Silica Sand Production Line Supplier In China
Silica sand is a crucial raw material in a wide range of industries, including glassmaking, ceramics, construction, and foundry. The production of silica sand involves a series of processes aimed at extracting, processing, and refining the raw material to meet the specific requirements of its end use.
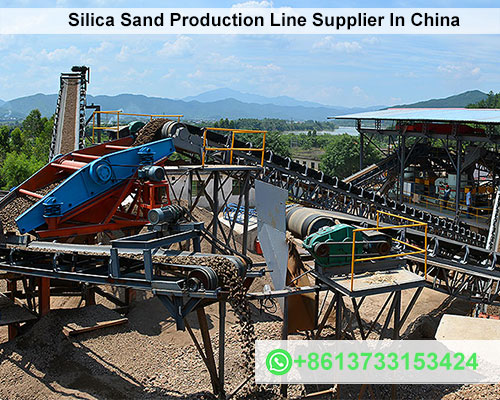
The Processing Stages
The silica sand production line typically consists of the following stages:
- Crushing and Screening: The raw silica ore, often in the form of large rocks or boulders, is initially subjected to crushing using primary and secondary crushers to reduce its size to manageable pieces. This is followed by screening to separate the crushed material into different size fractions.
- Grinding: The screened silica sand is then further processed in grinding mills, such as ball mills or rod mills, to achieve the desired particle size and shape. This stage is particularly important for applications requiring fine silica sand.
- Beneficiation: Impurities, such as clay, iron oxides, and other minerals, are removed from the ground silica sand through a series of beneficiation processes. These may include washing, flotation, and magnetic separation techniques.
- Dewatering and Drying: The beneficiated silica sand is then dewatered to remove excess water using techniques such as hydrocyclones, settling tanks, and filtration systems. The dried sand is finally subjected to drying processes, such as rotary dryers or fluidized bed dryers, to reduce its moisture content to the desired level.
- Grading and Classification: The dried silica sand is graded and classified according to particle size and other quality parameters using screens, classifiers, and air separators. This ensures that the final product meets the specific requirements of the intended application.
- Quality Control: Throughout the production process, rigorous quality control measures are implemented to monitor and maintain the purity, particle size distribution, and other critical properties of the silica sand. This involves sampling, testing, and analyzing the material at various stages of the process.
Factors Affecting Production
The specific configuration and equipment used in a silica sand production line can vary depending on the characteristics of the raw ore, the desired product specifications, and the production capacity requirements. Factors such as the feed size, mineralogical composition, and environmental regulations also influence the design and operation of the production line.
Applications of Silica Sand
The high purity and versatility of silica sand make it an essential material in a diverse range of industries:
Glassmaking: Silica sand is the primary component of glass, forming the structural framework of the material. Its purity and particle size distribution significantly impact the optical properties and strength of the glass.
Ceramics: Silica sand is a major ingredient in ceramic products, including tiles, bricks, and sanitaryware. Its high silica content contributes to the strength, durability, and thermal resistance of ceramics.
Construction: Silica sand is widely used in construction materials such as concrete, mortar, and asphalt. Its inert properties and ability to enhance the strength and workability of these materials make it a valuable component.
Foundry: Silica sand is employed in foundry applications to create molds for casting metal parts. Its refractoriness and ability to form intricate shapes make it suitable for this purpose.
Other Applications: Silica sand also finds applications in sandblasting, filtration, water purification, and various industrial processes.
The silica sand production line plays a crucial role in supplying this essential raw material to various industries. The efficient processing of silica sand ensures the production of high-quality products that meet the diverse needs of end users.