Cement manufacturing process by vertical roller mill
The cement industry plays a vital role in global construction, providing the essential building material for infrastructure development. To meet the growing demand for cement, manufacturers continuously seek innovative and efficient production processes. One such advancement is the use of Vertical Roller Mills (VRMs) in cement production. This article will explore the key aspects of the VRM technology and its role in the cement manufacturing process.
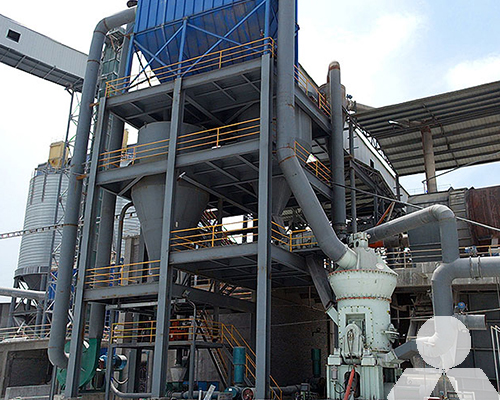
Vertical Roller Mill (VRM):
A Vertical Roller Mill, often referred to as a VRM, is a cutting-edge grinding equipment used in the cement industry to crush and grind raw materials into fine powder. Unlike traditional ball mills or horizontal roller mills, VRMs utilize a vertical design with rollers that rotate on a central axis, enabling efficient and energy-saving grinding.
Key Components of VRM:
- Grinding Table: The grinding table is a flat, horizontal surface where the raw materials are crushed and ground. It is equipped with rollers that press against the material, facilitating the grinding process.
- Rollers: The rollers are the core components of a VRM, and they exert pressure on the grinding table to crush the raw materials. These rollers can be individually controlled to maintain optimal grinding conditions.
- Separator: VRMs feature an integrated dynamic separator that classifies the crushed material into fine and coarse particles. This separation process ensures that only the fine particles are collected as finished cement.
- Drive System: VRMs are equipped with powerful drive systems that rotate the grinding table and rollers. These systems are designed for high efficiency and precise control of grinding operations.
Cement Production Process Using VRM:
- Raw Material Preparation: In the cement production process, raw materials such as limestone, clay, shale, and iron ore are carefully proportioned and crushed into a homogenous mixture.
- Grinding: The crushed raw materials are fed into the VRM, where they undergo grinding to achieve the desired fineness. The pressure exerted by the rollers on the grinding table creates a fine powder.
- Classification: The ground material is classified by the dynamic separator, separating the fine particles from the coarse ones.
- Clinker Production: The fine material collected from the VRM is heated in a rotary kiln to produce clinker, the intermediate product in cement manufacturing.
- Cement Grinding: After cooling, the clinker is mixed with gypsum and other additives and ground in a separate VRM to produce the final cement product.
Advantages of VRM in Cement Production:
- Energy Efficiency: VRMs are known for their energy-efficient grinding process, reducing energy consumption compared to traditional mills.
- Consistency: VRMs offer precise control over the grinding process, ensuring consistent product quality.
- Flexibility: VRMs can handle a wide range of raw materials and produce various types of cement, making them versatile in cement production.
- Environmental Benefits: Lower energy consumption leads to reduced greenhouse gas emissions, aligning with sustainability goals.
The use of Vertical Roller Mills in cement production has revolutionized the industry by providing a more efficient and environmentally friendly grinding solution. VRMs offer enhanced energy efficiency, product consistency, and flexibility, making them an essential component of modern cement manufacturing. As the industry continues to evolve, VRM technology is poised to play a pivotal role in meeting the increasing demand for cement worldwide while contributing to a greener future.