Sandstone Crushing Production Line Design Project
1. Introduction
Sandstone is a sedimentary rock composed of sand grains cemented together. It is a common building material and is also used in the production of glass, ceramics, and abrasives. Sandstone crushing production lines is used to process sandstone into different sizes for various applications.
The design of a sandstone crushing production line depends on a number of factors, including the size and type of sandstone being processed, the desired product size, the production capacity, and the environmental regulations.
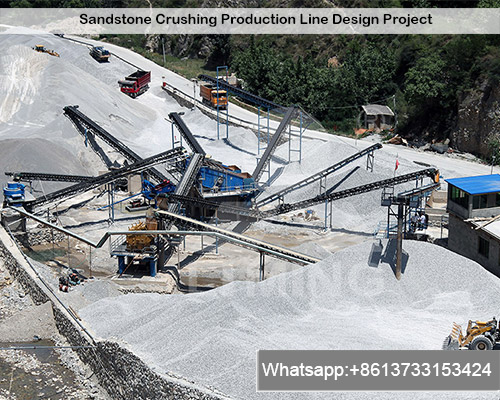
2. Common Equipment in a Sandstone Crushing Production Line
A typical sandstone crushing production line consists of the following equipment:
- Vibrating feeder: The vibrating feeder evenly feeds the sandstone into the primary crusher.
- Primary crusher: The primary crusher reduces the sandstone to a smaller size. This is typically done using a jaw crusher or a cone crusher.
- Secondary crusher: The secondary crusher further reduces the sandstone to the desired product size. This is typically done using a cone crusher or an impact crusher.
- Vibrating screen: The vibrating screen separates the sandstone into different sizes.
- Conveyor belts: Conveyor belts transport the sandstone between the different pieces of equipment.
- Dust collection system: The dust collection system collects and removes dust from the production line.
3. Design Considerations
- Production capacity: The production capacity of the sandstone crushing production line is the amount of sandstone that can be processed per hour. The production capacity is determined by the size and capacity of the equipment.
- Product size: The product size of the sandstone crushing production line is the size of the sandstone particles that is produced. The product size is determined by the settings of the crushing and screening equipment.
- Environmental regulations: The design of the sandstone crushing production line must comply with all applicable environmental regulations. This includes regulations on dust emissions, noise emissions, and water usage.
4. Benefits of a Sandstone Crushing Production Line
- Increased efficiency: Sandstone crushing production lines can significantly increase the efficiency of sandstone processing. This is because they can process large amounts of sandstone quickly and efficiently.
- Improved product quality: Sandstone crushing production lines can produce high-quality sandstone products. This is because they can control the size and shape of the sandstone particles.
- Reduced costs: Sandstone crushing production lines can reduce the costs of sandstone processing. This is because they can reduce the amount of labor and energy required.
5. Applications
Sandstone crushing production lines is used in a variety of applications, including:
- Construction: Sandstone is a common building material and is used in the construction of roads, bridges, and buildings.
- Glass production: Sandstone is used in the production of glass.
- Ceramics production: Sandstone is used in the production of ceramics.
- Abrasives production: Sandstone is used in the production of abrasives.
6. Conclusion
Sandstone crushing production lines is an essential part of the sandstone industry. They is used to process sandstone into different sizes for various applications. Sandstone crushing production lines can increase efficiency, improve product quality, and reduce costs.
Additional Considerations
- The type of sandstone being processed: The type of sandstone being processed will affect the choice of equipment and the design of the production line. For example, harder sandstones will require more powerful crushing equipment.
- The moisture content of the sandstone: The moisture content of the sandstone will also affect the choice of equipment and the design of the production line. For example, wet sandstone will require equipment that can handle wet material.
- The availability of power and water: The availability of power and water will also affect the design of the production line. For example, if power is limited, then the production line may need to be designed to use less energy-intensive equipment.