Rock Crushing Equipment For Recycling
Recycling has become a cornerstone of modern waste management and resource recovery. In industries such as construction, mining, and demolition, recycling equipment plays a vital role in reducing waste, conserving natural resources, and minimizing environmental impact. One of the most important technologies in recycling is rock crushing equipment, which is used to break down materials like concrete, asphalt, and other construction debris into reusable aggregates.
This article explores the different types of rock crushing equipment used in recycling, their functionality, and the advantages they offer to both the environment and the economy.
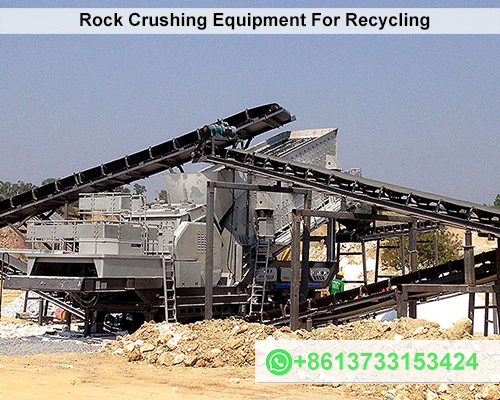
What is Rock Crushing Equipment for Recycling?
Rock crushing equipment is designed to reduce the size of larger materials, such as rocks, concrete, and asphalt, into smaller, more manageable pieces. This process enables the recovery of valuable resources from construction and demolition debris that would otherwise end up in landfills. By turning waste materials into usable aggregates, crushing equipment not only contributes to recycling but also supports the creation of high-quality construction materials like road base, gravel, and recycled concrete aggregates.
Types of Rock Crushing Equipment for Recycling
- Jaw crusher are one of the most common types of rock crushing equipment used in recycling. These machines consist of two crushing plates—one fixed and one movable—that apply compressive force to the material. As the material enters the crusher, the movable jaw plate moves toward the fixed plate, crushing the material into smaller pieces.
- Advantages:
- Ideal for large, bulky materials like concrete and asphalt.
- Simple design and easy to operate.
- Low maintenance compared to other crushing equipment.
- Applications: Concrete recycling, demolition debris, asphalt recycling, and hard rock crushing.
- Advantages:
- Impact crusher, also known as horizontal shaft impact crusher (HSI) or vertical shaft impact crusher (VSI), use high-speed impact force to break down materials. These crusher work by throwing the material against a surface at high velocity, causing the material to break into smaller pieces.
- Advantages:
- Highly effective for breaking down softer materials like concrete, asphalt, and rocks.
- Produce cubical-shaped aggregates, which are ideal for certain construction applications.
- Can handle a wide range of materials, including recycled concrete, asphalt, and natural stone.
- Applications: Concrete and asphalt recycling, manufacturing of sand and gravel aggregates, and production of high-quality aggregate for road construction.
- Advantages:
- Cone crusher operate using a similar principle to jaw crusher but are more effective for secondary and tertiary crushing stages. They consist of a conical head that crushes material against a stationary bowl. Cone crusher is particularly effective at reducing the size of material and producing finer, more uniform aggregates.
- Advantages:
- High capacity and excellent for fine crushing.
- Efficient for harder materials like granite and basalt.
- Can produce a more uniform product compared to jaw crusher.
- Applications: Asphalt recycling, concrete recycling, aggregate production, and hard rock processing.
- Advantages:
- Hammermills, or hammer crusher, are another popular type of crushing equipment used in recycling. These machines use rotating hammers or blades to break the material into smaller pieces. The material is crushed when it is repeatedly hit by the rotating hammers.
- Advantages:
- Versatile and capable of handling various types of materials, including concrete and asphalt.
- Produces a fine product that is suitable for use in various construction applications.
- Relatively simple design, making maintenance easy.
- Applications: Recycling concrete, asphalt, demolition debris, and for producing sand and fine aggregates.
- Advantages:
- Mobile rock crusher are a game-changer in the recycling industry. These crusher is mounted on tracks or wheels, allowing them to be easily transported to different job sites. Mobile crusher can be equipped with jaw, impact, or cone crusher, providing flexibility for various recycling applications.
- Advantages:
- High mobility, enabling work directly at the recycling site, which reduces transportation costs.
- Flexible and can be adapted for various types of recycling projects.
- Saves time and operational costs by avoiding the need to transport large amounts of waste material.
- Applications: On-site concrete and asphalt recycling, demolition sites, construction sites, and mining operations.
- Advantages:
The Recycling Process Using Rock Crushing Equipment
The process of recycling with rock crushing equipment typically follows several key steps:
- Material Collection: Construction and demolition debris, such as concrete, asphalt, and other waste materials, are collected. These materials are often stockpiled at a central location.
- Pre-Sorting and Screening: Before the materials are fed into a crusher, they may be pre-sorted to remove contaminants, such as metals, plastics, and wood. Screening is also done to separate materials by size.
- Crushing: The sorted and screened material is fed into the rock crusher, where it is broken down into smaller pieces. Depending on the equipment used, the material may be reduced to various sizes, from coarse aggregates to fine particles.
- Post-Crushing Screening: After crushing, the material is often screened again to ensure it meets the desired size and quality specifications. Some materials may need to be further processed, depending on the intended use.
- Final Product: The final product is recycled aggregate, which can be used in various construction applications, such as road base, backfill, and in the production of new concrete.
Benefits of Rock Crushing Equipment for Recycling
- Environmental Sustainability:
- Reduces the need for extracting raw materials, which helps conserve natural resources like sand, gravel, and stone.
- Decreases the amount of waste sent to landfills, promoting circular economy principles.
- Minimizes the environmental impact of transportation, as materials can be processed directly on-site, reducing the need for long-distance hauling.
- Cost-Effectiveness:
- Recycling materials on-site eliminates the need for costly transportation to landfills or recycling centers.
- Reduces the need to purchase new construction materials, which can be expensive.
- The equipment is designed for durability and low maintenance, offering long-term cost savings.
- High-Quality Aggregates:
- Recycled aggregates are often of high quality and can be used in many construction applications, such as road base, foundation material, and even in the production of new concrete.
- Recycled concrete and asphalt are often used in highway construction, providing durable, cost-effective materials.
- Energy Efficiency:
- Recycling construction materials with crushing equipment requires less energy than producing new aggregates from raw materials, contributing to lower carbon emissions and energy consumption.
- Flexibility and Mobility:
- Mobile rock crusher provide the flexibility to process material directly on-site, which can significantly reduce operational costs related to transportation and handling.
Conclusion
Rock crushing equipment is an essential part of the recycling process, enabling the transformation of waste materials into valuable, reusable aggregates. The variety of crusher available—such as jaw crusher, impact crusher, cone crusher, and mobile rock crusher—ensures that recycling companies can efficiently handle different types of materials. By investing in rock crushing equipment, businesses can contribute to a more sustainable future, reduce waste, and benefit from cost-effective and high-quality recycled materials for construction projects. As the demand for sustainable practices continues to grow, rock crushing equipment for recycling will remain a critical component in the circular economy.