Mobile Cone Crusher For Tungsten Ore Processing
Tungsten, renowned for its exceptional hardness and high melting point, is a critical metal used in industries ranging from aerospace to electronics. However, processing tungsten ore presents significant challenges due to its abrasive nature and the need for precise particle size reduction. Traditional fixed crushing plants often struggle to meet the demands of remote mining sites or dynamic operational requirements. Enter the mobile cone crusher—a game-changing innovation that is transforming tungsten ore processing with its flexibility, efficiency, and adaptability.
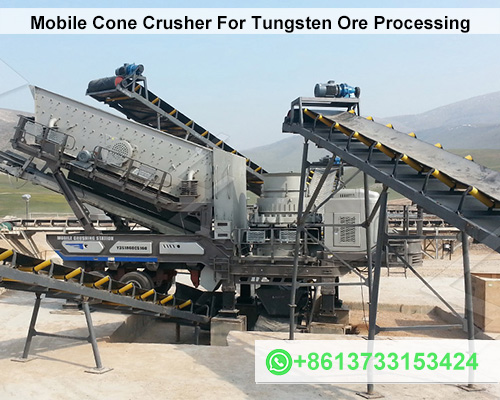
The Challenges of Tungsten Ore Processing
Tungsten ore, primarily found in wolframite and scheelite minerals, requires multi-stage crushing and grinding to liberate the valuable tungsten particles. Conventional processing methods rely on stationary crushers and conveyors, which are costly to install, lack mobility, and may not optimize energy consumption. Additionally, mining operations in rugged or remote locations face logistical hurdles, making transportation of ore to fixed plants economically unviable.
Why Mobile Cone Crushers?
A mobile cone crusher integrates advanced crushing technology with portability, offering a tailored solution for tungsten ore processing. Here’s why it stands out:
- Portability and Rapid Deployment
Mounted on a tracked or wheeled chassis, mobile cone crushers can be transported directly to mining sites, eliminating the need for costly infrastructure. This mobility is particularly advantageous for small-scale or temporary tungsten projects, enabling operators to process ore on-site and reduce transportation costs. - High-Efficiency Crushing
Equipped with robust cone crushers, these units deliver superior reduction ratios and produce uniformly shaped particles. Advanced hydraulic systems allow real-time adjustment of crusher settings to optimize output size—critical for downstream processes like gravity separation or flotation. - Energy and Cost Savings
Modern mobile cone crushers feature energy-efficient motors and smart control systems that minimize power consumption while maximizing throughput. By processing ore closer to the source, fuel and logistics expenses are significantly reduced. - Adaptability to Complex Ore Bodies
Tungsten deposits often vary in hardness and composition. Mobile cone crushers can be paired with screening units to create closed-loop systems, recirculating oversized material for re-crushing. This ensures consistent product quality and minimizes waste. - Environmentally Friendly Operations
Reduced dust emissions, noise suppression technologies, and lower carbon footprints align mobile crushers with increasingly stringent environmental regulations. Their compact design also minimizes land disturbance compared to fixed installations.
Applications in Tungsten Processing Workflows
- Primary or Secondary Crushing: Mobile cone crushers handle both roles, breaking down raw ore into manageable sizes for further grinding.
- Tailings Reprocessing: They enable efficient recovery of tungsten from legacy tailings, supporting sustainable resource utilization.
- Hybrid Systems: Integrated with mobile screens or jigging machines, these units facilitate turnkey solutions for end-to-end processing.
Case for Adoption
A mining company in Central Asia recently deployed a mobile cone crusher for a tungsten project in a mountainous region. By eliminating the need to transport ore to a distant fixed plant, the operation reduced costs by 30% and achieved a 20% increase in processing efficiency. The crusher’s ability to adjust settings on-the-fly also improved recovery rates during fluctuations in ore hardness.
The Future of Tungsten Processing
As demand for tungsten grows in high-tech industries, mobile cone crushers are poised to play a pivotal role in streamlining supply chains. Innovations such as hybrid power systems, AI-driven optimization, and IoT-enabled remote monitoring will further enhance their performance and sustainability.
Conclusion
The mobile cone crusher represents a paradigm shift in tungsten ore processing, combining cutting-edge technology with operational agility. For mining companies seeking to boost productivity, cut costs, and reduce environmental impact, this versatile machinery is no longer an option—it’s a necessity. By embracing mobile solutions, the tungsten industry can ensure efficient resource extraction while meeting the challenges of the 21st century.