What are the modules of VU aggregate optimization system?
Material Feed Size: 0-25mm
Production Capacity: 75-270t/h
Application Scope: Supporting sand production for mixing plants, dry mortar, cement product plants, aggregate mines, and large-scale construction projects.
Applicable Materials: Inexpensive and readily available tailings, waste materials, construction debris, stone chips, and guami stones, etc.
The VU Dry Sand Making System consists of the VU Impact Crusher, VU Modulation Control Screen, VU Particle Shape Optimization Machine, Wetting Mixer, Dust Removal & Powder Collection Module, and Central Control System.
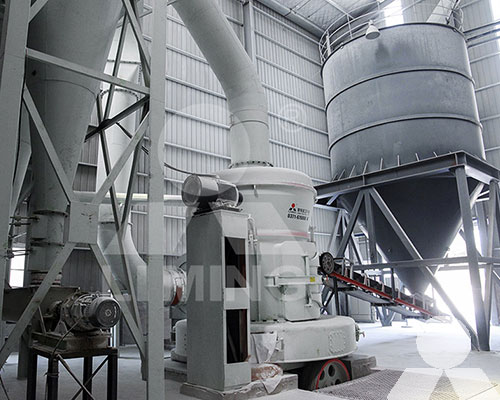
The raw materials are elevated and fed into the VU Impact Crusher, where they undergo high-frequency impact grinding. The processed materials then enter the Modulation Control Screen for classification. Based on the screening results, the oversize materials return to the VU Impact Crusher for further processing, while the undersize materials enter the VU Particle Shape Optimization Machine for reshaping. Meanwhile, the entire Modulation Control Screen adjusts the material’s powder content through wind selection via the dust collector. Finally, the materials discharged from the VU Particle Shape Optimization Machine are evenly mixed in the Wetting Mixer.
After processing through the VU Aggregate Optimization System, the output consists of well-graded, round-shaped particles with controllable powder content, as well as dry, clean, and high-value stone powder (applicable range determined by the raw materials).
Advantages of VU Aggregate Optimization System:
- The system employs a highly compact tower layout, significantly reducing the footprint. The entire production and screening process takes place in a fully enclosed environment, eliminating concerns about dust emission. The dry production and screening process prevent the generation of wastewater and sludge.
- “Stone-on-stone” centrifugal crushing method is used, where the rotor crushes, shapes, and grinds the incoming materials, achieving a combination of crushing and high-density crushing. This effectively improves the particle shape of the finished sand and increases the proportion of fine aggregates.
- By combining air classification technology with vibrating screening technology, material feeding, linear screening, and negative pressure dust removal are carried out within a single chamber. The central control system can adjust the total air volume online, enabling control of the powder content in the finished sand and fine modulus adjustment.
- VU Sand has needle-like particles eliminated, and the surface consists mainly of spherical and polyhedral shapes, with indistinct edges and corners. It closely resembles the high-quality natural sand. Without changing any hardware, the system can achieve fine modulus adjustments from 2.3 to 2.9 and powder content adjustments between 5% to 13%.
Please note that some technical terms may have specific translations depending on the industry, so it’s always best to use industry-standard terms if available.