Quarry Crusher Types
In the construction and mining industries, efficient crushing operations are critical for processing large rocks into smaller, usable aggregates. Crusher play an essential role in this process, converting quarried material into specific sizes for use in construction projects, road-building, and other applications. Quarry crusher come in various types, each with unique features, benefits, and applications. In this article, we’ll explore the most common types of quarry crusher, examining how each functions and what scenarios they’re best suited for.
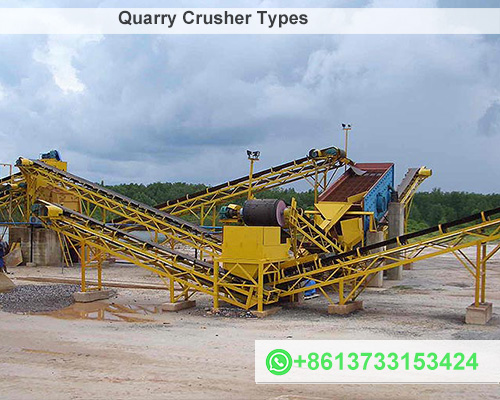
1. Jaw Crusher
Overview:
Jaw crusher is primary crusher commonly used in quarrying operations. This machine uses compressive force to break down large materials, making it suitable for hard and abrasive rocks.
How It Works:
The jaw crusher has two plates, one stationary and one moving. As the moving plate advances towards the stationary plate, the material is crushed in the gap between them, producing smaller pieces. This cycle continues until the desired size is achieved.
Advantages:
- High reduction ratio
- Suitable for hard materials (e.g., granite, basalt)
- Simple design and low maintenance
Best For:
Primary crushing stages, especially with hard and abrasive materials.
2. Cone Crusher
Overview:
Cone crusher is widely used for secondary and tertiary crushing. They work by compressing the material between an eccentrically rotating cone and a fixed cone, producing fine and uniform aggregates.
How It Works:
Material enters the cone from the top and gets trapped in a crushing cavity. As the cone rotates, the space between it and the concave (the fixed cone) narrows, crushing the material into smaller pieces.
Advantages:
- Produces a uniform shape and size
- Handles medium to very hard materials
- High efficiency in closed-circuit applications
Best For:
Secondary and tertiary crushing stages, producing finely crushed stone for aggregate.
3. Impact Crusher
Impact crusher is divided into two main categories: horizontal shaft impact (HSI) crusher and vertical shaft impact (VSI) crusher. Each type is designed to handle different materials and offer unique advantages.
a. Horizontal Shaft Impact (HSI) Crusher
Overview:
HSI crusher is ideal for materials with low to medium hardness and are commonly used in recycling and construction applications.
How It Works:
The HSI crusher uses a high-speed rotor equipped with blow bars to strike and break the material against impact plates or curtains. This action creates a high-speed impact force that fractures the material.
Advantages:
- Good for softer materials like limestone
- Produces well-shaped aggregates
- Capable of handling large feed sizes
Best For:
Soft to medium-hard materials, primary and secondary crushing.
b. Vertical Shaft Impact (VSI) Crusher
Overview:
VSI crusher is used primarily for producing high-quality, cubical-shaped aggregates and sand. They are widely used in construction and road-building industries.
How It Works:
In a VSI crusher, material is fed vertically into a spinning rotor, which throws it outward against anvil or rock-lined surfaces. This unique “rock-on-rock” crushing action results in a high-quality product with consistent particle shape.
Advantages:
- Produces fine, well-shaped material
- Great for sand production
- Versatile with high reduction rates
Best For:
Sand and gravel production, creating high-quality aggregates for asphalt and concrete applications.
4. Gyratory Crusher
Overview:
Gyratory crusher is another primary crusher type, often used for large-scale mining and quarrying applications. They handle large feed sizes, reducing them to manageable sizes for further processing.
How It Works:
A gyratory crusher operates with a central spindle and a concave surface. Material is fed from the top, where it is crushed as it falls into the narrowing gap between the spindle and the concave.
Advantages:
- Handles very large feed sizes
- Continuous operation with high throughput
- Long-lasting with lower operating costs for large quantities
Best For:
Primary crushing in large-scale operations, particularly in mining.
5. Roll Crusher
Overview:
Roll crusher is typically used for fine crushing stages and are effective for soft to medium-hard materials, like coal and limestone.
How It Works:
Roll crusher consist of two parallel, rotating rolls that crush the material as it passes through them. The crushing action is achieved by compressing the material between the two rolls.
Advantages:
- Minimal dust production
- Consistent size reduction
- Low fines production
Best For:
Soft or medium-hard materials, achieving consistent particle sizes in small-scale production.
6. Hammer Crusher
Overview:
Hammer crusher, also known as hammer mills, are effective for medium-hard to soft materials. They are commonly used for limestone and gypsum processing in cement plants.
How It Works:
Hammer crusher use high-speed rotating hammers to impact and break down the material. The hammers crush the material until it reaches the desired size, then expel it through a grid or grate.
Advantages:
- High crushing ratio
- Simple structure, easy to maintain
- Effective for softer materials
Best For:
Soft to medium-hard materials, particularly in the cement industry and for materials with low abrasiveness.
Choosing the Right Quarry Crusher
Selecting the right type of crusher for a quarry operation depends on various factors, including:
- Material Hardness: Harder materials generally require stronger, more durable crusher like jaw and cone crusher.
- Desired Output Size and Shape: VSI and impact crusher is ideal for producing finer, well-shaped materials.
- Production Volume: Large-scale operations benefit from robust, high-capacity crusher like gyratory and cone crusher.
Conclusion
Each type of quarry crusher offers distinct advantages, depending on the nature of the material and the needs of the operation. Understanding these differences is crucial for selecting the right equipment, maximizing productivity, and minimizing operating costs. Whether a jaw crusher for primary crushing, a cone crusher for secondary stages, or a VSI crusher for creating high-quality sand, choosing the right crusher ensures efficient processing and optimal output quality for quarry operations.