Crusher for Processing Concrete
In the world of construction and demolition, concrete is one of the most widely used materials. However, once concrete structures or pavements are torn down or replaced, the leftover concrete needs to be processed for reuse or disposal. This is where crusher designed specifically for processing concrete come into play. These machines help break down the bulky material into smaller, more manageable pieces, enabling it to be recycled and reused in various construction applications.
What is a Concrete Crusher?
A concrete crusher is a machine that is specifically engineered to crush, grind, and process concrete debris from demolished buildings, roads, and other structures. The primary purpose of these crusher is to reduce the size of concrete materials, turning them into smaller pieces known as recycled aggregate. This processed material can be reused in new construction projects, helping to reduce the environmental impact of producing new concrete.
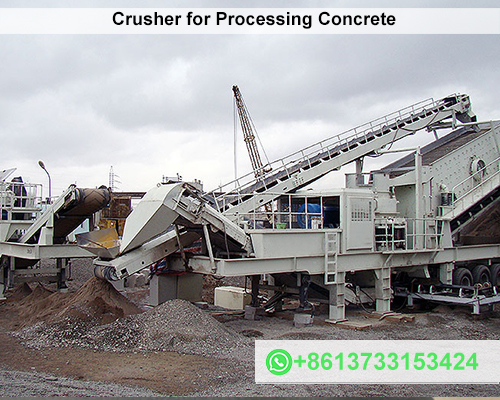
Types of Crusher for Concrete Processing
Several types of crusher is used for processing concrete, each offering different features and benefits depending on the size, scope, and nature of the job.
1. Jaw Crusher
Jaw crusher is the most common type of crusher used for processing concrete. They are known for their ability to handle large, bulky materials. These crusher have two powerful jaws that crush concrete by compressing the material between them. The material is fed into the crusher’s inlet, where it is subjected to a compressive force that breaks it down into smaller pieces.
Advantages:
- Capable of handling large, rough pieces of concrete.
- Simple design, making them easy to maintain.
- Ideal for primary crushing in large-scale demolition projects.
Disadvantages:
- Can be less efficient for finer material sizes.
- Requires more energy for crushing very hard or reinforced concrete.
2. Impact Crusher
Impact crusher, also known as impact breakers, work by using impact rather than compression to break down materials. These crusher have a rotating impeller or hammer that strikes the concrete, shattering it into smaller pieces. Impact crusher is particularly effective at breaking up concrete with steel reinforcement (rebar).
Advantages:
- High production rates for smaller aggregate sizes.
- Efficient at handling reinforced concrete due to the impact force.
- Less wear and tear compared to jaw crusher when handling concrete with rebar.
Disadvantages:
- Produce more dust and fine materials.
- Less effective for larger pieces of concrete.
3. Cone Crusher
Cone crusher is similar to jaw crusher but are typically used for secondary or tertiary crushing. These crusher use a rotating cone-shaped mantle to crush concrete against a concave surface. They are known for producing finely crushed materials and are particularly useful for shaping the material into uniform sizes.
Advantages:
- Produce a more uniform product.
- Can handle a variety of materials, including concrete with rebar.
- Great for secondary crushing after jaw crusher.
Disadvantages:
- Generally slower than impact crusher.
- May require additional equipment for feeding large, bulky concrete pieces.
4. Roll Crusher
Roll crusher use two heavy rolls to crush concrete, typically at lower speeds. The material is crushed by being pressed between the rolls, which rotate in opposite directions. Roll crusher is often used for crushing concrete into smaller aggregate sizes, especially in situations where a finer product is desired.
Advantages:
- Lower operating costs.
- Produce a uniform and consistent product.
- Great for processing softer concrete without much reinforcement.
Disadvantages:
- Not ideal for very hard or reinforced concrete.
- Slower compared to other crusher types.
5. Mobile Crusher
Mobile crusher, as the name suggests, are crusher mounted on tracks or wheels, making them highly portable. These crusher combine various types of crushing mechanisms (usually jaw, cone, or impact crusher) into a single unit that can be easily moved from one job site to another.
Advantages:
- Highly versatile and portable, allowing them to be used in various locations.
- Can process concrete directly on-site, reducing transport costs.
- Flexible and efficient for both large and small-scale projects.
Disadvantages:
- Can be more expensive to rent or purchase than stationary crusher.
- May have lower throughput compared to stationary crusher in high-demand applications.
The Process of Concrete Crushing
The concrete crushing process can vary depending on the type of crusher used, but generally follows these steps:
- Loading the Concrete: Concrete debris is loaded into the hopper or feed chute of the crusher. This can be done manually or using heavy machinery such as excavators or front-end loaders.
- Crushing: Once the material is in the crusher, it is processed by the crusher mechanism (impact, compression, or shearing force), which breaks down the concrete into smaller, more manageable pieces.
- Screening and Sorting: After crushing, the material is often screened to separate different sizes of aggregates. Larger pieces are sent back through the crusher, while smaller pieces are stockpiled for reuse.
- Storage or Transport: Once the concrete is processed into the desired size, it can be transported for reuse in construction projects, typically as aggregate for road bases, new concrete mixes, or even as backfill material.
Benefits of Using a Concrete Crusher
Using a concrete crusher for processing concrete offers several advantages, particularly in terms of sustainability, cost-efficiency, and convenience:
- Recycling: The main benefit of using a concrete crusher is the ability to recycle concrete. The crushed material can be reused as aggregate, reducing the need for virgin materials and helping to conserve natural resources.
- Cost Savings: Processing concrete on-site can save on transportation costs, as the material doesn’t need to be hauled to a landfill or processing facility. Additionally, the recycled aggregate can be reused in new projects, reducing the need to purchase new materials.
- Environmental Benefits: Crushing concrete reduces the need for new raw materials, which in turn reduces the environmental impact of mining, transportation, and processing. It also reduces the amount of concrete waste sent to landfills, contributing to waste reduction efforts.
- Efficient Operations: Modern concrete crusher is designed for high efficiency, allowing contractors to process large amounts of concrete in a relatively short amount of time, ensuring that projects stay on schedule.
Conclusion
Concrete crusher is indispensable tools for the construction and demolition industries. They help reduce waste, lower construction costs, and promote the recycling of materials, making them a key element of sustainable construction practices. Whether you’re dealing with large-scale demolition or small-scale construction, understanding the types of crusher and their benefits can ensure that concrete processing is done efficiently and cost-effectively. By incorporating the right crusher for your project, you can contribute to a greener, more sustainable building environment while saving money and resources.