How Much Can a Crushing Aggregate Plant Cost?
A crushing aggregate plant is a vital piece of equipment in the construction and mining industries, used for breaking down large rocks into smaller, more manageable sizes. The cost of setting up and operating a crushing aggregate plant can vary greatly depending on several factors, including the type of plant, its capacity, location, and operational features. In this article, we’ll explore the key cost components involved in setting up and running a crushing aggregate plant.
1. Initial Capital Investment
The initial cost of a crushing aggregate plant includes several major components, such as the crusher itself, screening equipment, conveyors, and other supporting machinery. The total capital investment will depend on the plant’s design and scale.
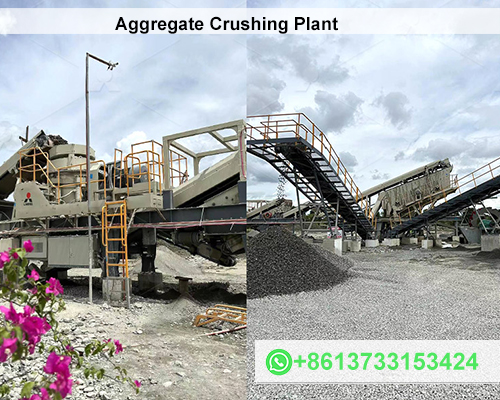
a. Crusher Type
Crushers come in various types, each with its price range:
- Jaw crushers: Commonly used for primary crushing, jaw crushers can cost anywhere from $50,000 to $150,000 or more depending on the size and brand.
- Cone crushers: Often used for secondary or tertiary crushing, these machines can cost between $100,000 to $500,000, depending on their size and capacity.
- Impact crushers: These are typically used for soft to medium-hard materials and can range in price from $100,000 to $300,000.
- Vertical shaft impact crushers (VSI): Used for finer materials and shaping aggregate, VSI crushers can range from $50,000 to $200,000.
b. Screening and Sorting Equipment
Screening systems separate materials by size and are crucial for ensuring the aggregate meets required specifications. Basic screening systems can cost between $20,000 and $100,000. More complex systems with multiple deck screens, washing units, and sorting technology can push the price up to $500,000 or more.
c. Conveyors and Material Handling
Conveyors are essential for moving materials between crushers, screens, and storage areas. Conveyor systems can vary in price, with basic systems costing $20,000–$100,000 and more complex configurations running upwards of $500,000, depending on length, capacity, and automation.
2. Installation Costs
The installation of a crushing aggregate plant involves site preparation, electrical work, foundation laying, and the actual setup of the machinery. Installation costs can range from 10% to 30% of the total equipment cost. For a large-scale plant, installation could cost anywhere from $100,000 to $500,000 or more.
3. Operational Costs
Once the plant is set up, there are ongoing operational costs to consider, including:
a. Labor Costs
The number of workers required to run a crushing aggregate plant can vary, but typically, a medium-sized plant will need operators for crushers, screeners, and material handlers. Labor costs can range from $50,000 to $200,000 annually, depending on the plant size and local wage rates.
b. Fuel and Energy Costs
Crushing plants are energy-intensive, especially when dealing with hard rock. Diesel fuel, electricity, and sometimes natural gas are the primary sources of energy for crushers and other equipment. Fuel and energy costs can range from $200,000 to $1,000,000 per year for a large operation, depending on production levels.
c. Maintenance and Repair
Maintenance costs will vary depending on the plant’s equipment and usage. Regular wear and tear on crushers, screens, and conveyors will require parts replacement and servicing. Annual maintenance can cost between $50,000 and $200,000, though more complex plants or those with heavy use may incur higher costs.
d. Water and Dust Control
Many crushing plants incorporate dust suppression systems and may require water for washing aggregate. These systems can add an additional operational cost, ranging from $10,000 to $100,000 annually, depending on local regulations and plant size.
4. Additional Costs
Other considerations include:
- Environmental Compliance: Environmental regulations may require investments in dust control, noise reduction, and water treatment systems. Compliance costs can range from $50,000 to several hundred thousand dollars, depending on local laws.
- Transportation and Shipping: Transporting raw materials to the plant and finished products to customers involves logistical costs, which can be significant, depending on distance and transportation method.
- Permitting and Licensing: Depending on the region, obtaining necessary permits and licenses for mining, crushing, and processing operations can be costly, ranging from a few thousand dollars to hundreds of thousands for complex projects.
5. Total Cost Estimates
- Small-Scale Plants: A smaller, lower-capacity plant with a single crusher, limited screening, and conveyors could cost between $500,000 to $1.5 million for initial setup, with annual operational costs of $100,000 to $300,000.
- Medium-Scale Plants: A more advanced medium-scale operation with multiple crushers, screening systems, and conveyors could cost between $2 million to $5 million in setup, with ongoing annual costs of $500,000 to $1 million.
- Large-Scale Plants: For large-scale operations with high-capacity crushers, multiple screening units, and sophisticated material handling systems, initial capital costs can range from $5 million to $20 million, with annual operational costs of $1 million to $5 million.
Conclusion
The cost of a crushing aggregate plant depends on many factors, including the type of equipment, plant capacity, location, and the specific needs of the operation. From initial setup costs to ongoing operational expenses, understanding the key factors that influence plant cost is crucial for making informed investment decisions. Whether for a small-scale operation or a large, high-capacity plant, proper planning and cost estimation will help ensure the long-term success and profitability of the aggregate crushing business.