Stone Crusher Machine for Mineral Zinc
The extraction and processing of zinc ore require specialized equipment to reduce large chunks of ore into manageable sizes for further processing. One of the most important pieces of machinery used in this process is the stone crusher. Stone crushers play a critical role in breaking down zinc ore, making it easier to extract the zinc and separate it from other materials. In this article, we will explore the importance of stone crusher machines in zinc mining, the types of crushers used, and the key considerations when selecting a crusher for mineral zinc processing.
1. The Role of Stone Crushers in Zinc Mining
Zinc is a highly valuable metal, commonly used in construction, electronics, and as an essential part of various alloys. It is mainly extracted from zinc ores like sphalerite (ZnS) through a complex process of crushing, grinding, and smelting. Before the ore can be processed to extract zinc, it needs to be crushed to a manageable size that allows the zinc-bearing minerals to be efficiently separated from the gangue (non-valuable materials).
This is where stone crushers come in. A stone crusher machine helps to break down large rocks and ores into smaller fragments, which is a critical first step in ore processing. The crusher reduces the size of the zinc ore and makes it suitable for further stages like grinding, flotation, or leaching, depending on the processing method.
2. Types of Stone Crushers Used for Mineral Zinc
There are various types of stone crushers available, each designed to handle different tasks and ore materials. Below are the main types of crushers used in the mining and processing of zinc ores:
2.1. Jaw Crusher
The jaw crusher is one of the most common types of crushers used for crushing zinc ores in the mining industry. It works by using two jaws, one fixed and one movable, that crush the material by applying compressive force. Jaw crushers are typically used for the initial reduction of large zinc ore blocks into smaller pieces.
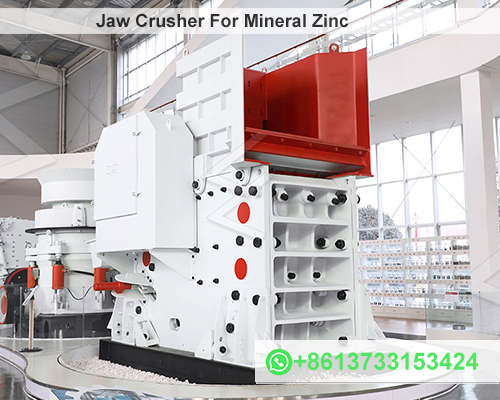
Advantages:
- High efficiency in reducing large, hard ores.
- Durability and reliability, especially for handling tough ore materials.
- Easy to maintain and repair, making it ideal for mining operations.
Limitations:
- Typically produces larger output particles, which may require secondary processing.
2.2. Cone Crusher
The cone crusher is typically used for secondary and tertiary crushing stages. After the jaw crusher has reduced the ore to a manageable size, the cone crusher is used to further reduce the material and produce smaller, more uniform sizes. The cone crusher is especially suitable for harder ores, like zinc-bearing sphalerite, as it is designed to crush through compression and shear forces.
Advantages:
- High crushing capacity and fine output size, making it ideal for high-volume operations.
- Efficient energy consumption due to advanced crushing technology.
- Can handle a wide range of ore materials, including very hard ores like zinc ore.
Limitations:
- Requires more maintenance compared to jaw crushers, especially in high-demand environments.
2.3. Impact Crusher
An impact crusher works by using impact force to break down the material. The ore is thrown against a series of plates that crush it into smaller pieces. Impact crushers are often used in the secondary or tertiary stages of crushing zinc ores to create a finer output.
Advantages:
- Produces fine and uniform product size.
- Efficient energy usage for medium to soft ores.
- Lower operational costs for certain materials.
Limitations:
- May not be as efficient for hard ores like zinc ore, which require more forceful crushing.
2.4. Hammer Crusher
A hammer crusher is another machine used in mineral processing that relies on high-speed rotors and hammers to crush ores. This type of crusher is commonly used for soft to medium-hard zinc ores, and it can produce a fine crushed product suitable for grinding or further processing.
Advantages:
- Simple design and low cost.
- Ideal for softer ores, breaking down materials with ease.
- High reduction ratio and high throughput capacity.
Limitations:
- Limited efficiency with harder ores like zinc, requiring more power.
2.5. Roll Crusher
The roll crusher is a compression-type crusher that uses two cylindrical rollers to crush materials by forcing them between the rolls. This machine is commonly used in secondary or tertiary crushing stages to produce uniform particle sizes.
Advantages:
- Produces consistent particle sizes.
- Low operational costs.
- Suitable for both hard and soft ores, including zinc.
Limitations:
- May require additional crushing stages to achieve smaller sizes.
3. Key Considerations When Selecting a Stone Crusher for Zinc Ore Processing
When selecting a stone crusher machine for mineral zinc, there are several factors that need to be considered to ensure optimal performance and cost-effectiveness:
3.1. Hardness and Size of Ore
Zinc ores can vary in hardness, with some ores being harder than others. For harder ores, like sphalerite, a jaw crusher or cone crusher may be required for initial and secondary crushing. If the ore is softer, a hammer or impact crusher may be sufficient. The crusher’s ability to handle hard ores without excessive wear is an important factor in determining the right machine.
3.2. Output Size Requirements
The required output size of the crushed material is another important consideration. If a finer product is required, crushers like cone crushers or impact crushers may be necessary for further reduction. A primary crusher like a jaw crusher is ideal for reducing ore to a coarse size, but for more precise size requirements, additional stages of crushing might be needed.
3.3. Capacity and Throughput
The crusher’s capacity to handle the volume of ore your operation requires is critical. Different crushers have different throughput capacities, ranging from small-scale crushers that handle a few tons per hour to large-scale industrial crushers that can process hundreds of tons per hour. Ensuring that the selected crusher matches your mining operation’s scale will help avoid bottlenecks and optimize production.
3.4. Energy Efficiency
Energy consumption is a significant operating cost in any mining operation. It is essential to select a crusher that offers a good balance between throughput and energy efficiency. Crushers like cone crushers tend to offer better energy efficiency than some other types, like impact crushers or hammer crushers, when dealing with harder ores.
3.5. Maintenance and Durability
The longevity and ease of maintenance of the crusher are also essential factors to consider. Crushers that require frequent repairs can result in costly downtime. Therefore, it is important to choose a machine from a reputable manufacturer with a strong support network for spare parts and service. Additionally, machines made from durable materials tend to have a longer lifespan, reducing long-term costs.
4. Conclusion
Stone crushers are a critical component of the zinc ore processing chain. They help reduce large chunks of zinc ore into smaller, more manageable pieces for further processing, whether through grinding, flotation, or leaching. Depending on the hardness and characteristics of the zinc ore, different types of crushers—such as jaw crushers, cone crushers, impact crushers, hammer crushers, and roll crushers—can be used in combination to achieve the desired output size.
When selecting a stone crusher for zinc ore processing, it is important to consider factors like the hardness of the ore, required output size, capacity, energy efficiency, and maintenance needs. With the right crusher, mining operations can improve the efficiency of their processing lines, ensuring that zinc is extracted in a cost-effective and environmentally responsible manner.