Stage Process of Basalt Aggregate Crusher
Basalt, a dense and durable volcanic rock, is widely used in construction as a high-quality aggregate material for concrete, road base, and railway ballast. To transform raw basalt into usable aggregate, a multi-stage crushing process is essential. This article outlines the key stages involved in processing basalt through a crusher system, ensuring optimal particle size, shape, and quality.
1. Primary Crushing (Coarse Crushing)
The first stage begins with the extraction of raw basalt from quarries. Large basalt boulders, often measuring up to 1 meter in diameter, are fed into a primary jaw crusher. This crusher uses compressive force to break down the rock into smaller, manageable pieces (typically 150–300 mm). The jaw crusher’s rugged design and high crushing ratio make it ideal for handling the hardness and abrasiveness of basalt.
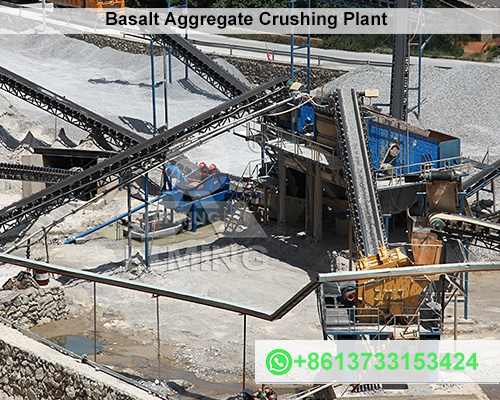
Key considerations:
- Adjusting the crusher’s discharge setting to control output size.
- Pre-screening to remove fine materials or debris before crushing.
2. Secondary Crushing (Intermediate Reduction)
The output from the primary crusher is conveyed to a secondary cone crusher or impact crusher. Secondary crushing further reduces the basalt fragments to sizes between 20–70 mm. Cone crushers are preferred for their ability to produce uniformly shaped particles, while impact crushers enhance cubicity (cube-shaped grains), which is critical for high-strength concrete applications.
Key considerations:
- Optimizing the crusher’s closed-side setting (CSS) for consistent output.
- Monitoring wear parts (e.g., mantles, concaves) due to basalt’s abrasive nature.
3. Screening and Classification
After secondary crushing, the material undergoes vibrating screening to separate particles by size. Oversized fragments are redirected back to the secondary crusher, while correctly sized aggregates proceed to the next stage. Screening ensures the final product meets specific gradation requirements (e.g., 10–20 mm, 20–40 mm).
Key considerations:
- Selecting screen mesh sizes based on project specifications.
- Using multi-deck screens to improve efficiency.
4. Tertiary Crushing and Shaping (Optional)
For applications demanding superior particle shape (e.g., asphalt or high-grade concrete), a tertiary vertical shaft impact (VSI) crusher may be employed. This stage uses a high-speed rotor to fracture basalt particles, producing well-shaped, angular aggregates with minimal flakiness.
Key considerations:
- Balancing rotor speed and feed rate to avoid over-crushing.
- Regular maintenance of anvils or rock shelves in the VSI.
5. Washing and Final Screening
To remove dust, clay, or impurities, aggregates may pass through a log washer or screw classifier. Clean basalt aggregates are then re-screened to ensure compliance with industry standards (e.g., ASTM or EN).
Key considerations:
- Recycling water in closed-loop systems to minimize waste.
- Drying aggregates if moisture-sensitive applications are required.
6. Storage and Dispatch
The final product is stockpiled in segregated bins based on size gradation. Automated conveyor systems or loaders transport the aggregates to trucks or railcars for delivery to construction sites.
Quality Control Measures
- Particle shape analysis: Ensuring cubical grains for better compaction.
- Abrasion resistance testing: Confirming durability using the Los Angeles abrasion test.
- Dust suppression: Installing spray systems to reduce airborne particles.
Conclusion
The stage process of a basalt aggregate crusher combines robust machinery, precise screening, and quality checks to transform raw rock into versatile construction materials. By optimizing each stage—from primary crushing to final screening—producers achieve high yields, reduced waste, and aggregates that meet the rigorous demands of modern infrastructure projects. Advances in automation and wear-resistant crusher components continue to enhance the efficiency of basalt processing lines worldwide.