Rock Crusher for Zinc Mineral Processing
Zinc is a vital industrial metal used in various applications, including galvanizing, alloy production, and battery manufacturing. To extract zinc from its ores, efficient mineral processing is essential, and rock crusher play a critical role in this process. This article explores the importance of rock crusher in zinc mineral processing, the types of crusher used, and their operational benefits.
The Role of Rock Crusher in Zinc Mineral Processing
Zinc ores, such as sphalerite (zinc sulfide), are typically found in association with other minerals like lead, copper, and iron. Before zinc can be extracted, the ore must be crushed and ground to liberate the valuable minerals from the waste rock. Rock crusher is the first step in this comminution process, reducing large chunks of ore into smaller, manageable pieces.
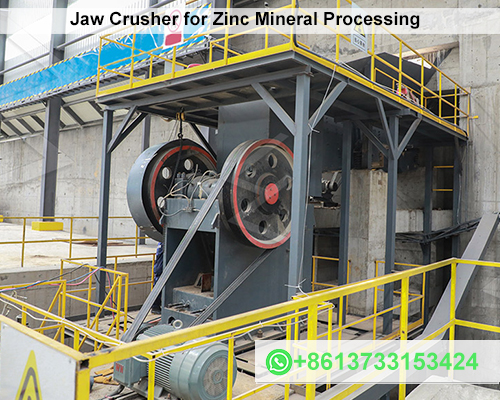
The primary goal of crushing is to achieve a particle size suitable for further processing, such as grinding and flotation. Efficient crushing ensures optimal recovery of zinc and minimizes energy consumption in downstream processes.
Types of Rock Crusher Used in Zinc Processing
- Jaw Crusher:
Jaw crusher is commonly used in the primary crushing stage. They utilize a fixed plate and a moving plate to compress and break down large ore pieces. Their robust design makes them ideal for handling hard and abrasive zinc ores. - Cone Crusher:
Cone crusher is often employed in secondary and tertiary crushing stages. They operate by squeezing the ore between a rotating mantle and a concave liner. Cone crusher is known for their efficiency and ability to produce a uniform particle size, which is crucial for subsequent grinding. - Impact Crusher:
Impact crusher use high-speed impact forces to break down ore. They are suitable for softer ores and can produce a more cubical product, which is advantageous for certain processing methods. - Gyratory Crusher:
Gyratory crusher is similar to jaw crusher but are designed for higher capacity operations. They are often used in large-scale mining operations where high throughput is required.
Benefits of Using Rock Crusher in Zinc Processing
- Increased Efficiency:
By reducing the size of the ore, crusher enable more efficient grinding and separation processes, leading to higher zinc recovery rates. - Cost Savings:
Properly sized ore reduces energy consumption in grinding mills, lowering operational costs. - Flexibility:
Modern rock crusher is designed to handle a wide range of ore types and sizes, making them adaptable to different mining conditions. - Durability:
High-quality crusher is built to withstand the harsh conditions of mining operations, ensuring long-term reliability and minimal downtime.
Challenges and Considerations
While rock crusher is essential for zinc processing, there are challenges to consider. Abrasive ores can cause wear and tear on crusher components, necessitating regular maintenance. Additionally, the choice of crusher type and configuration must align with the specific characteristics of the ore and the processing plant’s requirements.
Conclusion
Rock crusher is indispensable in the zinc mineral processing chain, enabling the efficient extraction of zinc from its ores. By selecting the right type of crusher and optimizing its operation, mining companies can enhance productivity, reduce costs, and maximize zinc recovery. As technology advances, rock crusher will continue to evolve, offering even greater efficiency and sustainability in mineral processing.
In summary, the integration of rock crusher into zinc processing operations is a cornerstone of modern mining, ensuring that this essential metal can be extracted and utilized to meet global demand.