Calcite Crushing and Grinding Process
Calcite crushing and grinding powder production process is an industrial production technology that processes calcite raw materials into fine powder through crushing, grinding, screening, and packaging to meet the needs of different industries such as construction, chemical, and pharmaceuticals. This article introduces the process, equipment, and optimization measures of calcite crushing and grinding powder production.
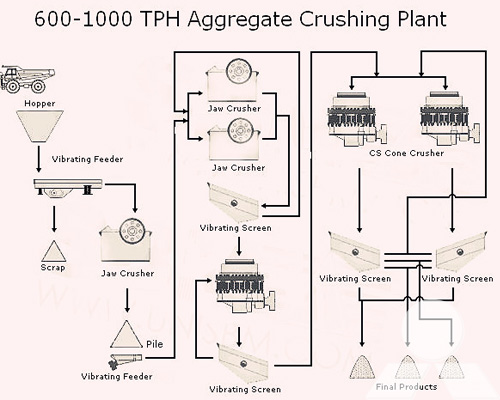
I. Calcite Crushing and Grinding Powder Production Process
The process of calcite crushing and grinding powder production includes crushing, grinding, screening, and packaging.
- Crushing: The raw calcite blocks are crushed by primary crushing equipment (such as jaw crusher) into small pieces.
- Grinding: The crushed calcite materials are sent to grinding equipment (such as ball mill, roller mill) for fine grinding to achieve the desired particle size and fineness.
- Screening: The ground calcite powder is screened through screening equipment (such as vibrating screen, rotary screen) to separate different sizes of fine powder.
- Packaging: The screened calcite powder is packaged through packaging equipment (such as automatic packaging machine) for storage and transportation.
II. Calcite Crushing and Grinding Powder Production Equipment
Calcite crushing and grinding powder production process requires multiple equipment, including crushing equipment, grinding equipment, screening equipment, and packaging equipment. Commonly used equipment includes:
- Jaw crusher: used for primary crushing to crush the calcite raw materials into small pieces.
- Impact crusher: used for intermediate crushing to further crush the calcite materials into smaller pieces.
- Ball mill: used for fine grinding to achieve the desired particle size and fineness of the calcite powder.
- Vibrating screen: used for screening the ground calcite powder to separate different sizes of fine powder.
- Automatic packaging machine: used for packaging the screened calcite powder for storage and transportation.
III. Optimization Measures for Calcite Crushing and Grinding Powder Production
To improve the efficiency and quality of calcite crushing and grinding powder production, the following optimization measures can be taken:
- Optimize equipment configuration: Select suitable crushing, grinding, screening, and packaging equipment according to production needs and raw material characteristics to improve production efficiency and product quality.
- Control crushing and grinding time: Control the crushing and grinding time to avoid excessive crushing and grinding, which can affect product quality and production efficiency.
- Strengthen equipment maintenance: Regularly maintain and repair equipment to ensure normal operation and service life, and reduce downtime due to failures.
- Optimize production process: Optimize the production process, reduce production steps and time, and improve production efficiency and product quality.
In conclusion, calcite crushing and grinding powder production process is a complex process that requires reasonable equipment configuration, time control, maintenance, and process optimization to improve production efficiency and product quality and meet the needs of different industries.