Process Analysis Of Basalt Crushing Line
Basalt is a common igneous rock that is used as an aggregate in construction materials. Basalt crushing lines are used to reduce the size of basalt rocks to the desired size for use in various applications. The basalt crushing process typically involves several stages, including:
- Primary crushing: This is the first stage of crushing, and it is typically done using a jaw crusher or a gyratory crusher. The purpose of primary crushing is to reduce the size of the basalt rocks to a size that can be handled by the secondary crushing equipment.
- Secondary crushing: This stage of crushing is typically done using a cone crusher or a hammer mill. The purpose of secondary crushing is to further reduce the size of the basalt rocks to the desired size for use in the application.
- Tertiary crushing: This stage of crushing is optional, and it is typically only used if a very fine product is required. Tertiary crushing is typically done using a vertical roller mill or a ball mill.
- Screening: Screening is used to separate the crushed basalt rocks into different size fractions. This is typically done using a series of vibrating screens.
- Washing: Washing is used to remove dust and other impurities from the crushed basalt rocks. This is typically done using a spray washer or a log washer.
- Stockpiling: The crushed and washed basalt rocks are typically stockpiled in separate piles for different size fractions. This allows for easy access to the material for use in various applications.
The specific equipment and process used in a basalt crushing line will vary depending on the desired product size, the capacity of the plant, and the characteristics of the basalt rock.
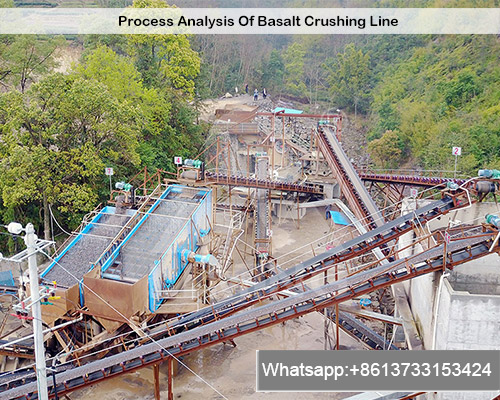
Here are some of the factors that can affect the efficiency of a basalt crushing line:
- The type of crushing equipment: Different types of crushing equipment have different efficiencies. For example, jaw crusher are typically less efficient than cone crusher.
- The feed size of the basalt rocks: The larger the feed size of the basalt rocks, the more energy will be required to crush them.
- The moisture content of the basalt rocks: Basalt rocks that are wet will require more energy to crush than basalt rocks that are dry.
- The presence of impurities in the basalt rocks: Impurities such as clay and silt can reduce the efficiency of the crushing process.
By carefully considering these factors, it is possible to design and operate a basalt crushing line that is efficient and productive.
Additional considerations
In addition to the factors discussed above, there are a number of other considerations that should be taken into account when designing and operating a basalt crushing line. These include:
- The environmental impact of the crushing process: Basalt crushing can generate dust and noise pollution. It is important to take steps to mitigate these impacts.
- The safety of the workers: The basalt crushing process can be dangerous. It is important to have proper safety procedures in place and to train workers on how to use the equipment safely.
- The cost of the crushing process: The cost of operating a basalt crushing line can be significant. It is important to design and operate the line in a way that minimizes costs.
By carefully considering all of these factors, it is possible to design and operate a basalt crushing line that is efficient, productive, environmentally friendly, safe, and cost-effective.