Dolomite Crushing and Grinding Process
Dolomite is a common mineral with calcium carbonate as its main component. In industrial production, dolomite is often used as building materials, chemical raw materials, pharmaceutical raw materials, etc. Among them, the production process of dolomite crushing and grinding powder is an important application. This article will introduce the process, equipment, and precautions of the production process of dolomite crushing and grinding powder.
I. Production process
The main process of the production process of dolomite crushing and grinding powder includes four steps: crushing, grinding, screening, and packaging.
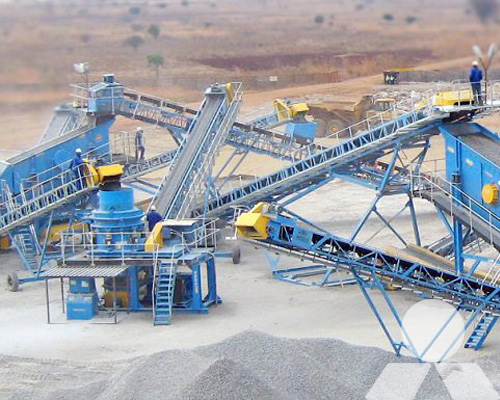
- Crushing
First, crush the raw dolomite blocks. Crushing equipment can choose jaw crusher, cone crusher, etc. The size of the crushed dolomite blocks should be controlled within a suitable range for subsequent grinding process. - Grinding
Send the crushed dolomite blocks to the grinding equipment for grinding. Grinding equipment can choose ball mill, roller mill, etc. During the grinding process, it is necessary to control the grinding time and particle size to ensure the quality of the ground dolomite powder. - Screening
The ground dolomite powder needs to be screened to remove impurities and control particle size. Screening equipment can choose vibrating screen, rotary screen, etc. The screened dolomite powder should meet the production requirements for particle size and quality. - Packaging
Finally, package the screened dolomite powder. Packaging equipment can choose automatic packaging machine, manual packaging machine, etc. When packaging, attention should be paid to the quality and sealing of the packaging materials to ensure the quality and safety of the product.
II. Equipment selection
The production process of dolomite crushing and grinding powder requires the use of various equipment, including crushing equipment, grinding equipment, screening equipment, and packaging equipment. Equipment selection should be comprehensively considered based on production scale, product quality requirements, and economic benefits.
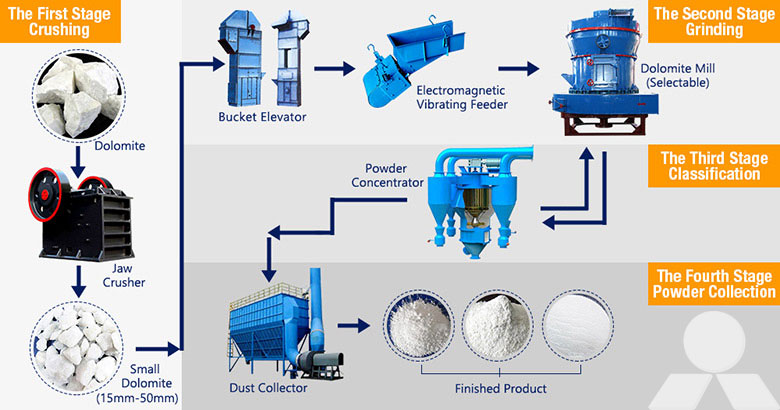
- Crushing equipment
Crushing equipment can choose jaw crusher, cone crusher, etc. Jaw crusher is suitable for crushing ores with high hardness and high crushing efficiency; cone crusher is suitable for crushing ores with medium hardness and uniform crushing particle size. - Grinding equipment
Grinding equipment can choose ball mill, roller mill, etc. Ball mill is suitable for products with low requirements for grinding fineness and high grinding efficiency; roller mill is suitable for products with high requirements for grinding fineness and uniform grinding particle size. - Screening equipment
Screening equipment can choose vibrating screen, rotary screen, etc. Vibrating screen is suitable for products with fine particle size and high screening efficiency; rotary screen is suitable for products with coarse particle size and high screening accuracy. - Packaging equipment
Packaging equipment can choose automatic packaging machine, manual packaging machine, etc. Automatic packaging machine is suitable for enterprises with large production scale and high packaging efficiency; manual packaging machine is suitable for enterprises with small production scale and low packaging cost.
III. Precautions
In the production process of dolomite crushing and grinding powder, attention should be paid to the following points:
- Selection and quality requirements of raw materials. Choose high-quality dolomite raw materials with less impurities to ensure product quality.
- Maintenance and maintenance of equipment. Regularly inspect and maintain equipment to ensure normal operation and service life of equipment.
- Sanitation and safety of production environment. Maintain the sanitation and safety of the production environment to prevent pollution and accidents.
- Quality inspection and control of products. Conduct quality inspection and control of the produced dolomite powder to ensure product quality and safety.
The production process of dolomite crushing and grinding powder is an important industrial production technology. In the production process, attention should be paid to the selection and quality requirements of raw materials, equipment selection and maintenance, sanitation and safety of the production environment, and quality inspection and control of products to ensure product quality and safety.