Daily production 2000 tons of cement clinker dry production line
In the realm of modern construction, cement is the fundamental ingredient that binds structures together. The manufacturing of cement clinker is a vital step in the cement production process, and one of the most efficient methods is the dry process. This article delves into the operations of a 2,000-ton-per-day dry process cement clinker production line, highlighting the key stages and the technology that drives this massive operation.
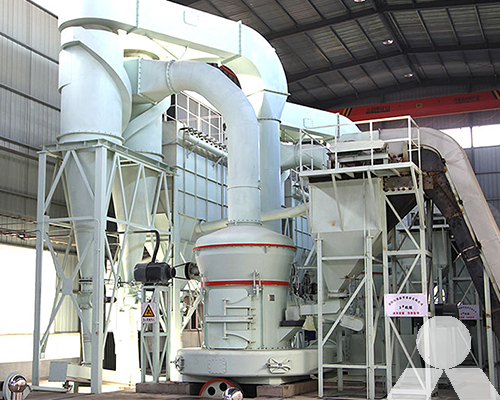
Raw Material Preparation
The journey of cement production begins with the extraction and transportation of raw materials. In the case of a dry process production line, limestone and clay are the primary ingredients. These raw materials are quarried, crushed, and blended in precise proportions to form the “raw mix.” This mix is then conveyed to the next stage for further processing.
Pyroprocessing
The heart of the production line lies in the pyroprocessing unit, where the raw mix is subjected to high temperatures to produce clinker. The key equipment in this unit includes a preheater, a rotary kiln, and a clinker cooler. Here’s a simplified overview of the process:
- Preheater: The raw mix enters the preheater, where it is preheated using the hot gases from the kiln. This preheating step not only saves energy but also helps to reduce the moisture content in the raw mix.
- Rotary Kiln: The preheated raw mix enters the rotary kiln, a massive cylindrical structure, where it is exposed to temperatures exceeding 1,400°C. This intense heat causes chemical reactions, transforming the raw mix into clinker nodules.
- Clinker Cooler: The hot clinker emerging from the kiln is rapidly cooled in the clinker cooler. This cooling process is crucial to maintaining the quality of the clinker and ensuring its proper storage and handling.
Clinker Grinding
Once the clinker is cooled, it is transported to the grinding mill. Here, gypsum is added to control the setting time of the cement. The clinker is finely ground to produce cement powder, which is then stored in silos.
Quality Control
Quality control is paramount in cement production. Throughout the entire process, samples are collected and tested to ensure that the product meets the required specifications. Factors such as clinker composition, fineness, and setting time are carefully monitored.
Environmental Considerations
Modern cement production lines prioritize environmental sustainability. Dust collectors and gas cleaning systems are employed to capture and treat emissions, ensuring that the plant operates in compliance with environmental regulations.
A 2,000-ton-per-day dry process cement clinker production line is a marvel of engineering and technology, producing the essential building material for countless construction projects. From raw material preparation to clinker grinding, each stage is meticulously controlled to ensure the quality and efficiency of the process. Furthermore, the commitment to environmental responsibility underscores the importance of sustainable cement production in today’s world.