Influence of crusher type in the shape of fine crushed aggregate grains
Quarries have invested in equipment to increase production and improve the quality of their products, such as vertical shaft impact crushers (VSI). This type of crusher works with autogenous comminution of the material to improve the shape of the coarse aggregates. However, there are few studies about the influence of crushers in the shape of fine aggregate grains. In this context, gneiss and granite fine crushed aggregates, produced in cone crushers and VSI were studied.
Parameters such as coefficient of volumetric shape, aspect ratio, and circularity were used to compare these aggregates with the river sand. The results showed that there is a difference between the shape of the sand river and the fine crushed aggregates. Among the crushed aggregates, those from the VSI showed improvements in grain shape, compared to aggregates from cone crushers. However, this improvement decreases with the reduction of grain size. For the study in the mortar, the crushed aggregates were sepa- rated in fractions by sieving and composed to obtain the same granulometric distribution for all the aggregates. The mortars made with the crushing aggregates from the VSI showed higher fluidity, lower air content and higher compressive strength when compared to the crushed aggregates pro- duced in the cone crusher.
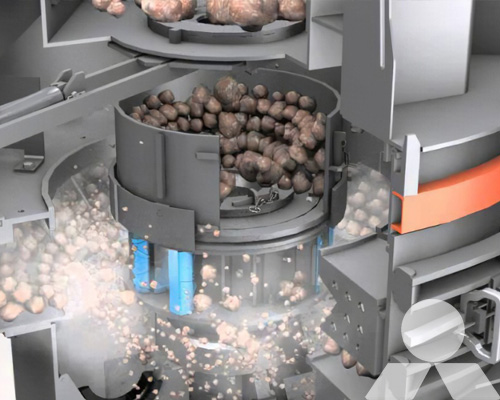
With the objective of improving this deficiency and increasing the consumer’s market, the companies that produce crushed aggre- gates (quarries) have invested in technology and new equipment. The main highlight has been the use of more modern and efficient crushers, trying to correct the shape of the grains, the granulomet- ric composition and even the quality of the fine aggregates. Within this context, there is the increasing use of the vertical shaft impact crushers (VSI). These crushers were developed at the end of the 1960’s in New Zealand, gaining space within the concrete in- dustry. The principle of comminution of the VSI type crushers is based on the acceleration of the particles through a central rotor that rotates in high velocity.
The grains enter the central part of the rotor and are thrown by the centrifugal force to the sides of the equipment, at velocities that may go up to 90 m/sec (approximately 320 km/hr), possibly colliding with the bed formed by the accumu- lated aggregates in the carcass of the crusher, or in the aggregates that fall in the form of a lateral cascade. The reduction of the particles occurs due to the collision of the rock against rock, generating a greater quantity of fine particles and an aggregate with a more cubic shape when compares to the aggregates ob- tained in the conic crushers. Normally the VSI crushers are em- ployed in quarries as tertiary crushers, for the exclusive production of crushed fine aggregate or for the reduction of the dimension of a material that eventually presents small commercial value.
Another kind of equipment commonly found in quarries as secondary and tertiary crushers is the conic crusher. It has an oscillating central piston, which, in circular movements, at one moment moves away and at another moves closer to the lateral carcass of the crusher. The actual crushing occurs by the compression of the rock between the coatings of the piston (mantle) and of the car- cass, or between the actually pressed particles. However, the fracture of the particles in this type of crushers obeys, in many cases, the preferential plans of the rocks, due to their mineralogi- cal constitutions, being able to generate aggregates with not so favorable shapes for the production of concretes. The technical scientific environment already knows of the benefits of the VSI crushers in the improvement of the shape of the grains of coarse crushed aggregates.