Kaolinite Process Equipment
Kaolinite, a clay mineral rich in aluminum silicate, is a key industrial material used in the production of ceramics, paper, rubber, paints, and many other products. The processing of kaolinite requires a series of equipment and procedures to extract the pure mineral from raw kaolin ore and prepare it for commercial use. This article provides an overview of the typical equipment used in kaolinite processing, from extraction to refining.
1. Extraction Equipment
Kaolinite mining usually begins with the extraction of raw kaolin ore from open-pit mines. The extraction process involves breaking up the ore and removing it from the deposit using:
- Excavators and Front Loaders: These heavy machines are used to remove the overburden (topsoil and subsoil) and extract the raw kaolin ore from the mine.
- Draglines: In larger kaolin mines, draglines may be used to remove layers of overburden and expose the ore beneath.
- Blasting: In some cases, blasting is used to fracture and loosen hard kaolin deposits, making it easier to excavate.
2. Crushing and Grinding Equipment
Once the kaolin ore is extracted, it is processed to reduce its size and prepare it for further processing. The first stage of kaolinite processing involves crushing and grinding the raw ore to obtain particles of uniform size.
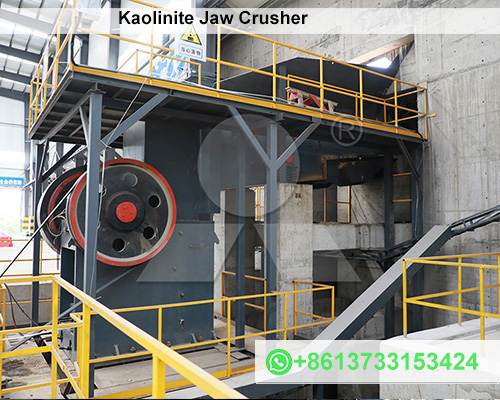
- Jaw Crusher: A jaw crusher is often used as the primary crushing equipment for reducing large kaolin ore chunks into smaller pieces.
- Hammer Mill: In some cases, hammer mills or impact crusher is used to further reduce the size of the material.
- Ball Mill: After crushing, the kaolin ore is often ground in a ball mill to create a fine powder. This is essential for liberating the kaolinite particles from impurities like quartz, feldspar, and other minerals.
3. Screening and Classification Equipment
After grinding, the next step is separating kaolinite from other impurities using screening and classification equipment.
- Vibrating Screens: These are used to classify kaolin particles by size, ensuring only particles within the desired range are sent for further processing.
- Hydrocyclones: Hydrocyclones are used to separate finer particles from coarser particles in a slurry. The kaolin slurry is fed into the cyclone, where centrifugal force pushes the coarse particles to the walls, allowing the finer kaolinite to remain in the center and exit from the top.
4. Washing and Desanding Equipment
Kaolinite often contains impurities like sand and silt that need to be removed. This process is achieved through washing and desanding.
- Scrubbers: Scrubbing machines are used to wash and agitate the kaolin ore, removing unwanted clay particles and freeing the kaolinite from associated impurities.
- Desander/Desilting Units: After washing, desanders or desilting units are employed to remove coarse particles, ensuring that the kaolin remains clean and free of abrasive materials.
5. Flotation Equipment
Flotation is used when fine impurities, such as iron oxides and organic matter, need to be separated from kaolinite. In this stage, chemicals are added to the slurry, allowing kaolinite to float and impurities to settle.
- Flotation Cells: The kaolin slurry is introduced into flotation cells, where air bubbles attract the kaolinite and lift it to the surface. The impurities sink to the bottom and are discarded. The floated kaolinite is skimmed off and sent for further processing.
6. Magnetic Separation Equipment
For kaolin that contains magnetic minerals like iron oxides, magnetic separation is used to purify the material.
- High-Intensity Magnetic Separators: These devices generate strong magnetic fields to attract and remove magnetic impurities from the kaolinite. The kaolinite particles, being non-magnetic, pass through while the iron impurities are captured by the magnetic field.
7. Calcination Equipment
In some cases, calcination (heating) is used to alter the physical and chemical properties of kaolinite, improving its whiteness and strength. This is especially important for high-grade kaolinite used in the paper and ceramics industries.
- Rotary Kilns: Kaolinite is fed into a rotary kiln where it is heated to temperatures between 500°C and 900°C. This process removes water from the mineral structure and enhances its brightness.
- Flash Calciners: These are more advanced and energy-efficient calciners used for rapid heating of kaolin in a short residence time.
8. Filtration and Drying Equipment
After processing, the kaolinite slurry must be dewatered and dried to produce a powdery product.
- Filter Presses: Filter presses are used to remove water from the kaolinite slurry by applying high pressure. The filtered cake is then ready for drying.
- Rotary Dryers: Rotary dryers or fluid bed dryers are employed to remove any remaining moisture from the kaolin, producing a fine, dry powder that is ready for packaging.
9. Packaging and Storage Equipment
Finally, the processed and purified kaolinite is packaged for shipment or storage.
- Bagging Machines: These machines are used to fill bags with the finished kaolin powder for distribution. The size of the bags can vary depending on customer requirements.
- Silos and Storage Bins: Large quantities of kaolin can be stored in silos or bins for future use. These storage units are designed to keep the material dry and free from contamination.
10. Conclusion
Processing kaolinite involves several stages, each requiring specialized equipment designed to extract, purify, and refine the mineral. From crushing and grinding to washing, classification, flotation, and calcination, each step is critical in producing high-quality kaolin for industrial applications. The choice of equipment depends on the specific properties of the raw kaolin ore and the desired end product, whether it’s for ceramics, paper, or other industries. With modern processing technology, the purity and performance of kaolinite can be maximized to meet the demands of a variety of sectors.