Mobile Screens on Tracks Enhancing Efficiency in Mining Operations
In the mining industry, efficiency, flexibility, and mobility are critical to optimizing operations. As mining sites are often located in remote and rugged terrains, mobile equipment has become increasingly essential for facilitating material processing. One of the most innovative and versatile solutions in this regard is the mobile screen on tracks. This powerful equipment has revolutionized the screening process, allowing miners to efficiently separate materials and ensure product quality while adapting to dynamic mining environments. In this article, we will explore the functionality, benefits, and applications of mobile screens on tracks used in mining.
What is a Mobile Screen on Tracks?
A mobile screen on tracks is a portable screening machine mounted on crawler tracks, designed for sorting and processing a wide variety of materials, including ores, rocks, gravel, and minerals. These machines are equipped with screening decks and a system of conveyor belts that can process materials efficiently while being mobile enough to navigate challenging terrains.
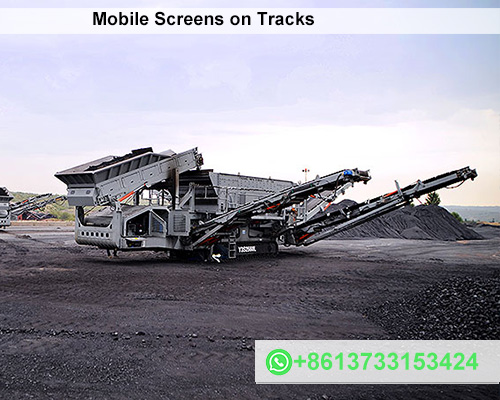
Unlike stationary screens, mobile screens are powered by diesel engines or electric motors, allowing them to be easily moved from one location to another without the need for permanent infrastructure or extensive setup. The crawler tracks give them the ability to traverse uneven ground and adapt to the changing needs of mining sites.
The Design and Features of Mobile Screens on Tracks
Mobile screens on tracks are built for rugged conditions and are capable of handling large volumes of material while maintaining precision and performance. Some of the essential design features include:
a. Heavy-Duty Crawler Tracks
The tracks enable the machine to move seamlessly across rough, uneven surfaces typically found in mining operations. Whether the terrain is rocky, muddy, or sloped, the crawler system ensures the machine can be relocated without difficulty.
b. Multiple Screening Decks
Mobile screens typically come with two or more screening decks that can separate materials into different sizes. The size of these decks can be adjusted based on the specific requirements of the mining operation. Screens are designed to handle everything from fine particles to large rocks.
c. Adjustable Speed and Vibrations
To accommodate different types of materials and to maximize efficiency, mobile screens come with adjustable speed settings and vibration control. This ensures optimal separation of materials, even in harsh or wet conditions often encountered in mining.
d. Efficient Conveyor Systems
Mobile screens are equipped with conveyors that move processed materials to different locations, eliminating the need for additional handling equipment. The conveyors can often be folded or adjusted for easy transport.
e. Remote Operation
Some advanced mobile screens come with remote operation controls, allowing workers to monitor and control the screening process from a distance. This feature increases safety by reducing the need for personnel to be in close proximity to the equipment.
Applications of Mobile Screens on Tracks in Mining
Mobile screens on tracks are versatile machines that can be used in various stages of the mining process, providing enhanced productivity and flexibility. Here are some key applications:
a. Ore and Mineral Processing
In mining operations, one of the primary uses of mobile screens is in the processing of ores and minerals. After the primary and secondary crushing stages, mobile screens are used to separate fine materials from the bulk, allowing miners to extract valuable minerals efficiently. These screens ensure that only the desired size of ore moves on to further processing.
b. Aggregate Screening
For mining operations that produce aggregates like sand, gravel, and crushed stone, mobile screens provide a vital step in ensuring product quality. They help classify the material into various sizes for use in construction, road building, and infrastructure projects.
c. Coal and Energy Mining
In coal mining, mobile screens are used to sort coal into different grades based on size, which is crucial for both the processing and shipping stages. Mobile screens improve efficiency by allowing coal to be screened directly at the mining site, reducing the need for transporting large amounts of unsorted material.
d. On-Site Screening at Open-Pit Mines
In open-pit mining, where large volumes of material need to be processed, mobile screens provide flexibility by moving along with the excavation process. This mobility reduces the time and cost associated with transporting materials to fixed screening locations, increasing overall operational efficiency.
Advantages of Using Mobile Screens on Tracks in Mining
The growing popularity of mobile screens on tracks in mining operations is largely due to the numerous advantages they offer:
a. Mobility and Flexibility
One of the most significant benefits of mobile screens on tracks is their mobility. Mining operations are often spread out over large areas, and these machines can be easily relocated to different sites or work areas without requiring disassembly or major setup. This mobility reduces downtime and enhances the operational efficiency of mining activities.
b. Reduced Material Handling Costs
With mobile screens, materials can be screened and sorted directly at the mining site, eliminating the need for extra transportation to fixed screening locations. This reduction in material handling costs can significantly impact the overall profitability of the operation.
c. Versatility in Material Processing
Mobile screens are highly versatile and can handle a wide variety of materials, from coarse rocks to fine gravel. This versatility allows mining operations to adapt the machine to different stages of the extraction and processing workflow, increasing its utility across various applications.
d. Quick Setup and Tear Down
Compared to stationary screening systems, mobile screens on tracks have a quick setup and tear-down process. This feature allows mining operations to start screening materials with minimal delay, improving productivity and minimizing the time required for equipment relocation.
e. Optimized Screening Performance
With adjustable screen settings, speed controls, and vibration mechanisms, mobile screens offer optimized performance tailored to the specific material being processed. This capability ensures that miners achieve high-quality output, maximizing the recovery of valuable materials.
f. Safety and Remote Operation
The ability to operate mobile screens remotely increases safety in mining environments, which are often hazardous. Remote controls reduce the need for operators to be physically near the equipment, minimizing the risk of injury from heavy machinery.
Challenges and Considerations
While mobile screens on tracks offer significant advantages, there are a few considerations to keep in mind:
a. Fuel and Power Efficiency
Mobile screens often run on diesel engines, which means fuel consumption is a key factor to consider. Proper maintenance and selecting the right size of mobile screen can help manage fuel efficiency, but operational costs may be higher in remote areas with limited access to fuel.
b. Terrain Limitations
Although these machines are designed for rugged terrains, extreme conditions such as steep slopes or very soft ground can pose challenges for mobility and stability. Ensuring that the machine is operating within its optimal range is essential for safe and efficient use.
Mobile screens on tracks have proven to be a game-changer in the mining industry, offering flexibility, mobility, and efficiency in material screening processes. With their ability to navigate challenging terrain, handle large volumes of material, and reduce the need for fixed infrastructure, mobile screens enhance productivity while lowering operational costs.
As mining operations continue to evolve, the demand for versatile and mobile equipment will only grow. By integrating mobile screens on tracks into mining operations, companies can achieve more streamlined and adaptable material processing, ultimately improving output and profitability in this highly competitive industry.