How to Select a Rock Crusher for 50-800 TPH?
Selecting the right rock crusher for your project is crucial to achieving optimal performance and cost-efficiency. Whether you’re working in a mining, construction, or aggregate production environment, your choice of a rock crusher impacts productivity, material handling, and operating costs. For applications with capacity requirements ranging from 50 to 800 tons per hour (TPH), understanding the key factors involved in the selection process can help you choose the most suitable crusher for your needs. This guide outlines the steps and considerations to make when selecting a rock crusher for a capacity range of 50-800 TPH.
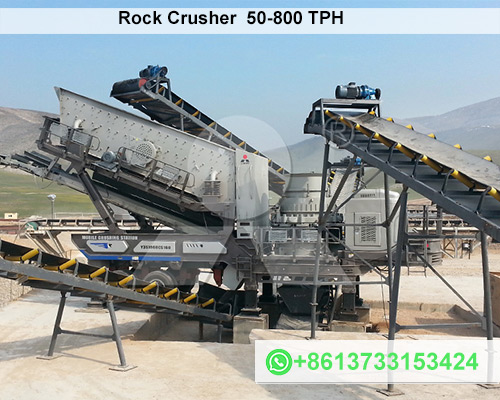
Key Factors to Consider When Selecting a Rock Crusher
- Material Type and HardnessThe material you’re processing plays a critical role in choosing the right crusher. Rocks and ores vary in hardness and abrasiveness, which directly impacts the type of crusher you’ll need.
- Soft to Medium-Soft Materials: If you’re processing softer materials like limestone, coal, or gypsum, impact crusher and primary jaw crusher ideal.
- Hard and Abrasive Materials: For harder materials like granite, basalt, and iron ore, jaw crusher or cone crusher more appropriate because they can withstand high crushing forces and minimize wear.
- Capacity Requirements (50-800 TPH)The required throughput will determine the size and type of rock crusher you need. Here’s a breakdown:
- 50-100 TPH: For smaller-scale operations or projects, jaw crusher, impact crusher, or small cone crusher typically used. These can handle modest capacities and are ideal for mobile setups.
- 100-300 TPH: Medium-capacity projects will likely benefit from larger jaw crusher or cone crusher with a wider feeding size and higher throughput.
- 300-800 TPH: For large-scale operations, heavy-duty crusher like cone crusher, gyratory crusher, or impact crusher with a high-capacity output are necessary. These crusher typically used in large mining or quarrying operations, processing hard materials.
- Type of CrusherSelecting the right type of crusher is one of the most important decisions for a specific project. Here are the most common types of crusher:
- Jaw Crusher: Best suited for primary crushing, jaw crusher can handle a wide range of materials and deliver large capacities, making them ideal for operations ranging from 50 to 800 TPH. Their robust design enables them to crush even the hardest rocks.
- Cone Crusher: Often used for secondary or tertiary crushing, cone crusher provide a high reduction ratio and produce finely graded material. They are particularly efficient for hard and abrasive materials and can operate across a wide range of capacities, from medium (100 TPH) to large-scale operations (800 TPH).
- Impact Crusher: These crusher ideal for materials that are softer, such as limestone, or for recycling applications like concrete and asphalt. Impact crusher offer excellent cubicity and are typically used in lower capacity applications (50-400 TPH).
- Gyratory Crusher: For large, high-capacity applications (over 400 TPH), gyratory crusher offer high throughput and are used in primary crushing for extremely hard and abrasive materials.
- Feeding SizeThe size of the feed material is another critical factor. Different crusher have different feed size limitations, which affect their ability to handle large rocks or material blocks.
- Jaw Crusher: These are well-suited for large feed sizes, handling up to 1,500 mm blocks, making them ideal for primary crushing of large, unprocessed rock.
- Cone Crusher: While effective at reducing material size, they typically handle smaller feed sizes compared to jaw crusher. The feed should be pre-screened or pre-crushed for optimal performance.
- Impact Crusher: Often used for medium to small feed sizes, generally handling material up to 800 mm. Impact crusher ideal for materials that break along natural lines.
- Desired Output SizeThe final product’s size is crucial for meeting project specifications. Different crusher produce different product shapes and sizes, so it’s essential to match your crusher to your desired output.
- Cone Crusher: Produce well-shaped, fine materials that are perfect for secondary and tertiary crushing.
- Jaw Crusher: These crusher typically produce coarser material and are ideal for primary crushing.
- Impact Crusher: Known for their excellent cubicity, impact crusher deliver a uniform product, particularly useful in applications requiring consistent size and shape.
- Mobility and Site ConditionsDepending on the site conditions and how frequently the crusher needs to be relocated, you may need either a mobile or stationary crushing unit.
- Mobile Crusher: These are perfect for operations that require frequent relocation or for projects that span across different sites. Mobile crusher typically have lower capacities (50-500 TPH), but they offer flexibility and ease of setup.
- Stationary Crusher: For larger, long-term operations, stationary crusher provide higher capacity and are more cost-effective for large-scale crushing (up to 800 TPH).
- Energy Efficiency and Operating CostsEnergy consumption and operating costs are essential factors in choosing the right crusher. Modern crusher equipped with advanced technologies that reduce power consumption and increase operational efficiency.
- Cone Crusher: Offer energy-efficient crushing with high productivity.
- Jaw Crusher: While powerful, they can consume more energy if not properly sized to the operation’s capacity.
- Impact Crusher: Can be energy-efficient for softer materials but may be less efficient for harder, more abrasive materials.
- Maintenance and Spare Parts AvailabilityCrusher wear parts—such as jaws, mantles, and impact hammers—require regular maintenance, especially when processing hard or abrasive materials. Choosing a crusher with easy access to spare parts and local support can significantly reduce downtime.
- Jaw and Cone Crusher: These are generally easier to maintain, with spare parts widely available, especially for popular brands.
- Impact Crusher: Require more frequent maintenance due to wear, but modern models are designed for easy access and part replacement.
Recommended Crusher for 50-800 TPH Range
- 50-150 TPH
- Primary Jaw Crusher (50-150 TPH): Ideal for small-scale mining, road construction, and recycling projects.
- Mobile Cone Crusher: For secondary and tertiary crushing with medium output and excellent mobility.
- 150-300 TPH
- Jaw Crusher with Pre-Screen (150-300 TPH): Excellent for medium-scale operations needing to handle larger feed sizes and variable materials.
- Cone Crusher or Impact Crusher (150-300 TPH): Best for producing fine material for aggregate or construction needs.
- 300-500 TPH
- Heavy-Duty Jaw Crusher (300-500 TPH): Ideal for large quarrying and mining operations requiring robust crusher to handle hard and abrasive materials.
- Secondary Cone Crusher (300-500 TPH): Provides high-quality secondary and tertiary crushing for finer product sizes.
- 500-800 TPH
- Gyratory Crusher (500-800 TPH): The best option for high-capacity, hard material processing operations in large-scale mining or quarries.
- High-Capacity Cone Crusher (500-800 TPH): Ideal for secondary and tertiary crushing with high output and low operating costs.
Conclusion
Selecting the right rock crusher for 50-800 TPH applications requires careful consideration of material type, crusher type, capacity, and site conditions. Whether you need a mobile unit for flexible operations or a stationary crusher for high-capacity processing, matching your crusher’s features to your project’s specific needs is essential. By factoring in material characteristics, feed size, desired output, and long-term operational goals, you can choose a crusher that maximizes productivity, efficiency, and profitability.