Rock Sand Making Machine
In the construction industry, sand plays an indispensable role as a key component in concrete, mortar, asphalt, and other building materials. Traditionally, natural sand from riverbeds and coastlines has been the primary source of this essential resource. However, with increased environmental concerns and the depletion of natural sand reserves, the demand for alternatives has surged. One such alternative is manufactured sand, commonly known as rock sand, which is produced by crushing rocks into fine particles. The rock sand making machine is at the heart of this transformation process, turning large rock masses into fine sand that can be used in construction projects.
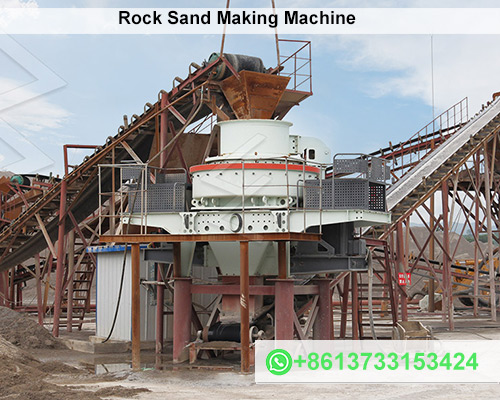
The Growing Need for Manufactured Sand
Due to the extensive use of natural sand in construction and infrastructure development, the pressure on natural resources has been rising. Mining of river sand has led to environmental degradation, such as erosion, loss of biodiversity, and habitat destruction. This growing ecological impact has driven a shift toward sustainable alternatives like manufactured sand.
Rock sand, also called M-sand, offers an eco-friendly and economically viable substitute for natural sand. The rock sand making machine makes this transformation possible by efficiently converting rock into high-quality sand suitable for concrete production, road construction, and other applications.
What is a Rock Sand Making Machine?
A rock sand making machine is a specialized piece of equipment designed to crush large rocks into fine particles of sand-like material. These machines are engineered to break down the toughest rocks and minerals through a variety of mechanisms, including compression, impact, and grinding, depending on the type of machine used. The resulting product is finely crushed rock material that mimics the properties of natural sand.
The machine typically incorporates a series of crusher and screening systems, ensuring that the sand produced meets specific particle size requirements for various construction uses.
How Rock Sand Making Machines Work
- Primary Crushing: Large rocks, usually obtained from quarries, are fed into a primary crusher, such as a jaw or cone crusher. This initial crushing stage reduces the size of the rocks to medium-sized fragments.
- Secondary Crushing: The crushed rocks from the primary stage are then fed into secondary crusher, such as vertical shaft impact (VSI) crusher. This stage breaks down the material into finer particles suitable for producing sand.
- Screening and Grading: The crushed rock particles are passed through vibrating screens that separate the material into different size fractions. The particles meeting the required size for sand are collected, while larger fragments are recirculated through the crusher for further refinement.
- Sand Washing (optional): Depending on the specific application, the rock sand may undergo a washing process to remove any impurities, such as clay, dust, or organic materials. This step ensures that the final product is clean and ready for construction use.
Types of Rock Sand Making Machines
Different machines are used depending on the desired size and shape of the sand, as well as the type of rock being processed. Common types of rock sand making machines include:
- Vertical Shaft Impact Crusher (VSI): These are the most widely used machines for producing high-quality sand. VSI crusher operate by propelling rock against a hard surface, fracturing it into fine particles.
- Hammer Mills: Hammer mills crush rocks through high-speed impact with rotating hammers. They are ideal for producing smaller, uniform-sized particles and can be adjusted for different grain sizes.
- Cone Crusher: These machines use a rotating cone inside a bowl to crush rocks into sand-sized particles. They are typically used for secondary and tertiary crushing.
- Jaw Crusher: These crusher is often used for primary crushing, where the rocks are reduced to a manageable size before being further processed into sand.
Benefits of Using a Rock Sand Making Machine
- Sustainable Alternative to Natural Sand: As natural sand sources dwindle, using rock sand reduces the ecological damage caused by sand mining from rivers and beaches.
- High Quality and Consistent Output: Rock sand making machines produce uniform and high-quality sand that meets the standards required for concrete and asphalt production. Unlike natural sand, which may vary in particle size and composition, manufactured sand can be tailored to specific requirements.
- Cost-Effective: Rock sand is often more affordable than natural sand, particularly in regions where natural sand is scarce. By using locally sourced rock, transportation costs can be minimized, making the overall construction process more economical.
- Improved Concrete Strength: Manufactured rock sand is known for having a cubical shape and fewer impurities, leading to better bonding properties in concrete. This results in higher strength and durability in construction projects.
- Energy Efficient: Modern rock sand making machines are designed for energy efficiency, reducing the overall environmental impact of the sand production process.
Applications of Rock Sand
- Concrete Production: Rock sand is widely used as a fine aggregate in concrete mixes. Its consistency and quality make it an excellent choice for producing strong, durable concrete for buildings, roads, bridges, and other infrastructure projects.
- Road Construction: In road construction, rock sand is mixed with asphalt to create a strong, stable surface for highways, driveways, and pavements.
- Masonry Work: Rock sand is used in the production of mortar and plaster, providing a fine, uniform material that enhances the finish of masonry and plasterwork.
- Landscaping: Manufactured sand is also used for various landscaping applications, including filling, leveling, and creating pathways.
Challenges and Solutions in Rock Sand Production
One of the main challenges of using rock sand is the potential variability in rock types, which can affect the quality and composition of the sand produced. To overcome this, advanced screening and grading systems are employed to ensure uniform particle size. Additionally, fine-tuning the crusher for specific types of rock helps to optimize output.
Moreover, dust generation during the crushing process is a concern. However, modern rock sand making machines incorporate dust suppression systems, improving air quality and reducing environmental impact.
Conclusion
The rock sand making machine is a game-changer for the construction industry, providing an eco-friendly and cost-effective alternative to natural sand. By converting rocks into high-quality manufactured sand, these machines support sustainable development, reduce environmental degradation, and ensure a steady supply of vital construction materials. As the demand for sand continues to grow, rock sand making machines will play an increasingly important role in ensuring a sustainable and resilient construction industry.