Grinding mill for gypsum building powder production line
Grinding mill is a crucial component in the gypsum building powder production line, responsible for pulverizing gypsum rock into a fine, consistent powder. The selection of an appropriate grinding mill is essential for achieving the desired powder fineness and ensuring the quality of the final gypsum building powder product.
Key Considerations for Grinding Mill Selection
Gypsum Rock Characteristics: The hardness, size, and moisture content of the gypsum rock significantly impact the grinding process and the required mill specifications.
Desired Powder Fineness: The fineness of the gypsum powder directly influences the performance of the final building material. Finer powder generally leads to smoother finishes and better bonding properties.
Production Capacity: The grinding mill’s capacity should align with the overall production requirements of the gypsum building powder production line.
Energy Efficiency: Grinding mills consume a significant amount of energy; selecting an energy-efficient mill can reduce operating costs and minimize environmental impact.
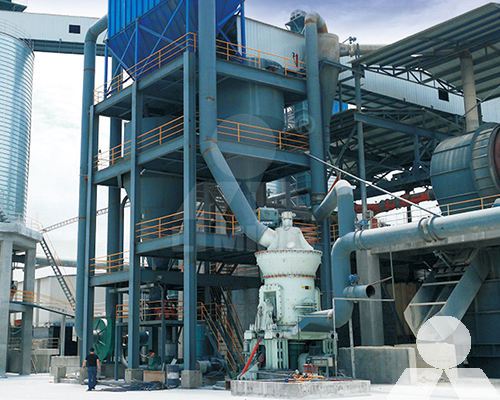
Common Types of Grinding Mills for Gypsum Powder Production
- Vertical Roller Mill: Vertical roller mill are widely used for grinding gypsum due to their high efficiency and ability to produce fine powder. They consist of vertical rollers that rotate against a stationary grinding plate, effectively pulverizing the gypsum rock.
- Ball Mill: Ball mill are versatile grinding mills suitable for various materials, including gypsum. They contain rotating drums filled with steel balls that crush the gypsum rock as the drum rotates.
- Raymond Mill: Raymond mill are high-speed grinding mills that utilize centrifugal force to pulverize gypsum rock. They are known for their ability to achieve exceptionally fine powder.
Factors Affecting Grinding Mill Performance
- Grinding Media: The type, size, and shape of the grinding media significantly impact the powder fineness and the mill’s efficiency.
- Rotational Speed: The rotational speed of the grinding mill’s rotor or rollers directly affects the grinding intensity and the powder fineness.
- Mill Feed Rate: The rate at which gypsum rock is fed into the mill influences the grinding process and the powder quality.
- Mill Fill Level: Maintaining an optimal mill fill level ensures efficient grinding and minimizes wear on the grinding media.
Maintenance and Troubleshooting for Grinding Mills
Regular maintenance of grinding mills is crucial for ensuring optimal performance and preventing costly breakdowns. Regularly inspecting grinding media for wear and tear, lubricating moving parts, and monitoring mill parameters are essential maintenance practices.
In case of operational issues, troubleshooting should focus on identifying the root cause of the problem. Common issues include uneven wear on grinding media, blockages in material feed systems, and fluctuations in power supply.
Grinding mills play a pivotal role in gypsum building powder production lines, transforming gypsum rock into a fine powder suitable for various building applications. Selecting an appropriate grinding mill based on gypsum rock characteristics, desired powder fineness, production capacity, and energy efficiency is crucial for achieving high-quality gypsum building powder.