Bituminous Coal Crushing Process Plant and Machinery
Introduction to Bituminous Coal Crushing
Bituminous coal, a vital energy resource for power generation and industrial applications, requires efficient crushing to meet size specifications for combustion, gasification, or coking. A well-designed bituminous coal crushing process plant ensures consistent particle size, reduces transportation costs, and enhances combustion efficiency. This article explores the machinery, workflows, and innovations that drive modern coal processing operations.
Key Stages in the Bituminous Coal Crushing Process
1. Primary Crushing
- Jaw Crusher:Reduce large coal lumps (≤1,500 mm) to manageable sizes (150–300 mm).
- Model Example:Liming C6X Jaw Crusher with hydraulic adjustment for precise output control.
- Rotary Breakers:Remove impurities (rock, shale) while crushing coal.
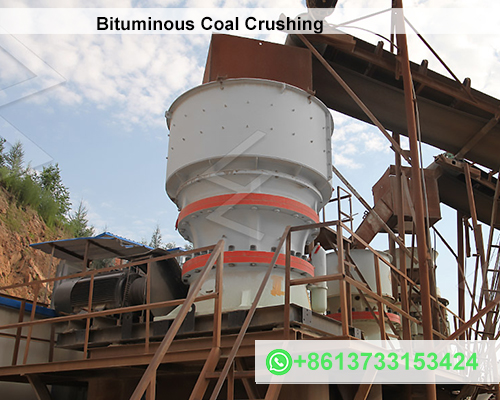
2. Secondary Crushing
- Impact Crusher:Produce uniform particles (20–50 mm) for improved combustion.
- Model Example:Liming CI5X Impact Crusher with high-speed rotor and anti-wear alloys.
- Roll Crusher:Generate finer grains (5–20 mm) for specialized applications like pulverized coal injection (PCI).
3. Screening and Classification
- Vibrating Screens:Separate coal into fractions (e.g., 0–5 mm, 5–20 mm).
- Air Classifiers:Remove fine dust and ash to meet environmental standards.
4. Material Handling
- Conveyors:Transport crushed coal to storage or processing units.
- Dust Suppression Systems:Minimize airborne particles using water sprays or bag filters.
Essential Machinery for Bituminous Coal Crushing
Equipment | Function | Key Features |
---|---|---|
Jaw Crusher | Primary size reduction | High torque, Mn18Cr2 jaw plates |
Impact Crusher | Secondary crushing & shaping | Adjustable grate, low maintenance |
Rotary Screen | Size classification | Multi-layer decks, self-cleaning design |
Belt Conveyor | Material transport | Fire-resistant belts, IoT-enabled monitoring |
Design Considerations for Coal Crushing Plants
- Coal Properties
- Moisture Content:High moisture may require pre-drying to prevent clogging.
- Hardness:Bituminous coal typically has a Mohs hardness of 2–3.
- Capacity Requirements
- Small plants:50–200 TPH (e.g., mining operations).
- Large plants:500–2,000 TPH (e.g., thermal power stations).
- Environmental Compliance
- Dust control systems to meet OSHA and EPA regulations.
- Noise reduction enclosures for urban installations.
- Energy Efficiency
- Hybrid crusher (diesel-electric) reduce fuel consumption by 20–30%.
Advantages of Modern Coal Crushing Plants
- Higher Throughput:Automated systems achieve 10–25% greater output vs. manual operations.
- Extended Equipment Life:Wear-resistant components (e.g., ceramic-lined impact plates) last 2–3x longer.
- Cost Savings:On-site crushing reduces transportation and handling expenses.
- Sustainability:Closed-loop water recycling and emission controls align with green energy goals.
Case Study:Optimizing a Coal Plant in Poland
A Polish energy company upgraded its facility with a Liming Mobile Crushing Plant (K3S216) to process bituminous coal. Results:
- 40% Higher Efficiency:Crushing capacity increased from 300 TPH to 420 TPH.
- 30% Lower Maintenance Costs:Ceramic-reinforced wear parts reduced replacements.
- Zero Emissions Fines:Integrated dust suppression ensured compliance with EU standards.
FAQs About Bituminous Coal Crushing
Q:What crusher is best for high-moisture coal?
A: Rotary breakers or impact crusher with anti-clogging designs.
Q:How to prevent dust explosions in coal plants?
A: Use inert gas systems, regular equipment cleaning, and spark detection.
Q:Can crushed coal be used for coke production?
A: Yes, but precise sizing (3–30 mm) is critical for coking efficiency.
Conclusion
A bituminous coal crushing process plant equipped with advanced machinery like Liming’s C6X jaw crusher and CI5X impact crusher ensures reliable, efficient, and eco-friendly operations. By optimizing crushing workflows and adopting durable technologies, industries can maximize energy output while minimizing environmental impact.