Hard Rock Quarrying Mining for Ready-Mix Concrete
The construction industry relies heavily on the supply of high-quality aggregates, and one of the most crucial sources is hard rock quarrying. For ready-mix concrete production, these aggregates—comprising crushed stones and gravel—are essential components that determine the strength, durability, and overall performance of the concrete. The process of quarrying and extracting hard rock for the production of aggregates is a highly specialized field, requiring sophisticated techniques, equipment, and an understanding of material properties. This article explores the process of hard rock quarrying and its role in supplying materials for ready-mix concrete.
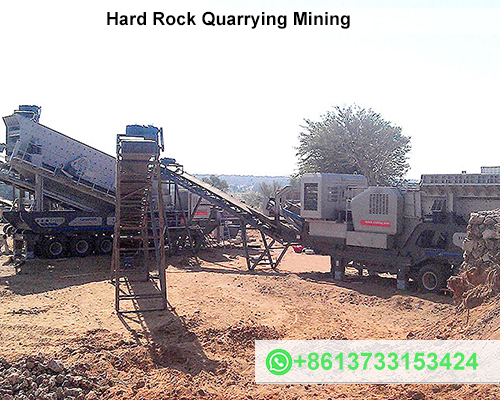
1. The Importance of Aggregates in Ready-Mix Concrete
Ready-mix concrete is a standardized blend of cement, water, fine aggregates (sand), and coarse aggregates (crushed stone or gravel). The quality of the aggregates used in concrete significantly impacts its characteristics, such as compressive strength, workability, and durability. In particular, hard rock aggregates are often preferred because they provide a more robust and durable end product. Hard rock is dense and stable, which is ideal for ensuring that the concrete mix withstands environmental stresses, including freeze-thaw cycles, abrasion, and chemical exposure.
Types of Aggregates:
- Fine Aggregates: These are typically sand-sized particles that fill the gaps between larger aggregates, contributing to the workability and cohesiveness of the concrete.
- Coarse Aggregates: These consist of larger fragments of rock, typically ranging from 3/8 inch to 2 inches in diameter. Hard rock quarrying typically focuses on producing these larger aggregates from rocks such as granite, basalt, limestone, and sandstone.
2. Hard Rock Quarrying Process
Hard rock quarrying is a multi-step process that involves several key stages to extract and prepare rock for use as aggregates in ready-mix concrete. This process involves the following steps:
a) Site Selection and Exploration
Before the quarrying process begins, geologists and engineers perform a thorough analysis of potential sites to ensure the presence of high-quality rock formations suitable for aggregate production. The rock is evaluated for its strength, hardness, and overall composition. Site access, environmental impact assessments, and regulatory considerations are also important factors in the planning process.
b) Drilling and Blasting
Once a site is chosen, the next step is drilling and blasting to break up the hard rock. Since the rock is often too solid to be extracted with conventional machinery, explosives are used to fragment the material into smaller, manageable pieces. Blasting techniques are carefully controlled to ensure safety and minimize environmental disruption. Modern quarrying operations use precise, controlled detonations that reduce vibration and dust, helping to meet environmental regulations.
c) Excavation and Transport
After the blasting, large machinery such as excavators and bulldozers are used to remove the fragmented rock from the quarry face. The material is then transported using dump trucks or conveyor belts to crushers, where it is processed into various sizes of aggregate. The crushed material is sorted and stockpiled based on size and quality to meet specific requirements for concrete production.
d) Crushing and Screening
Crushing is a critical step in producing aggregates. The blasted rock is loaded into crushers, which reduce it into smaller sizes suitable for use in concrete. There are several types of crushers used, including jaw crushers, cone crushers, and impact crushers. After crushing, the material is screened to separate fine aggregates from coarse aggregates. This screening ensures that the final product is uniform and meets the required grading specifications for concrete production.
e) Washing and Sorting
For high-quality concrete, particularly in regions where aggregate purity is crucial, washing and sorting are additional steps in the processing chain. Washing removes dust, clay, and other impurities from the aggregates, ensuring that the final product is clean and does not negatively affect the concrete mix. Sorting ensures that the aggregates meet the required size distribution for specific applications.
3. Environmental and Sustainability Considerations
Quarrying operations, while necessary for aggregate production, can have significant environmental impacts. These include habitat disruption, dust emissions, water usage, and noise pollution. To mitigate these effects, modern quarries employ a range of sustainable practices:
- Reclamation: Many quarries follow a reclamation plan, which aims to restore the site once quarrying has ceased. This might include replanting vegetation, creating wildlife habitats, or repurposing the site for recreational use.
- Dust and Noise Control: Advanced dust suppression systems, such as water sprays and dust collectors, are commonly used to minimize airborne particles. Noise control measures, such as strategically placed barriers or the use of quieter machinery, also help reduce the impact on surrounding communities.
- Energy Efficiency: Modern quarries invest in energy-efficient equipment, renewable energy sources, and optimized transportation routes to reduce their carbon footprint.
4. The Role of Technology in Modern Quarrying
The quarrying industry has seen significant technological advancements in recent years. Automation, data analytics, and remote monitoring have all contributed to increased efficiency, safety, and sustainability in operations.
- Automation and Robotics: Automated drilling rigs, trucks, and crushers help streamline the extraction process, reducing human labor and enhancing precision.
- Geospatial Mapping and Data Analytics: Advanced technologies such as LiDAR (Light Detection and Ranging) and GPS-based systems enable quarry operators to map rock formations accurately, improving the planning and excavation stages.
- Drones and Remote Sensing: Drones are increasingly used to monitor quarry sites, offering real-time data on stockpiles, quarry faces, and overall site conditions.
5. Conclusion
Hard rock quarrying plays a crucial role in the production of high-quality aggregates for ready-mix concrete. By extracting and processing hard rock, quarries provide the necessary raw materials for constructing everything from residential buildings to large infrastructure projects. The process, while complex, is essential for meeting the demands of modern construction, and ongoing advances in technology and sustainability practices continue to improve the efficiency and environmental footprint of these operations.
In the future, as demand for concrete and construction materials grows, the quarrying industry will continue to innovate, balancing the need for quality aggregates with a commitment to sustainability and responsible resource management.