Optimized crusher selection for the cement industry
The properties of raw materials required for the cement production differs at a wide range. The limestone deposits used today as base material show very different prop- erties regarding hardness, abrasiveness and stickiness. To optimize the crushing and at the same the investment and operating costs different types of crusher are avail- able on the market.This paper should give a short overview how to optimize the crusher selection for the cement industry.
Material Characteristics
Before choosing a crusher for a certain application the quarry and especially the characteristics of the raw material has to be analyzed.Of fundamental significance is the hardness of the material to be crushed. To de- scribe this property the compressive strength, the Los Angeles Index or the Mohs Hardness should be determined.In addition the abrasiveness of the material has to be described. This can be done by determining the Silica content, the free quartz content and the abrasion index.Of the same importance is to express the stickiness of the material. For this reason the moisture, the clay content and in very difficult applications the handling coefficient (shear test) has to be investigated.Based on this values and characteristics of the material the overview on page 3 al- lows to make a pre-choice of the required crusher.
Selection Criteria
Primary crushing of limestone for the cement production requires high crushing ratios to reduce the run of mine material in one step down to the required grain size distribu- tion (approx. 0 – 25/80mm) for the raw material mills. One step crushing should al- ways be the aim to keep on one side investment costs and on the other side mainte- nance time and costs down.
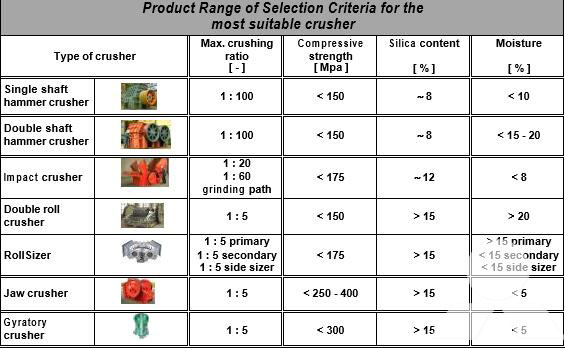
According to the above overview one step crushing can be achieved by operating hammer crushers and impact crushers. These crushers are fast running machines with a high kinetic energy resulting in strong impact forces and high crushing ratios. The allowable compressive strength of 150 Mpa is normally sufficient for most of the limestone applications.
The silica content is an important issue to be considered when using hammer or im- pact crushers. Due to the high speed of the rotors the crushing tools (hammers or impact bars) are sensitive to wear. The limit for these machines is between 8%-12% silica content. Before making a final decision the abrasiveness of the raw material has to be analyzed very carefully to avoid suffering under high maintenance costs. If the silica content is above the mentioned values a more ‘gentle’ crushing system with lower crushing ratios in two steps has to be considered.
As final characteristics the moisture content has to be taken into account. While the impact crusher is limited by a moisture content of max. 8% the double shaft hammer crusher can still be operated up to a moisture content of up to 20%. This special fea- ture allows to charge limestone and sticky materials like e.g. clay at the same time to obtain a pre-homogenization already in the crusher.
As soon as the silica or the moisture content is too high to operate one step crushing systems with hammer or impact crushers two step crushing systems has to be in- stalled to reduce the run of mine material to the requested grain size distribution for the raw material mills. Possible crushers for these two step systems are Double Roll Crushers, RollSizers, Jaw Crushers and Gyratory Crushers which are all able to op- erate in abrasive material. But while the crushing ratio of these crushers is approx. the same (1:5) there ability to crush hard and/or wet material differs.
Jaw crusher and gyratory crushers are crushing the material by high pressure and are suit- able for hard materials with a compressive strength of up to 400 Mpa. The compres- sive strength of limestone is normally below 150 Mpa and these crushers are there- fore mainly used if the raw material is very abrasive. On the other side these ma- chines are sensitive to high moisture contents which have to be considered very care- fully.
The above made explanations about the different types of crushers show that for every kind of limestone a suitable crusher combination exists to produce the required grain size distribution. But not only for limestone also for the necessary additives (like e.g. clay, lime, puzzolan, sandstone, iron ore, shist,….) with there different material characteristics the proper crusher method can be optimized according to the material properties.