Procedure commissioning of the cement rotary kiln in details
The rotary kiln is a critical component in cement manufacturing, transforming raw materials into clinker which is then ground to produce cement. The commissioning of a cement rotary kiln is a meticulous process that ensures the equipment is fully functional and ready for production. This article outlines a detailed procedure for commissioning a cement rotary kiln, shedding light on the steps necessary to bring this pivotal equipment online.
Documentation: Acquire and review all necessary documents such as equipment manuals, design specifications, and installation instructions. Understanding the design and operational parameters is critical for successful commissioning.
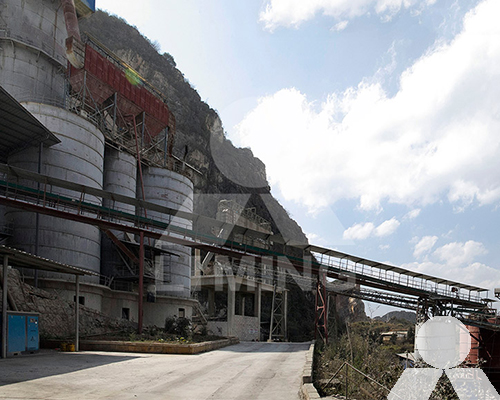
Installation Verification: Ensure that the kiln installation conforms to the design specifications. Check the alignment, level, and the structural integrity of the kiln and its support components.
Equipment Inspection: Thoroughly inspect all auxiliary systems including the drive system, lubrication, seals, and refractory lining to ensure they are properly installed and functional.
Dry Run: Conduct a dry run of the kiln without material to check the rotation, drive system functionality, and to identify any abnormal vibrations or noises.
Control System Testing: Test the control systems, sensors, and actuators to ensure they are calibrated and functioning as per the specifications.
Safety System Verification: Validate the safety systems including emergency shutdown mechanisms, fire suppression systems, and other safety interlocks.
Cold Commissioning: Operate the kiln at low temperatures to cure the refractory lining. This step is crucial for ensuring the longevity and efficiency of the refractory material.
Hot Commissioning: Gradually increase the temperature of the kiln to operational levels, monitoring the equipment parameters and making necessary adjustments to ensure optimum performance.
Initial Material Loading: Load a small quantity of raw material and monitor the kiln’s performance. Assess the temperature profiles, material flow, and clinker quality.
Adjustments: Make any necessary adjustments to the feed rate, temperature, and air flow to ensure the desired clinker quality and kiln performance.
Data Collection and Analysis: Continuously collect and analyze data on kiln performance, clinker quality, and emissions to assess the kiln’s operational efficiency.
Fine-tuning: Fine-tune the operational parameters to achieve the desired performance and efficiency.
Operator Training: Train the operators on the proper operation, maintenance, and safety procedures for the kiln.
Documentation Handover: Handover all documentation including operational manuals, maintenance schedules, and commissioning reports to the plant personnel.
Performance Review: Conduct a thorough review of the kiln’s performance over a specified period.
Maintenance Planning: Establish a maintenance plan based on the manufacturer’s recommendations and the observed performance.
In conclusion, commissioning a cement rotary kiln is a complex procedure that requires a detailed and systematic approach. Through meticulous preparation, rigorous testing, and continuous monitoring, the kiln can be commissioned successfully, paving the way for efficient and sustainable cement production. The knowledge and expertise gained from the commissioning process are invaluable for ensuring the long-term operational efficiency and reliability of the cement rotary kiln.