Cone Crusher For Raw Tungsten Processing
Tungsten, known for its exceptional hardness and high melting point, is a critical metal used in various industries, including aerospace, electronics, and mining. To extract and process tungsten efficiently, specialized equipment is required. Among the most important machines in this process is the cone crusher, which plays a vital role in breaking down raw tungsten ore into manageable sizes for further processing.
What is Tungsten and Why is it Important?
Tungsten, also referred to as wolfram, is a rare metal with the highest melting point of all elements (3,422°C or 6,192°F). It is widely used in the production of hard materials, such as tungsten carbide, which is essential for cutting tools, drill bits, and wear-resistant parts. Additionally, tungsten is used in filaments for incandescent light bulbs, electrical contacts, and radiation shielding.
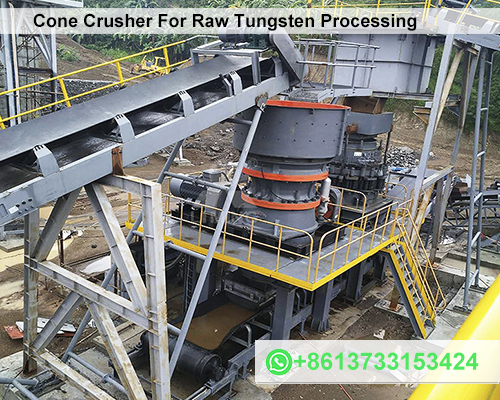
The Role of Crushing in Tungsten Processing
The processing of raw tungsten ore begins with crushing, a critical step that reduces the size of the ore to facilitate further beneficiation. Cone crusher is particularly well-suited for this task due to their ability to handle hard and abrasive materials like tungsten ore. By breaking down the ore into smaller particles, cone crushers enable efficient separation of tungsten from other minerals and impurities.
Why Choose a Cone Crusher for Tungsten Processing?
Cone crushers are widely regarded as one of the most effective crushing machines for processing hard and abrasive materials. Here are some key reasons why they are ideal for tungsten processing:
- High Crushing Efficiency: Cone crushers are designed to deliver high reduction ratios, meaning they can break down large chunks of tungsten ore into smaller, more uniform particles in a single pass.
- Durability: Tungsten ore is extremely hard and abrasive, but cone crushers are built with robust materials and advanced engineering to withstand such demanding conditions.
- Precision and Control: Modern cone crushers come equipped with adjustable settings, allowing operators to control the size of the output material with precision. This is crucial for optimizing downstream processing.
- Low Operating Costs: Cone crushers are designed for energy efficiency and require minimal maintenance, making them a cost-effective solution for tungsten processing.
Types of Cone Crushers for Tungsten Processing
There are several types of cone crushers available, each suited to different stages of the crushing process:
- Spring Cone Crusher: Ideal for secondary crushing, this type of crusher uses a spring mechanism to protect the machine from damage caused by uncrushable materials.
- Hydraulic Cone Crusher: Equipped with hydraulic systems, these crushers offer greater flexibility and control over the crushing process, making them suitable for both secondary and tertiary crushing.
- Compound Cone Crusher: Designed for high productivity, this type of crusher combines the benefits of spring and hydraulic systems, making it a versatile choice for tungsten processing.
Key Considerations When Selecting a Cone Crusher
When choosing a cone crusher for tungsten processing, several factors should be taken into account:
- Ore Characteristics: The hardness, abrasiveness, and size of the tungsten ore will influence the type of cone crusher required.
- Production Capacity: The crusher must be capable of handling the desired throughput to meet production targets.
- Particle Size Requirements: The crusher should be able to produce the desired particle size for downstream processes, such as grinding and separation.
- Maintenance and Support: Opt for a reliable manufacturer that offers robust after-sales support and readily available spare parts.
Benefits of Using a Cone Crusher in Tungsten Processing
- Improved Recovery Rates: Efficient crushing ensures that tungsten particles are liberated from the ore, improving recovery rates during subsequent processing stages.
- Energy Efficiency: Cone crushers are designed to minimize energy consumption, reducing operational costs.
- Versatility: Cone crushers can handle a wide range of materials, making them suitable for various stages of the tungsten processing workflow.
- Consistent Output: The ability to produce uniform particle sizes ensures consistent performance in downstream processes.
Conclusion
The cone crusher is an indispensable tool in the processing of raw tungsten ore. Its ability to efficiently break down hard and abrasive materials into smaller, manageable sizes makes it a critical component in the tungsten production chain. By investing in a high-quality cone crusher, mining operations can enhance their efficiency, reduce costs, and ensure the production of high-grade tungsten concentrates.
In summary, the cone crusher not only simplifies the crushing process but also contributes to the overall sustainability and profitability of tungsten mining and processing operations. With the right equipment, the journey from raw tungsten ore to a valuable industrial resource becomes both efficient and economically viable.