Other Non-metals
Last Updated :2023-10-13 Views:374
Cost for mini plant cement Grinding Plant factory construction
Setting up a small-scale cement grinding plant involves various costs and considerations. The construction of such a facility requires meticulous planning to ensure its efficiency, safety, and profitability. In this article, we will delve into the key components that contribute to the construction costs of a small cement grinding plant.
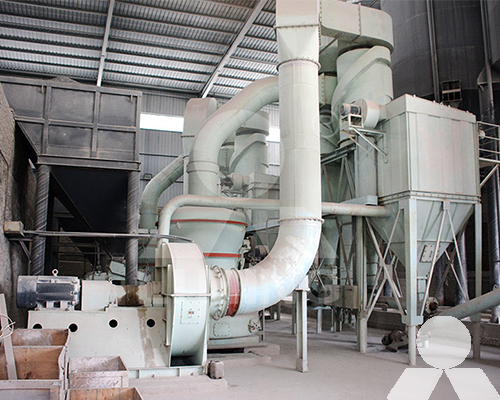
- Land Acquisition and Preparation
The first step in establishing a cement grinding plant is acquiring suitable land. The location should be chosen strategically, taking into account proximity to raw material sources, transportation facilities, and target markets. The cost of land can vary significantly depending on the region and local real estate market conditions. - Infrastructure and Utilities
Once the land is secured, you will need to invest in basic infrastructure and utilities such as road access, water supply, and electricity. Building roads, installing water systems, and connecting to the electrical grid can be a substantial upfront cost. - Plant Design and Engineering
The design and engineering of the cement grinding plant is a critical phase. It includes designing the layout of the facility, specifying the machinery, and planning for safety and environmental compliance. Hiring experienced engineers and consultants is essential for ensuring a well-optimized and compliant design. - Machinery and Equipment The heart of any cement grinding plant is the machinery and equipment used to crush and grind the raw materials into the desired product. This includes crushers, mills, conveyors, and various auxiliary equipment. The cost of these machines can vary significantly based on their size, capacity, and quality.
- Construction and Labor Costs
The actual construction of the facility, including the erection of structures, installation of equipment, and associated labor costs, is a major expense. Skilled labor is often needed for concrete work, steel structures, electrical installations, and plumbing. - Environmental and Regulatory Compliance
Adhering to environmental regulations and obtaining necessary permits and licenses can add to the overall costs. Pollution control measures, waste disposal systems, and other environmental considerations must be addressed. - Raw Material Storage and Handling
In addition to the grinding machinery, the plant will need adequate storage facilities for raw materials, such as limestone, clay, and additives. Conveyor systems, silos, and storage structures are necessary to ensure a steady supply of materials. - Quality Control and Testing
Quality control laboratories and testing equipment are vital to maintaining product quality. These facilities ensure that the cement produced meets the required standards, and their setup costs should be considered. - Administrative and Office Facilities
Office spaces, administrative buildings, and employee amenities are often required for managing day-to-day operations and supporting the workforce. - Contingency and Miscellaneous Costs
Finally, it’s crucial to set aside a contingency fund for unexpected expenses that may arise during the construction process. Miscellaneous costs, such as insurance, safety measures, and initial working capital, should also be considered.
The construction of a small-scale cement grinding plant involves a diverse range of expenses. The overall cost can vary greatly depending on location, scale, and the quality of machinery and facilities chosen. Careful planning and budgeting are essential to ensure that the plant is built efficiently, complies with regulations, and ultimately becomes a profitable venture.