Attritor grinding machine layout for silica sand
Attritor grinding machines are a type of wet grinding machine that is used to grind a variety of materials, including silica sand. They are characterized by a rotating drum that contains the material to be ground and a grinding medium, such as steel balls or rods. The material and the grinding medium are mixed together by the rotating drum, and the grinding action occurs as the material is rubbed against the grinding medium.
The layout of an attritor grinding machine for silica sand will vary depending on the specific application. However, there are some general principles that can be followed.
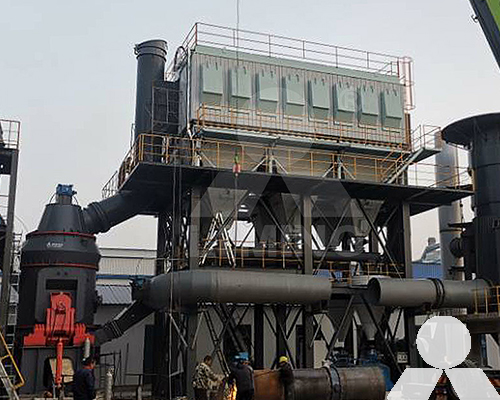
The first step is to select the correct attritor. The size and capacity of the attritor will depend on the amount of silica sand to be ground and the desired particle size.
The next step is to select the correct grinding medium. The size and type of grinding medium will also affect the particle size of the ground silica sand.
Once the attritor and grinding medium have been selected, the next step is to design the feed system. The feed system must ensure that the silica sand is evenly distributed throughout the attritor.
The final step is to design the discharge system. The discharge system must be able to efficiently remove the ground silica sand from the attritor.
Here is a more detailed overview of each of these steps:
Selecting the attritor
The size of the attritor will depend on the amount of silica sand to be ground. The capacity of the attritor is typically expressed in terms of the volume of material that can be ground per hour.
The type of attritor will also affect the particle size of the ground silica sand. Ball mills are typically used to grind silica sand to a fine particle size, while rod mills are typically used to grind silica sand to a coarser particle size.
Selecting the grinding medium
The size of the grinding medium will affect the particle size of the ground silica sand. Smaller grinding media will produce a finer particle size, while larger grinding media will produce a coarser particle size.
The type of grinding medium will also affect the wear rate of the attritor. Steel balls are the most common type of grinding medium, but they can be expensive and wear quickly. Ceramic balls are more expensive than steel balls, but they are less likely to wear.
Designing the feed system
The feed system must ensure that the silica sand is evenly distributed throughout the attritor. This can be accomplished by using a hopper or a screw feeder.
Hopper feeders are the simplest type of feed system. They consist of a hopper that is located above the attritor. The silica sand flows out of the hopper by gravity.
Screw feeders are more efficient than hopper feeders. They use a screw to move the silica sand into the attritor.
Designing the discharge system
The discharge system must be able to efficiently remove the ground silica sand from the attritor. This can be accomplished by using a screen or a cyclone.
Screens are the most common type of discharge system. They use a screen to separate the ground silica sand from the grinding medium.
Cyclones are more efficient than screens at separating the ground silica sand from the grinding medium. They use centrifugal force to separate the two materials.
Attritor grinding machines are a versatile tool that can be used to grind a variety of materials, including silica sand. By carefully designing the layout of an attritor grinding machine, it is possible to achieve the desired particle size and efficiency.