Design Parameters of Vibrating Screen
Vibrating screens are essential components in industries ranging from mining and construction to pharmaceuticals and food processing. They are primarily used to separate materials by size, shape, or density using vibration as the driving force. The design of a vibrating screen is a complex task requiring careful consideration of several key parameters to ensure efficiency, reliability, and durability. This article outlines the primary design parameters of vibrating screens and their impact on performance.
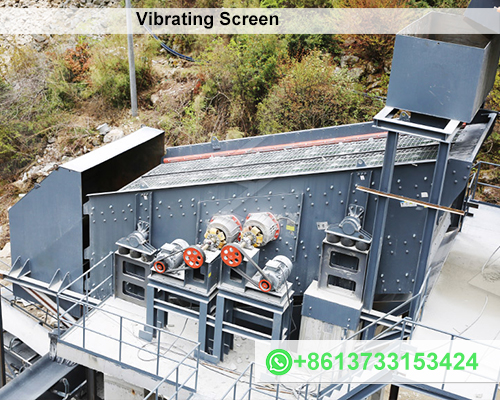
1. Screen Type and Configuration
The type of vibrating screen depends on the application and material properties:
- Linear Vibrating Screens: Generate vibrations along a straight path, ideal for precise classification and dewatering.
- Circular Vibrating Screens: Use rotary motion, often suited for coarse material screening.
- Elliptical Vibrating Screens: Combine the benefits of linear and circular motion, effective for fine screening.
2. Screen Deck
The screen deck is the surface on which materials are separated, and its properties significantly affect performance:
- Material: Common options include woven wire mesh, perforated plates, and polyurethane. The choice depends on wear resistance, efficiency, and application.
- Number of Decks: Single, double, or multi-deck configurations are available, enabling multiple separation stages.
3. Vibratory Motion
The vibratory motion impacts the efficiency of material stratification and separation:
- Amplitude: Defines the vibration displacement. Higher amplitude suits coarse materials, while lower amplitude is suitable for fine particles.
- Frequency: Affects the speed of vibration. Higher frequencies increase separation efficiency for small particles.
- Inclination: The angle of the screen deck influences material flow. Steeper angles improve material movement but may reduce screening efficiency.
4. Capacity and Throughput
The capacity of a vibrating screen is determined by the size and volume of material it can process per unit time:
- Screen Area: A larger area allows for higher throughput but may reduce efficiency if not adequately supported by motion parameters.
- Feed Rate: The rate at which material is fed onto the screen impacts performance. Excessive feed can lead to clogging and inefficiency.
5. Material Characteristics
The physical properties of the material being screened dictate specific design considerations:
- Particle Size Distribution: The range of particle sizes affects the choice of screen mesh and vibration parameters.
- Moisture Content: High moisture can lead to screen clogging; dewatering screens or anti-blinding systems may be required.
- Bulk Density: Heavier materials require more robust designs and higher vibration amplitudes.
6. Drive Mechanism
The drive mechanism generates and transmits vibratory forces to the screen deck:
- Electric Motors: Commonly paired with eccentric weights to produce vibrations.
- Hydraulic Drives: Suitable for heavy-duty applications with adjustable force settings.
- Magnetic Drives: Often used in fine screening applications for precise control.
7. Structural Considerations
The structural integrity of the vibrating screen ensures longevity and safe operation:
- Frame Design: Frames must withstand the dynamic forces generated during operation. Steel or reinforced composites are typical materials.
- Damping Systems: Reduce vibration transfer to the support structure, protecting the screen and surrounding equipment.
- Maintenance Access: Easy access to replace screen media and inspect drive components is essential for minimizing downtime.
8. Power Consumption
Efficient energy usage is critical in modern vibrating screen design:
- Balance of Power: Overpowered systems waste energy, while underpowered systems fail to perform optimally.
- Energy Recovery Systems: Advanced designs may include mechanisms to recapture energy from the vibration process.
Conclusion
The design of a vibrating screen is an intricate balance of multiple parameters, each influencing its efficiency, capacity, and durability. Engineers must consider the material properties, application requirements, and operational conditions to develop a system tailored to specific needs. Advances in simulation and materials science are continually improving the performance and sustainability of vibrating screen designs, ensuring their continued relevance across industries.
By understanding and optimizing these parameters, manufacturers can enhance productivity, reduce operational costs, and achieve superior material separation performance.