Crushing and Screening Equipment For Ore Crushing
In the mining and mineral processing industries, crushing and screening equipment plays a pivotal role in transforming raw ore into usable materials. Efficient ore crushing is essential for maximizing productivity, reducing operational costs, and meeting quality standards. This guide explores the types of crushing and screening equipment, their applications, and best practices to optimize your operations—perfect for mining professionals and industry newcomers alike.
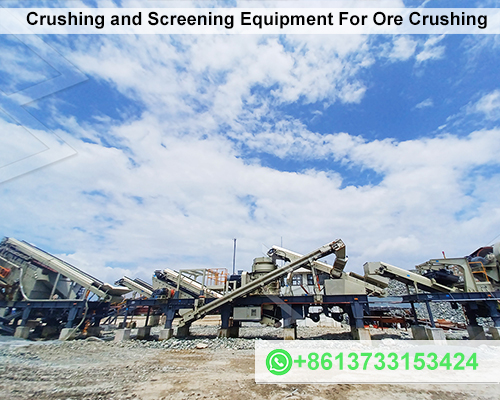
Why Crushing and Screening Equipment Matters for Ore Processing
Ore crushing and screening are the first steps in extracting valuable minerals from raw materials. The right equipment ensures:
- Higher Efficiency: Reducing oversized ore to manageable sizes for downstream processes.
- Cost Savings: Minimizing energy consumption and wear-and-tear on machinery.
- Quality Control: Producing uniformly sized particles for consistent processing results.
Without effective crushing and screening, bottlenecks can arise, leading to delays and increased operational expenses. Let’s dive into the key equipment used in this critical stage.
Types of Crushing Equipment for Ore Processing
- Jaw Crusher
- Function: Primary crushing of hard, abrasive ores like granite and basalt.
- Benefits: High throughput, simple maintenance, and durability.
- Applications: Ideal for initial size reduction in mining and quarrying.
- Cone Crusher
- Function: Secondary or tertiary crushing for finer particle sizes.
- Benefits: Precision crushing with adjustable settings.
- Applications: Used in aggregate production and metal ore processing.
- Impact Crusher
- Function: Versatile crushing via high-speed impact forces.
- Benefits: Excellent for softer ores and recycling applications.
- Applications: Limestone, coal, and recycled concrete processing.
- Gyratory Crusher
- Function: Heavy-duty primary crushing for large-scale operations.
- Benefits: High capacity and reliability.
- Applications: Major mining projects requiring continuous operation.
Essential Screening Equipment for Ore Classification
After crushing, screening equipment separates ore by size, ensuring only properly sized material moves to the next stage. Key types include:
- Vibrating Screens: Most common, using vibration to sort particles.
- Trommel Screens: Rotating drums for wet or sticky ores.
- High-Frequency Screens: Precision separation of fine materials.
Pro Tip: Pair crusher and screens in a closed-circuit system to recirculate oversized material for re-crushing, boosting efficiency.
How to Choose the Right Crushing and Screening Equipment
Selecting the best equipment depends on:
- Ore Characteristics: Hardness, abrasiveness, moisture content, and size.
- Production Goals: Required throughput and final product specifications.
- Site Conditions: Space limitations, power availability, and environmental regulations.
For example, a jaw crusher paired with a vibrating screen suits high-volume primary crushing, while cone crusher and high-frequency screens excel in precision secondary stages.
Top 3 Benefits of Modern Crushing and Screening Systems
- Automation Integration: Advanced systems offer real-time monitoring and adjustments, reducing downtime.
- Energy Efficiency: Newer models consume less power while maintaining high output.
- Modular Designs: Portable or modular setups enable flexible deployment across sites.
Maintenance Tips for Longevity
- Regularly inspect wear parts like crusher liners and screen meshes.
- Lubricate moving components to prevent overheating.
- Use OEM (Original Equipment Manufacturer) parts for compatibility.
Future Trends in Ore Crushing Technology
The industry is shifting toward:
- Smart Crusher: IoT-enabled equipment for predictive maintenance.
- Sustainable Practices: Equipment designed to reduce carbon footprint.
- Hybrid Power Systems: Combining electric and diesel for remote operations.
Conclusion
Investing in the right crushing and screening equipment is critical for optimizing ore processing efficiency, reducing costs, and achieving consistent product quality. By understanding the types of machinery available, their applications, and maintenance needs, mining operations can stay competitive in a demanding industry.
For more insights on mining equipment and best practices, explore our blog or contact our experts today!