What is the steps in the Calcium Carbonate Manufacturing Process and Equipment?
Calcium carbonate is a white, odorless, and tasteless powder that is the most abundant naturally occurring inorganic compound. It is found in a variety of rocks and minerals, including limestone, chalk, and marble. Calcium carbonate is used in a wide variety of applications, including papermaking, plastics, paints, and food.
There are two main types of calcium carbonate: natural and synthetic. Natural calcium carbonate is mined from the earth, while synthetic calcium carbonate is produced from limestone or other calcium-rich materials.
The manufacturing process for calcium carbonate varies depending on the type of calcium carbonate being produced. For natural calcium carbonate, the process typically involves crushing the ore, followed by screening and grinding. The ground ore is then washed to remove impurities.
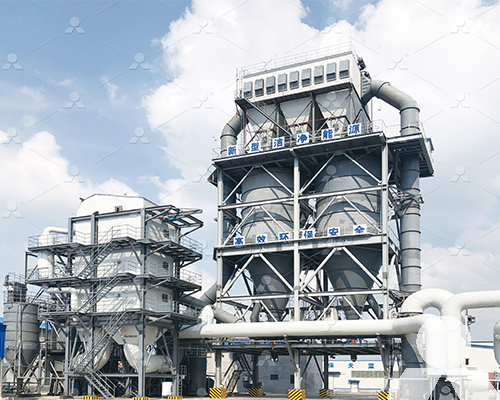
For synthetic calcium carbonate, the process typically involves calcining limestone or other calcium-rich materials. Calcination is a process of heating the material to a high temperature, which converts the calcium carbonate into calcium oxide. The calcium oxide is then dissolved in water to form a solution of calcium hydroxide. The calcium hydroxide solution is then carbonated with carbon dioxide, which converts it back into calcium carbonate.
The following are the steps involved in the manufacturing process for calcium carbonate:
1. Raw material preparation
The first step in the manufacturing process is to prepare the raw materials. For natural calcium carbonate, this typically involves crushing the ore, followed by screening and grinding. The ground ore is then washed to remove impurities.
For synthetic calcium carbonate, the first step is to calcine the limestone or other calcium-rich materials. Calcination is a process of heating the material to a high temperature, which converts the calcium carbonate into calcium oxide.
2. Calculation
In the case of synthetic calcium carbonate, the next step is to dissolve the calcium oxide in water to form a solution of calcium hydroxide. This is done by adding the calcium oxide to water and stirring until it dissolves.
3. Carbonation
The final step is to carbonate the calcium hydroxide solution with carbon dioxide. This is done by bubbling carbon dioxide gas through the solution. The carbon dioxide reacts with the calcium hydroxide to form calcium carbonate.
Equipment
The equipment used in the manufacturing process for calcium carbonate varies depending on the type of calcium carbonate being produced. For natural calcium carbonate, the equipment typically includes crusher, screens, grinder mill, and washers.
For synthetic calcium carbonate, the equipment typically includes calciners, dissolvers, and carbonators.
Applications
Calcium carbonate is used in a wide variety of applications, including:
- Papermaking
- Plastics
- Paints
- Food
- Cosmetics
- Pharmaceuticals
- Construction
Calcium carbonate is a versatile material with a wide range of applications. It is an important industrial mineral that is used in a variety of products that we use every day.