Simple Design of a Rock Crushing Plant
Rock crushing plants are used widely in the mining, quarrying, and construction industries to process large rocks into smaller, more manageable pieces for various applications. Although there are numerous design considerations when building these plants, a simplified design can yield an efficient and low-cost operation, especially for smaller or temporary projects. This article will explore the basic components and layout of a rock crushing plant and guide you through the design of a simple yet functional system.
1. Understanding the Purpose of Rock Crushing
The primary function of a rock crushing plant is to reduce large rocks into smaller particles, such as gravel, sand, or even dust. This makes it easier to transport, process, and utilize in various applications. Commonly crushed materials include granite, basalt, limestone, and sandstone. A well-designed crushing plant can meet the demands of construction projects, road building, and aggregate production.
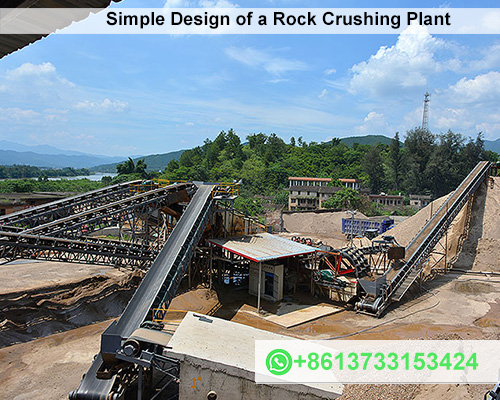
2. Essential Components of a Rock Crushing Plant
A basic rock crushing plant design will include the following components:
- Primary Crusher: Reduces large rocks to manageable sizes.
- Secondary Crusher: Further reduces the rock to the desired size.
- Conveyor Belts: Move material between crushing stages and to storage.
- Screening Equipment: Separates crushed material by size.
- Storage Hopper: Holds the final product before transport.
Each of these components plays a crucial role in ensuring a continuous flow of material through the system and achieving desired product sizes.
3. Step-by-Step Design Guide for a Simple Crushing Plant
Step 1: Select a Primary Crusher
The primary crusher is the first stage in the process and is responsible for the initial size reduction of the rock. Common options include:
- Jaw Crusher: Ideal for large rocks; simple in design, reliable, and can handle high compressive strength materials.
- Gyratory Crusher: Good for high-capacity applications; more complex and costly but provide a higher throughput.
For a simple, low-cost design, a jaw crusher is often preferred, especially for smaller operations.
Step 2: Choose a Secondary Crusher
The secondary crusher further processes material after the primary crusher. Depending on the product size requirements, several types of crusher can be used:
- Cone Crusher: Suitable for high-hardness materials and provide consistent particle size.
- Impact Crusher: Ideal for materials that are less abrasive and require finer crushing, such as limestone.
A cone or impact crusher is often chosen for this stage, depending on the material’s hardness and desired output.
Step 3: Design the Material Handling System
Efficient material handling is critical to keep the process moving without bottlenecks. Key elements include:
- Conveyor Belts: Connect the crusher and move material throughout the plant. For a basic setup, you need conveyors leading from the primary crusher to the secondary crusher, and from the secondary crusher to the screening system.
- Storage Hopper or Surge Pile: Holds the processed material temporarily, reducing the need for constant loading and unloading. This setup can help prevent stoppages and ensure continuous crushing.
Step 4: Set Up Screening Equipment
Screening separates the material into different sizes for various uses. A simple setup might include:
- Vibrating Screens: Effective for classifying and separating material. Multiple screens can provide gradation for different output sizes, such as coarse gravel, sand, or fine particles.
Screens should be placed after the secondary crusher and before the storage hopper to separate materials before final storage.
4. Energy and Environmental Considerations
While simplicity is key in this design, energy efficiency and environmental impact should not be ignored. Consider using electric-powered equipment, where possible, to reduce fuel costs and emissions. Dust suppression systems (like water sprays) are also vital to comply with environmental regulations and maintain air quality in the work area.
5. Layout and Workflow Optimization
- Linear Layout: For a simple setup, placing all components in a straight line minimizes space usage and simplifies conveyor design.
- Safety and Maintenance Access: Design the plant layout to allow easy access for maintenance and repairs. Placing equipment on elevated platforms can improve access and streamline operations.
Conclusion
A simple rock crushing plant design includes a primary and secondary crusher, conveyor belts, screening equipment, and a storage hopper, arranged in a streamlined and efficient configuration. By carefully selecting each component based on material requirements, desired output, and budget, this layout achieves reliable performance with minimal operational costs. Whether you’re setting up a plant for a small quarry or as a temporary solution, this design can provide the basis for a cost-effective and efficient rock crushing operation.