Gyratory Cone Crusher Technical Specification
The gyratory cone crusher is an advanced piece of equipment primarily used in mining and large-scale quarrying for crushing hard materials such as ore and rocks. It is favored for its ability to handle high volumes of material with consistent, reliable performance. Combining the functionality of a gyratory crusher and a cone crusher, it ensures efficient primary and secondary crushing, making it an integral part of industrial and mining processes. This article delves into the technical specifications of gyratory cone crusher, offering insights into their design, working principles, and performance features.
Understanding Gyratory Cone Crusher
A gyratory cone crusher is a combination of a gyratory crusher’s high capacity and a cone crusher’s secondary and tertiary capabilities. The core crushing mechanism consists of a conical head that gyrates within a concave bowl, creating a compression action on the material fed into the crusher. The result is fine-grained, evenly crushed material.
This crusher design is ideal for large, hard-to-break materials like granite, basalt, iron ore, and other hard stones. Its application is extensive, spanning mining, aggregate production, and other heavy-duty crushing needs.
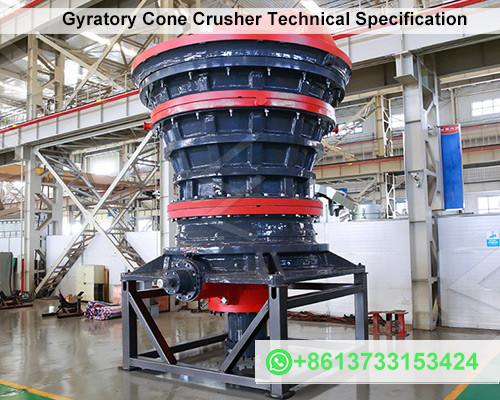
Technical Specifications of Gyratory Cone Crusher
Here’s a comprehensive breakdown of the key technical parameters that define the performance of gyratory cone crusher:
1. Crushing Capacity
- Primary Capacity: Gyratory cone crusher can handle large feed sizes and volumes, with capacities ranging from 100 to over 5,000 tons per hour (tph), depending on the size of the machine.
- Secondary/Tertiary Capacity: For finer material production, these crusher can process up to 1,000 tph in secondary or tertiary crushing stages, providing flexibility in material processing.
2. Feed Opening Size
- The feed opening typically ranges from 150 mm to over 1,500 mm, allowing the crusher to accept large, coarse feed materials. A wider feed opening enhances the crusher’s ability to take in oversized material, reducing the need for pre-processing.
3. Crushing Chamber and Angle
- The crushing chamber is designed to apply maximum force to the material. It is adjustable to various profiles depending on the desired output size. The crushing angle is another important parameter, typically between 20° and 35°, ensuring an effective balance between throughput and reduction ratio.
- A steeper crushing angle produces finer product granules, while a flatter angle can increase capacity but may reduce the degree of material fragmentation.
4. Reduction Ratio
- The reduction ratio is the ratio of the input material size to the output material size. Gyratory cone crusher typically offer a reduction ratio between 4:1 and 7:1, meaning large feed materials can be reduced to much smaller particle sizes in a single pass.
5. Power Requirements
- Depending on the size and model, gyratory cone crusher usually require drive motors in the range of 200 to 1,200 kW (kilowatts). These high-power motors allow the machine to crush very hard, tough materials efficiently and continuously over long periods of time.
- Energy efficiency is a critical factor, and modern designs integrate advanced motor technologies that optimize energy consumption.
6. Mantle and Concave Design
- The mantle (the conical head) and concave (the stationary outer surface) are the primary components responsible for the actual crushing. These parts are made from durable, wear-resistant materials like manganese steel, providing longevity and resistance to abrasion.
- Mantles and concaves are available in different profiles and alloy compositions, depending on the type of material being crushed and the desired output.
7. Automation and Control Systems
- Modern gyratory cone crusher feature advanced automation systems that monitor operational parameters in real-time. These systems control aspects such as the hydraulic setting adjustment, lubrication, and overload protection.
- The inclusion of features like automated gap settings and real-time monitoring helps improve operational efficiency and reduces machine downtime due to manual adjustments.
8. Adjustable Discharge Setting
- The discharge setting can be adjusted hydraulically, allowing operators to fine-tune the product size. Depending on the model, the discharge setting can be adjusted from as low as 10 mm to over 300 mm, making the gyratory cone crusher highly versatile for various material specifications.
9. Frame Design and Durability
- Gyratory cone crusher have a robust and heavy-duty frame construction, typically made of high-strength steel. This ensures the crusher can withstand significant mechanical forces, vibrations, and material loads.
- The design typically includes an oversized main shaft, ensuring structural integrity and longevity under high pressure and stress.
10. Lubrication and Cooling Systems
- These crusher use advanced lubrication systems to ensure that internal moving components, such as the eccentric and bearings, are constantly lubricated. This reduces wear and friction, enhancing machine efficiency.
- For high-power machines, cooling systems are often integrated to dissipate heat generated during the crushing process, preventing overheating and ensuring reliable long-term performance.
Key Features of Gyratory Cone Crusher
- High Capacity: Capable of handling extremely large volumes of material, making them suitable for primary and secondary crushing in large-scale operations.
- Efficient Crushing Mechanism: The gyratory motion ensures continuous and consistent crushing performance, reducing material clogging and increasing throughput.
- Adjustability: Gyratory cone crusher allow for easy adjustment of the crushing gap and product size, providing flexibility for various applications.
- Durability and Reliability: Built with high-grade materials, these machines are designed for long-term use, even in harsh mining environments.
- Low Operating Costs: Automation, advanced lubrication, and energy-efficient design reduce the overall operational costs of the gyratory cone crusher, making it a cost-effective choice for industries.
- Versatility: Suitable for crushing a wide range of materials, from softer aggregates to harder ores and minerals.
Applications of Gyratory Cone Crusher
- Mining: Used extensively in mineral processing plants, gyratory cone crusher is effective in crushing ores and other materials in primary or secondary stages.
- Aggregates: Gyratory cone crusher is ideal for producing high-quality aggregates for road building, concrete, and other construction projects.
- Cement Production: In the cement industry, they are used for reducing limestone and other raw materials to prepare for grinding.
- Metal Recycling: These crusher can also be employed to crush recycled metal and scrap materials, offering efficient recovery processes.
Conclusion
The gyratory cone crusher combines high capacity with precision crushing to meet the demands of modern mining and construction industries. Its technical specifications, including large feed size capacity, adjustable discharge settings, high reduction ratios, and advanced automation, make it an indispensable piece of equipment for heavy-duty crushing tasks. By offering enhanced durability, efficiency, and flexibility, gyratory cone crusher ensure optimal performance in various industrial applications, from mining to aggregate production.