Crusher Plant Working Mechanism and Performance Analysis
Stone crushing machines play a crucial role in various industries, such as mining, construction, and road building, by breaking down large rocks into smaller, more manageable sizes. Understanding the working principles and analyzing the performance of these machines is essential for efficient operation and optimization. In this article, we will delve into the working principles and perform a performance analysis of stone crushing machines.
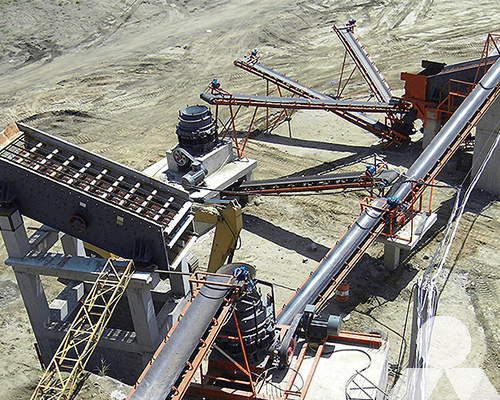
Working Principle
Stone crushing machines, often referred to as stone crushers or rock crushers, are mechanical devices designed to break down large rocks into smaller pieces. The working principle of these machines can be summarized in the following steps:
- Feeding: Large rocks are fed into the crusher’s hopper through a vibrating feeder or conveyor belt.
- Crushing: Inside the machine, there is a chamber with a rotating rotor or hammer bars that strike the incoming rocks. The impact and compression forces generated by the rotor break the rocks into smaller pieces. Some crushers also use a compressive force between a fixed and a movable jaw to achieve the desired size reduction.
- Discharge: The crushed material is discharged through an adjustable gap between the rotor and the surrounding casing or between the jaws, depending on the type of crusher.
- Screening: In some cases, the crushed material may pass through a screen to sort it into different sizes before final discharge.
Performance Analysis
The performance of stone crushing machines can be analyzed based on several key parameters:
- Capacity: Capacity refers to the maximum amount of material that a crusher can process per unit of time. It is typically measured in tons per hour (TPH). Higher capacity machines can handle larger volumes of material, improving productivity.
- Efficiency: Efficiency is a measure of how effectively a crusher converts input energy into output material. A more efficient machine consumes less power while producing the same amount of crushed material, leading to cost savings.
- Size Reduction Ratio: The size reduction ratio is the ratio of the initial feed size to the final product size. It determines how finely the machine can crush rocks. Higher reduction ratios result in finer crushed material.
- Wear and Maintenance: Stone crushing machines are subjected to wear and tear due to the abrasive nature of the materials they process. Analyzing the wear patterns and maintenance requirements helps in optimizing the machine’s lifespan and reducing downtime.
- Particle Size Distribution: Understanding the particle size distribution of the crushed material is crucial for quality control and meeting specific product requirements. Various crushers produce different size distributions.
- Energy Consumption: Energy consumption is a significant factor in the operational cost of stone crushing machines. Analyzing and optimizing energy efficiency can lead to substantial savings.
Stone crushing machines are indispensable in many industries, and their proper understanding and performance analysis are crucial for efficient operation and productivity. By comprehending the working principles and assessing key performance parameters, operators and engineers can optimize these machines, ensuring they meet production requirements while minimizing operational costs.