Mobile Screening Plants & Ore Crusher
Introduction
In today’s fast-paced mining and quarrying industries, efficiency and adaptability are paramount. Mobile screening plants and ore crushers have emerged as game-changers, enabling operators to process materials directly at extraction sites. Combining crushing and screening in a single mobile unit, these systems reduce costs, enhance productivity, and minimize environmental impact. In this guide, Liming Heavy Industry explores how our advanced mobile screening plants and crushers transform ore processing, their key benefits, and how to select the ideal setup for your operations.
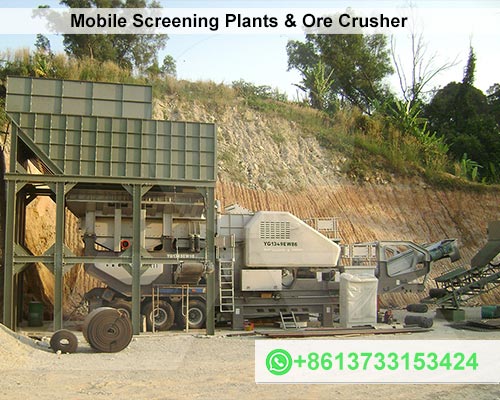
What Are Mobile Screening Plants & Ore Crusher?
Mobile screening plants and ore crushers is integrated systems designed to crush raw materials (e.g., iron ore, gold, limestone) and screen them into precise grades on-site. Unlike fixed plants, these mobile units can be transported between locations, making them ideal for remote mines, temporary projects, or sites with limited infrastructure.
Key Components:
- Mobile Crusher: Breaks down large rocks into smaller fragments (e.g., jaw, cone, or impact crushers).
- Mobile Screen: Separates crushed material into defined sizes (e.g., 0–10mm, 10–30mm).
- Conveyor System: Transfers material between crushers, screens, and stockpiles.
Why Choose Liming’s Mobile Screening & Crushing Plants?
- Cost Efficiency:
- Eliminates hauling costs by processing materials on-site.
- Reduces labor and infrastructure expenses (no permanent setup required).
- Enhanced Flexibility:
- Deploy units to multiple sites or adjust layouts for changing project needs.
- Faster Project Timelines:
- Set up and begin processing within hours, not weeks.
- Environmental Compliance:
- Advanced dust suppression and noise reduction systems meet global standards (e.g., EPA, EU directives).
Liming Heavy Industry’s Mobile Solutions
As a leader in crushing and screening technology, Liming Heavy Industry offers tailored mobile systems for diverse ore types:
1. NK Series Mobile Crushing & Screening Plants
- Models: NK200 (200–350 TPH), NK300 (400–600 TPH), NK500 (800–1,000 TPH).
- Features:
- Integrated jaw crusher (C6X Series), cone crusher (HPT Series), and multi-layer vibrating screens.
- Hybrid power options for fuel savings in off-grid areas.
- Ideal For: Large-scale iron ore, copper, or gold mining.
2. VU Series Mobile Screening Plants
- Screen Layers: 2–4 layers with customizable mesh sizes (5mm–100mm).
- Applications:
- Pre-screening before primary crushing.
- Final grading of aggregates for construction.
3. C6X Jaw Crusher + 3YKN Series Screen Combo
- Feed Size: Up to 1,500mm (C6X).
- Output: Adjustable from 0–50mm via screen configuration.
- Use Case: High-capacity processing of abrasive ores like magnetite.
Case Study: Liming NK300 Plant Boosts Efficiency in Australian Iron Ore Mine
Client: A Tier-1 iron ore producer in Pilbara, Australia.
Challenge:
- Process 600 TPH of hematite ore (feed size: 0–1,000mm) into 0–30mm pellets.
- Frequent site relocations due to shifting mining fronts.
Solution:
- Equipment: Liming NK300 Mobile Plant with:
- C6X160 Jaw Crusher (Primary crushing to 150–250mm).
- HPT300 Cone Crusher (Secondary crushing to 30–50mm).
- 3YKN3075 Screen (3-layer screening for 0–10mm, 10–20mm, 20–30mm).
Results:
- Output Precision: 98% of material within 0–30mm range.
- Mobility: Relocated 3 times in 6 months with <8-hour downtime per move.
- Cost Savings: Reduced fuel consumption by 25% using hybrid power mode.
How to Choose the Right Mobile Screening & Crushing System
- Material Type:
- Hard ores (e.g., granite): Prioritize jaw crushers (C6X) + impact-resistant screens.
- Sticky or wet ores: Opt for anti-clogging screens (VU Series).
- Capacity Needs:
- Match plant size (NK200/NK300/NK500) to hourly tonnage targets.
- Mobility Requirements:
- Tracked units for rough terrain vs. wheeled units for paved sites.
- After-Sales Support:
- Choose brands like Liming Heavy Industry with global service networks.
Maintenance Tips for Peak Performance
- Daily Inspections:
- Check screen mesh for tears and crusher liners for wear.
- Lubrication:
- Use high-temperature grease for crusher bearings in dusty environments.
- Software Updates:
- Enable IoT features for real-time diagnostics (e.g., Liming’s Smart Mining Platform).
FAQs About Mobile Screening & Crushing Plants
Q: Can mobile plants handle both crushing and screening?
A: Yes! Systems like Liming’s NK Series integrate crushers, screens, and conveyors in one unit.
Q: What’s the lifespan of screen mesh in abrasive ores?
A: Liming’s polyurethane screens last 6–12 months in iron ore applications, depending on usage.
Q: Are mobile plants suitable for underground mining?
A: Compact models (e.g., NK200) can be adapted for narrow tunnels with low-profile designs.
Conclusion
Mobile screening plants and ore crushers is indispensable for modern mining and quarrying. By investing in Liming Heavy Industry’s innovative NK Series or VU Series systems, operators gain unmatched flexibility, precision, and cost efficiency. Whether processing iron ore, gold, or aggregates, our solutions ensure you stay ahead in a competitive market.