Daily processing 300 tons of copper ore beneficiation equipment
Copper, a versatile and essential metal in various industries, is primarily extracted from copper ore through a series of beneficiation processes. The demand for copper continues to rise, making it crucial for mining operations to employ efficient and advanced equipment for ore processing. This article discusses the essential equipment required for processing 300 tons of copper ore per day.
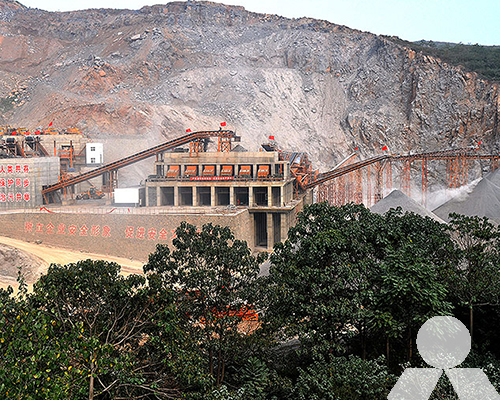
Crushing and Grinding
- Jaw Crusher: The process begins with the crushing of raw copper ore. A robust jaw crusher reduces the ore into smaller, manageable pieces, ensuring uniform particle size for downstream processing.
- Cone Crusher: To further refine the crushed ore, a cone crusher is employed. It achieves finer particle size reduction, enhancing the overall efficiency of the milling process.
- Ball Mill: The ground ore is then fed into a ball mill, where it is further pulverized into a fine powder. This step is critical for liberating valuable copper minerals from the gangue material.
Mineral Separation
- Flotation Cells: Flotation is a widely-used technique for separating copper minerals from other non-valuable minerals. Flotation cells, equipped with reagents, create a froth that selectively captures and separates copper minerals.
- Thickeners and Filters: To separate the copper concentrate from water and gangue, thickeners and filters are employed. The concentrate is collected, while water and tailings are disposed of.
Concentration and Smelting
- Smelting Furnaces: The copper concentrate is then subjected to high-temperature smelting in furnaces. This process melts the copper concentrate, separating the copper metal from impurities.
- Refining: After smelting, the molten copper undergoes refining processes to remove any remaining impurities, ensuring the highest purity possible.
Quality Control and Environmental Management
- Analytical Equipment: To maintain the quality of the final product, analytical equipment is used to monitor copper content and impurities throughout the processing stages.
- Dust and Emissions Control: To comply with environmental regulations, dust collectors and emissions control systems are integrated into the facility to minimize environmental impact.
Automation and Efficiency
- Conveyor Systems: Efficient conveyor systems ensure the smooth flow of materials throughout the processing plant, reducing manual handling and increasing operational efficiency.
- Automation and Control Systems: Modern ore processing facilities utilize advanced automation and control systems to monitor and optimize various processes, enhancing overall efficiency and safety.
Processing 300 tons of copper ore per day requires a well-designed and integrated system of equipment and processes. The selection and utilization of the right equipment are essential for achieving high efficiency, quality, and environmental compliance in copper ore processing. With advancements in technology and a focus on sustainable practices, the mining industry continues to evolve, ensuring a steady supply of this vital metal for various applications worldwide.