Layout of Stone Crusher Plant
Introduction
The design and layout of a stone crusher plant is a critical factor for achieving efficient and effective production in the crushing process. A well-designed layout ensures the smooth flow of material, minimizes operational bottlenecks, reduces energy consumption, and improves overall productivity. The process of designing a stone crusher plant involves various elements, including machinery selection, plant capacity, material handling, and space optimization. In this article, we will explore the key components and considerations that go into planning the layout of a stone crusher plant.
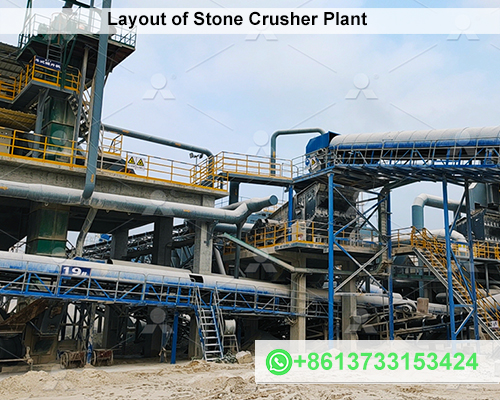
1. Components of a Stone Crusher Plant
A typical stone crusher plant consists of several key components that work together to process raw materials (usually rocks and stones) into smaller aggregates. The main components are:
- Feeding System: The first step in the process is the feeding system, which delivers raw materials (such as stone, gravel, or rocks) to the crusher. This could involve a vibrating feeder or a conveyor belt, depending on the setup.
- Primary Crusher (Jaw Crusher or Gyratory Crusher): This is the first stage of crushing, where large, unprocessed materials are reduced to a manageable size. Jaw crushers or gyratory crushers are typically used in this stage.
- Secondary Crushers (Cone Crusher or Impact Crusher): After the primary crushing, the material often needs further reduction in size. Secondary crushers, like cone crushers or impact crushers, are used to reduce the size of the material to the required specification.
- Tertiary Crushers (Vertical Shaft Impact Crusher or Hammer Crusher): In some cases, further crushing is required to achieve a finer grade of material. Tertiary crushers are used to produce sand or very fine aggregates.
- Screening System: Once the material has been crushed to the desired size, the screening process separates different sizes of aggregates using vibrating screens. This is essential to ensure that materials are sorted into specific grades for various construction applications.
- Conveying System: Conveyor belts are used to transport materials from one stage of the plant to the next. Efficient material handling is essential for ensuring a smooth flow of production.
- Dust Control and Waste Management: Dust suppression systems, such as water sprays and bag filters, are employed to minimize airborne dust. Waste management includes the collection and disposal of unused or non-usable material.
2. Key Considerations in the Layout Design
The layout of a stone crusher plant involves more than just the arrangement of machinery. A good layout optimizes the space and ensures smooth operational flow. Here are the key factors to consider when designing the layout of a stone crusher plant:
a. Space Optimization
Efficient use of space is crucial for the success of the plant. The equipment should be arranged to minimize the travel distance of materials, thus reducing transportation time and costs. For example, placing crushers close to the feed material sources and screening units close to the crushers can reduce material handling costs.
In addition, the design should leave enough space for future expansion and allow for the movement of maintenance personnel and equipment.
b. Flow of Material
The layout should ensure a continuous flow of material from one process to the next. The material should be fed into the plant in a steady and controlled manner, and the crushing process should be optimized to reduce downtime. Each section (primary, secondary, tertiary) should be arranged in a way that minimizes the distance material must travel, which reduces both handling costs and material wastage.
c. Energy Efficiency
Energy consumption is one of the biggest operational costs in a stone crusher plant. By designing the plant layout carefully, it’s possible to reduce energy consumption and maximize efficiency. For example, positioning crushers and screens in such a way that the material flows under gravity can help reduce the need for additional energy input, such as conveyors or additional crushers.
d. Dust Control and Environmental Impact
Dust and noise pollution are significant concerns in stone crushing plants. Effective dust control systems must be integrated into the layout to reduce the impact on the surrounding environment. These systems typically include water spraying systems, dust collection units, and sealed conveyors.
Noise reduction can be achieved by isolating noisy equipment in soundproof enclosures and using noise dampening materials where possible.
e. Safety and Access for Maintenance
The layout should prioritize worker safety and facilitate easy maintenance of machinery. Providing sufficient space for safe movement of workers, ease of access to machines for repairs, and proper ventilation in enclosed areas are critical considerations.
In addition, emergency access routes and safety measures (such as fire extinguishers, emergency stops, and signage) should be clearly marked in the layout.
f. Transportation and Storage of Finished Products
The finished material must be properly stored and transported to the next phase, such as stockpiling or dispatch. The layout should include provisions for stockpiles, finished product bins, and transportation facilities. Ensuring that these areas are strategically placed near the crushing units can help streamline the operation.
g. Water and Waste Management
A stone crusher plant often requires water for dust suppression and cooling systems. The layout should account for water sources, storage, and efficient distribution throughout the plant. Proper waste management plans should be implemented to handle non-usable material and avoid environmental contamination.
3. Sample Layout Plan for a Stone Crusher Plant
A typical stone crusher plant layout might look like the following:
- Raw Material Storage Area: Located near the plant entrance for easy access.
- Feeding and Conveying System: A vibrating feeder delivers material to the primary crusher, typically located close to the raw material stockpile.
- Primary Crusher (Jaw Crusher): Located near the feeding system for initial size reduction.
- Secondary Crusher (Cone Crusher or Impact Crusher): Positioned to receive material from the primary crusher.
- Screening System: Includes multiple vibrating screens to separate various sizes of aggregates.
- Tertiary Crusher (if needed): If a finer aggregate is required, a tertiary crusher may be included.
- Stockpiles: Finished products like sand, gravel, and aggregates are stockpiled or transferred to storage bins.
- Dust Control Systems: Positioned at various points, including near crushers and screens.
- Transport Area: For the dispatch of finished products to the customer or storage for later use.
4. Conclusion
The layout of a stone crusher plant is a fundamental aspect of its operation. A well-thought-out layout not only maximizes productivity but also ensures that the plant operates efficiently, safely, and in compliance with environmental standards. By considering factors like material flow, energy efficiency, space utilization, and environmental impact, you can design a stone crusher plant that minimizes costs while maximizing output and minimizing downtime. Whether building a new plant or upgrading an existing one, investing time and resources into designing a proper layout will lead to long-term operational success.