leverage.
- Advantages:Higher crushing force, ideal for abrasive materials.
- Applications:Mining, quarrying tough ores.
3. Mobile Jaw Crusher
- Diagram Feature:Integrated conveyor and screening system.
- Advantages:Portability for on-site crushing.
Common Jaw Crusher Diagrams for Troubleshooting
Diagram 1:Overload Protection Mechanism
- Shows how the toggle plate fractures under excessive load, preventing damage to the main components.
Diagram 2:Wear Parts Replacement
- Highlights replaceable components like jaw plates, wedges, and bearings.
Applications Supported by Jaw Crusher Diagrams
- Mining:Crushing gold, copper, and iron ores.
- Recycling:Reducing concrete and asphalt rubble.
- Aggregate Production:Generating 20–100 mm gravel for construction.
Benefits of Understanding Jaw Crusher Diagrams
- Improved Maintenance:Identify wear-prone parts (e.g., jaw plates) and schedule replacements.
- Optimized Performance:Adjust discharge settings for desired output size.
- Cost Savings:Avoid downtime with proactive troubleshooting.
Case Study: Boosting Efficiency in an Arizona Limestone Quarry with Liming Heavy Industry
A limestone quarry in Arizona upgraded its crushing operations by installing a Liming C6X125 Jaw Crusher to replace outdated equipment. By leveraging Liming’s advanced engineering and optimization tools, the quarry achieved remarkable results:
Key Results
- Output Increased by 30%
- Adjusted the hydraulic wedge adjustment system to optimize the discharge opening, achieving a crushing capacity of 500 TPH (up from 385 TPH).
- Implemented variable frequency drive (VFD) control to fine-tune motor speed for different limestone hardness levels.
- Wear Life Extended by 40%
- Switched to Liming’s Mn18Cr2 alloy jaw plates with ceramic inserts, doubling service intervals from 1,200 to 2,000 hours.
- Reduced replacement costs by $18,000 annually.
- Energy Savings of 15%
- The C6X125’s energy-efficient design and optimized kinematics lowered power consumption to 28 kWh/ton, compared to 33 kWh/ton previously.
Technical Upgrades
- Intelligent Control System: Real-time monitoring via Liming’s IoT platform enabled predictive maintenance, cutting unplanned downtime by 60%.
- Modular Structure: Quick replacement of wear parts reduced maintenance time from 8 hours to 2.5 hours per service.
Project Overview
Parameter | Before Liming C6X125 | After Liming C6X125 |
---|---|---|
Throughput | 385 TPH | 500 TPH |
Jaw Plate Lifespan | 1,200 hours | 2,000 hours |
Energy Cost | $0.12/ton | $0.10/ton |
Annual Savings | — | $220,000 |
Why Liming’s C6X Jaw Crusher?
- Hydraulic Adjustment: Enables quick changes to discharge settings for precise product sizing (50–200 mm).
- Robust Frame: Welded steel construction withstands high-impact loads in abrasive limestone environments.
- Eco-Friendly Operation: Low noise (<75 dB) and dust suppression compatibility meet EPA standards.
FAQs About Jaw Crusher Diagrams
Q:How do I adjust the discharge opening?
A:Use the adjusting wedge (see Diagram 1) to increase or decrease the gap.
Q:What causes uneven jaw plate wear?
A:Misaligned feed distribution or uneven material hardness.
Q:Where can I find OEM jaw crusher diagrams?
A:Check the manufacturer’s manual or websites like Metso or Sandvik.
Conclusion
A jaw crusher diagram is a vital tool for operators and engineers to maximize efficiency, reduce downtime, and ensure safe operations. By studying these diagrams, you can better understand component interactions and implement data-driven optimizations.