Vertical Roller Mill Grinding Process
The vertical roller mill is a type of grinding machine used to grind materials into extremely fine powder for use in mineral dressing processes, paints, pyrotechnics, cements, and ceramics. It is an energy-efficient alternative for a ball mill or a horizontal roller mill.
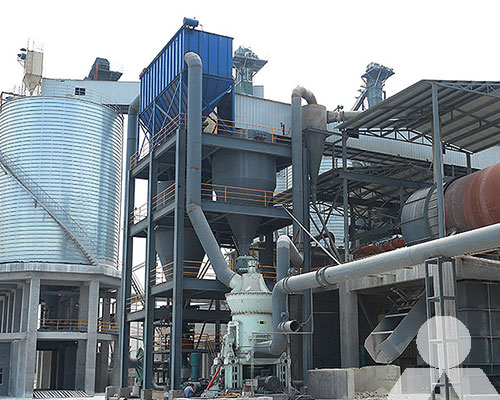
The grinding process in a vertical roller mill involves feeding the material into the mill inlet, where it is grinded between a roller and a table. The material is initially crushed by the pressure exerted by the roller, and then ground further by the grinding table. The grinding action is a combination of compression and shearing forces generated by the rotating rollers and the stationary table.
Here is a step-by-step overview of the grinding process in a vertical roller mill:
- 1.Material feed: The raw material, such as limestone or clinker, is fed into the mill through the inlet chute at the top of the mill. The material falls onto the grinding table and is dispersed under the grinding rollers.
- 2.Grinding: As the grinding table rotates, the material is crushed by the pressure and grinding action of the rollers. The grinding rollers exert both compressive and shearing forces on the material, reducing it to smaller particles. The ground material is then swept upwards by the air flow and carried to the classifier.
- 3.Classification: The fine particles separated by the classifier are carried out of the mill with the air flow and collected in a cyclone or bag filter for further processing or storage. The coarse particles, on the other hand, fall back onto the grinding table for further grinding.
- 4.Drying: Depending on the moisture content of the raw material, some vertical roller mills also incorporate a drying function. Hot gas from a furnace or waste heat source is introduced into the mill to evaporate any moisture present in the material, ensuring efficient grinding and preventing material sticking on the grinding surfaces.
- 5.Grinding efficiency: The design of the vertical roller mill allows for efficient grinding with a lower power consumption compared to traditional ball mills or horizontal roller mills. The grinding pressure, grinding track, and grinding table are optimized to achieve high grinding efficiency and a narrow particle size distribution.
- 6.Control systems: Modern vertical roller mills are equipped with advanced control systems to monitor and regulate the grinding process. These systems can automatically adjust the mill parameters such as grinding pressure, grinding table speed, and classifier settings to optimize the performance of the mill and maintain stable operation.
Overall, the vertical roller mill grinding process offers advantages such as high grinding efficiency, low power consumption, and the ability to grind a wide range of materials. It has become increasingly popular in the cement industry and other sectors where fine grinding is required.